Thermal Protection Systems (TPS) have played a critical role in reusable vehicle designs since NASA engineers first began work on the Space Shuttle in 1972. Before that, with disposable space capsules, Mercury, Gemini, and Apollo – use of ablative materials were to absorb heat energy and then dissipate it through vaporization. To accommodate multiple missions, such as with the Shuttle, TPS designs took a different tack, utilizing a variety of materials (flexible insulation blankets, composites, ceramic tiles, and others) to protect the craft and its occupants from the extreme heat of re-entry. However, since the Columbia accident in 2003, engineers have been particularly motivated to find designs that are more durable.
Since the mid-1990s, Dutch Space, Leiden, Netherlands, a supplier of high quality subsystems and products for the international space industry, has been a key player in the development of metallic TPS and hot structures for reusable craft. The metallic TPS of the European Experimental Re-Entry Testbed (EXPERT), an unmanned capsule developed by the European Space Agency and the prime contractor, Thales Alenia-Space of Italy, is one of Dutch Space’s latest efforts (photo page 58). It is pending launch from a Russian submarine aboard a three-stage Volna rocket in the summer of 2011, and promises validation, not only of new materials, but also of simulation as an integral tool in the development process.
Tale of Two Materials
ESA is preparing new launch systems to respond better to Europe's future institutional needs and to continue at the forefront of new developments in space. Photo courtesy European Space AgencyFrom the start, Dutch Space has focused on the use of metallic materials for TPS designs. According to Javad Fatemi, technical leader of the EXPERT’s TPS project, metals have a lot of advantages over ceramics.
“Metals are easy to use and maintain,” Fatemi says. “They can handle impacts much better, and inspection is easier.”
However, on the negative side, metals are heavier than other materials and cannot cope with high temperatures as well as ceramics. Therefore, to take maximum advantage of material properties, Fatemi is betting on a TPS, which uses a combination of metallic and ceramic parts.
The thermal protection system, EXPERT, which measures approximately 5ft high, 4ft in diameter, is comprised of two major components. First is a nose cap made of a ceramic matrix composite (CMC), which takes the brunt of the thermal load during re-entry, and second is a conical metallic after-body manufactured from an oxide dispersion strengthened alloy, PM1000. They chose these two materials for their high-temperature stability and weight efficiency. Four flaps that protrude from the surface at the base of the vehicle are also made of the more heat-tolerant CMC.
“We could not make the whole craft out of metal,” Fatemi says, “because the temperature is roughly 1,900°C at the nose and 2,050°C at the flaps, which are both higher than the 1,200°C to 1,250°C limit for the metal.”
However, while providing material advantages, a two-part, two-material design also introduced the project’s greatest design challenge: The thermal expansion of the metal is eight times greater than that of the ceramic.
The European Experimental Re-Entry Testbed (EXPERT), an unmanned capsule developed by the European Space Agency, utilizes a hybrid thermal protection system (TPS) comprised of a ceramic matrix composite (CMC) blunt nose and a metallic conical after-body. Four CMC flaps are installed on the flat parts of the metallic TPS. The TPS accommodates sensors for aerothermodynamic measurements. All electronics are housed on the cold structure, which will be shielded from the extreme heat of atmospheric re-entry by the TPS. Photo courtesy European Space Agency“At the junction between the nose cap and the after-body, we had this huge thermal mismatch,” Fatemi says.
If the shape of the vehicle was to change during re-entry from the thermal mismatch – even just slightly – it could alter the flow from laminar to turbulent and, as a result, increase heat flux by a factor of two to three.
The solution was a structure that bridges the two components while allowing for differential heat expansion.
“We needed to design the TPS so that we were sure it wouldn’t trigger turbulence,” Fatemi explains. “Simulation was key to solving that problem.”
Realistic Simulation
When Fatemi joined Dutch Space’s EXPERT team in 2004, one of his first tasks was to compare commercially available finite element analysis (FEA) software that is used for simulating structural and thermal behavior. After conducting a tradeoff study, his reasons for selecting Abaqus FEA from SIMULIA, the Dassault Systèmes brand for realistic simulation, were clear.
“For one,” Fatemi says, “with Abaqus, you have a unified finite element (FE) model. That means if you want to create both a thermal and a structural model, you can use the same mesh and easily change the element type and the boundary conditions.”
“We imported the CATIA model directly into Abaqus CAE to make the FE model,” Fatemi states. “Every time we made a revision based on our analysis, the CATIA model would automatically update.”
Abaqus could also handle the complexity of the highly nonlinear TPS simulation with its robust interface between the pre- and post-processors and the solver. “The contact and specialized mechanisms, like special joints on the flaps, were all easy to model,” Fatemi says. “With Abaqus, we are able to closely simulate reality.”
The extreme in-flight forces that EXPERT encounters are a variety of thermal and mechanical loads. During the launch, it will experience acceleration, random vibration, and acoustic and shock loads. During re-entry, it will be subject to severe aerodynamic heating and aerodynamic forces. In addition, there is the shock of impact when it comes back to earth, landing on the Kamchatka peninsula.
To accommodate the multiple physics that the vehicle is subjected to, Fatemi developed both 3D structural and 3D thermal models. He used the structural model to analyze the stiffness, strength, and thermo-mechanical behavior of the TPS when subjected to launch, aerodynamic heating, and pressure loads. In this model, taken into account all non-linearities – geometrical, materials, and boundary conditions – and the mechanical properties of all materials were treated as temperature dependent. The model used four-node linear quadrilateral shell elements (S4R), with each element having six degrees-of-freedom (DOF) per node (three translations and three rotations).
Use of the thermal model was to estimate the temperature histories for all TPS parts, as well as payloads. This model was constructed from four-node, heat transfer quadrilateral shell elements (DS4) with DOF represented as temperature; it had a total of 112,994 elements and 128,358 nodes.
