Makino Establishes Global Titanium R&D Center, Offers Horizontal Machining Series with ADVANTiGE
Makino’s Mason, OH, facility has been designated Makino’s Global Titanium Research and Development Center, where a specialized group of engineers will further the development of titanium milling technologies. The facility includes state-of-the-art machine tools, specialized titanium machining and tooling experts, CMM equipment, and all the necessary tools and talent to further titanium machining technologies.
“Titanium machining is very process driven, meaning the machine tool, cutting tools, machining process, and coolants must all be developed and integrated specific to titanium’s material properties,” says Tom Clark, vice president of Makino. “Our mission at Makino’s Global Titanium R&D Center is to provide manufacturers with the best in titanium application expertise by combining Makino’s titanium machining capabilities with the world’s leading process technologies. This is an ideal opportunity to work with vendors, suppliers, and partners to develop improved metal removal rates with longer tool life in titanium milling.
“The Mason, Ohio facility was chosen based on the increasing importance of titanium in the aerospace industry which is centralized in North America. Our past experience in aluminum aerospace applications, and grinding of hard metals, will serve as an advantage to the continued development of titanium aerospace processing techniques.”
Makino’s Global Titanium R&D Center will be managed by a select group of engineers with knowledge and experience around titanium in both academic and industrial backgrounds. The group will be working with tooling and consumable vendors from around the world for a wide knowledge base in all types of titanium applications.
Titanium Machinery
Makino’s Global Titanium R&D Center features a variety of machining platforms, including horizontal machining centers, vertical machining centers, 5-axis machining centers, and wire and ram EDMs. Currently installed equipment includes a Makino a81M horizontal machining center, D500 5-axis vertical machining center, EDGE3 ram EDM with Titanium Booster technology, and Makino’s latest T2 and T4 5-axis horizontal machining centers. T-series machines are built specifically for titanium aerospace parts and are the first to include ADVANTiGE technologies. The first machines in Makino’s T-series include the T4 and T2 5-axis horizontal machining centers. The larger T4 provides X, Y, and Z axis travels of 4,200mm, 2,000mm, and 1,000mm, respectively, and can hold workpieces up to 5,000kg. For smaller aerospace components, the T2 provides X, Y, and Z axis travels of 2,000mm, 2,000mm, and 1,800mm, respectively, and can hold workpieces up to 5,000kg.
“Makino’s ongoing titanium research and development continues to offer the most effective process solutions for a wide variety of today’s aerospace structural and engine components,” says Mark Larson, Makino’s titanium process R&D manager.
Unattended Machining
The T2 includes an automatic pallet changer system that features continuous operation and eliminates costly downtime for part changeovers with pallet change times of only 60 seconds. This machine can also be integrated with an automatic pallet transfer and storage system in a highly flexible Makino Machining Complex (MMC) for extended periods of unattended operation. This automation system assigns work and initiates operations, automatically, maximizing spindle utilization. makino.com
Open House, 10 Year Anniversary
Handtman CNC Technologies, E. Dundee, IL, celebrated their 10-year anniversary with an open house during the week of June 6, 2011. The two-day event highlighted the HBZ CompactCell, presented with one of the various automated solutions for the very first time.
During the open house, presentations by experienced German and American Handtmann employees, as well as several suppliers, occurred throughout the event. The 10-year success of the American subsidiary demonstrates the importance of an on-site-presence in international markets for manufacturers of HSC-machining centers. handtmanncnc.com
Complete Success: Facility Obtains AS9100/ISO 9001:2008 Cert.
Build-A-Quote Provides Multiple Options
The Build-A-Quote system from Haas Automation, takes open pricing a step further by allowing customers to select and configure a machine, add options and accessories, and then generate a detailed custom quotation.
Build-A-Quote is easy to navigate, and accessible via the computer, tablet, or smart phone. The systematic process allows the customer to generate an accurate price quote for a new turning center, vertical machining center, or horizontal machining center. The completed quote can then be printed, or sent electronically to the local Haas Factory Outlet for follow-up.
To help customers make informed selections, the Haas website offers easy access to machine specifications, descriptions, and images, as well as links to cutting videos and the Haas information blog. Potential buyers can compare specs, side-by-side, and then select the combination of available options and accessories best suited for their operation. haascnc.com
Establishing an Aerospace Division
OSG Tap & Die has recently established an aerospace division that is 100% dedicated to the manufacturers of the aerospace industry. Nicknamed the A Team, this new division allows OSG to seamlessly communicate across the research, development, and sales channels to provide the best engineered solutions for the most difficult machining challenges in today’s aerospace market.
All of OSG’s aerospace tooling feature exclusive metallurgy and cutting geometries to help increase productivity, reliability, and tool life, while reducing machining time and scrap. OSG also offers a patented ultra-fined diamond coating, which is a prerequisite when machining composites.
OSG’s aerospace division released a new product brochure featuring numerous state-of-the-art composite solutions earlier in the year. A new catalog dedicated entirely too aerospace tooling is scheduled to be released this autumn. osgtool.com
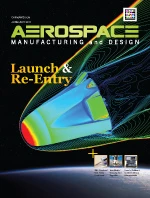
Explore the July 2011 Issue
Check out more from this issue and find your next story to read.
Latest from Aerospace Manufacturing and Design
- Ralliant to establish global headquarters in North Carolina
- Philatron MIL-DTL-3432 military cables
- Beyond Aero refines its hydrogen-electric light jet
- Americase's advanced protective solutions
- Social media - what are your thoughts
- GE Aerospace secures Air Force engine contract
- Thomson Industries' online sizing and selection tool
- #53 - Manufacturing Matters - 2024 Leaders in Manufacturing Roundtable