In the most recent analyses, Fatemi used CATIA V5 and Abaqus V6.10. Because of analysis complexity, he ran them on a high-performance Linux-based compute cluster for parallel computing – an Abaqus-compatible hardware configuration.
Analyzing Loads

To ensure that the vibrations of launch do not occur at the vehicle’s resonant frequencies, which can accentuate stresses, Fatemi carried out a normal mode analysis using the structural model. The requirement for minimum eigen frequency for the EXPERT was set at 80Hz. The minimum value reached during analysis was 86Hz, falling within specification.
Performance of a non-linear static strength analysis was to verify the structural performance of the TPS during launch. This analysis indicated that maximum loads occur during the separation of the second and third stages of the rocket and that during this event all EXPERT components had positive Margins of Safety (MS).
Re-Entry Challenges
While launch will generate harsh loads on the EXPERT, it is during re-entry that extreme thermal and mechanical loads really rest the vehicle. As the approximately half-ton vehicle slams into a wall of air at 14 times the speed of sound, it generates tremendous kinetic energy. According to basic physical principles, this energy translates into heat: when friction from the air slows the craft, its surface heats up, as governed by the relationship between airflow and heat flux (see Sidebar). The 150-second re-entry window officially begins when the 436kg (961 lb) craft is at an altitude of 104km (64.6Mi) and first encounters the atmosphere. Velocity at that time will be 5km per second (11,184mph), with an entry path angle of -5.5°.
To simulate the aerodynamic heating of the EXPERT, a computational fluid dynamics (CFD) code, called Lore – developed by a student at Delft University of Technology – was used to calculate spatial distributions of heat flux over the vehicle’s outer surface at five discrete speeds (between Mach 18 and Mach 10) on the re-entry trajectory (see page 62). The heat flux distributions were then directly mapped from the CFD mesh to the thermal FE mesh in Abaqus using a dedicated sub-routine developed at Dutch Space. The stagnation heat flux profile was used to interpolate the spatial distribution of heat flux between different Mach numbers. Spatial distributions of dynamic pressure (at the same five trajectory points) were also calculated using CFD and mapped in the same way.
During re-entry, aerodynamic heating and dynamic pressure create severe loads on the TPS, dependent on vehicle shape, atmospheric density, and speed. In addition, as the temperature increases, the mechanical properties of TPS materials degrade. To measure these effects, Fatemi used a sequential thermo-mechanical analysis, which predicted the temperature history in the EXPERT’s TPS and payload, and generated maximum temperatures for each of the three critical EXPERT structures at specific times during re-entry: CMC nose (2,165K at 102 sec), CMC flaps (2,328K at 95 sec), and metallic after-body (1,464K at 112 sec).
The thermo-mechanical analysis also calculated the effects of the thermal mismatch between the composite nose and the metallic conical structure, generating gap (axial displacement) and step (radial displacement) measurements. Gap evolution is important in determining the design of the seals between the nose and the TPS, while the step values guarantee that changes in surface geometry will not trigger turbulent flow during re-entry. In both cases, analysis results fell within specified requirements. In addition, plastic stress/strain and MS – which vary as a function of loads and material temperature for specific parts – were calculated and determined to be within specification.
Confidence is High
As the EXPERT project neared completion, the Dutch Space team took the final step of conducting physical tests to validate the predictions of analysis with actual measurements. In one scenario, Fatemi modeled and tested a highly nonlinear bolt joint at very high temperatures. In another, engineers conducted a dynamic test of the vehicle and compared it with simulation results.
Comparing test and analysis results, accuracy for the bolt joint was within 3% and for the dynamic test within 5%.
“These comparisons gave everyone – the customer, the prime contractor, and Dutch Space – high confidence in the Abaqus FEA results,” Fatemi says. “This is important since budgets were limited, full-scale thermo-mechanical tests are extremely expensive, and the EXPERT is going to fly without any full-scale thermo-mechanical tests.”
The next project for Fatemi will be a complete vehicle analysis of EXPERT in which a CFD aerothermodynamic analysis is coupled with the Abaqus FE model (a first for non-military vehicles). He is also moving on to develop carbon fiber-reinforced polymer (CFRP) engine thrust frame technology for the European Space Agency’s (ESA) next-generation launchers, with FEA slated to play a key role again.
“My objective is to build our capability for virtual testing and replace as much physical testing as possible,” Fatemi says. “With EXPERT, we proved that simulation shortens the time-to-market and reduces costs. We have done all of our design verification using high-fidelity analysis and have confidence in the power of FEA to predict outcomes we can rely on.”
Heat Flux, Air Flow During atmospheric re-entry of spacecraft, heat flux and air flow are inextricably intertwined. Counterintuitively, heat load is inversely proportional to drag – or in other words, the greater the drag, the smaller the heat load. |
Dutch Space
Leiden, The Netherlands
dutchspace.nl
Dassault Systems
Lowell, MA
3ds.com
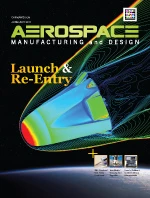
Explore the July 2011 Issue
Check out more from this issue and find your next story to read.
Latest from Aerospace Manufacturing and Design
- Textron Aviation to bring its largest-ever lineup to 2025 EAA AirVenture
- Qualified materials for 3D-printing mission-critical applications
- #69 Manufacturing Matters - Shopfloor Connectivity Roundtable with Renishaw and SMW Autoblok
- Demystifying Controlled Unclassified Information (CUI)
- Simplify your shop floor operations while ensuring quality parts
- Happy Independence Day - July 4th
- Bombardier receives firm order for 50 Challenger, Global jets
- Automatic miter bandsaw