Soaring fuel prices, unrest in oil producing nations, global demand to save the environment, corporate demand to cut costs; these are just some of the forces creating an urgent need for more fuel-efficient turbine engines. While there is immense pressure on design engineers to develop these engines, the heat is on test engineers to create new ways to validate component parts that will run, spin, and vibrate in hotter, harsher turbine engine environments – that could reach more than 2,000°F.
As engines run hotter – and at higher pressures – it extracts more energy from the fuel, which makes the engine more efficient. However, extreme heat and higher running speeds put added stress on blades and rotors, which are demanding new classes of materials. Engine components face stress and degradation through thermal interaction, creep, erosion, vibration, and hot corrosion.
Newer engines will create environments that are hotter and harsher than predecessor models. Testing options that simulate these conditions are attractive to validate the performance of critical components, especially when data for new materials is lacking. Isolating and controlling test conditions are critical in order to gather essential technical data in advance of the test phase of an engine program.
What design engineers create, test engineers and modelers must simulate in order to evaluate the performance of coatings, parts, and materials that will operate in the new world of lighter materials and hotter engines. Test Devices is developing equipment and methodologies that better simulate real world engine conditions.
Some unique test capabilities include high cycle fatigue, radial or axial thermal gradient, radial growth, thermal mechanical fatigue, and strain surveys. The specific range and control of spin testing includes a maximum speed of 160,000rpm, with an accuracy of ±0.01% at maximum speed for over-speed testing and ±1rpm for vibration mode (dynamic spin testing). Drives for speed ranges are 20,000rpm, 30,000rpm, 40,000rpm, 60,000rpm, 100,000rpm, and 160,000rpm.
Model Validation
Historically, engineers and scientists have been able to refer in part to existing bodies of information, models, test results, and field experiences as they refine and modify engine parts. With manufacturers bringing dramatically new components, materials, and coatings to market, there is a limited body of knowledge that scientists and engineers can rely on to confirm their assumptions. One of the best ways for developers to validate their models is through rotational testing.
Managing resonant vibration of compressor and turbine blades presents a technical challenge for jet engine and industrial gas turbine (IGT) programs. Under certain conditions of operation, blades vibrate in response to pulsing flow from upstream stages. If common power settings coincide with blade resonant modes, they can crack and fracture from high cycle fatigue during operation.
Increasingly, engineers are using spin testing to better understand and validate the life and integrity of airfoils and integrally bladed disks. This testing evaluates blade resonance by simultaneously subjecting components to the centrifugal, vibratory, and thermal stresses of an operating engine. Bladed rotor components are tested fully assembled, or with custom designed scaled rotors, in a similar manner as they operate in the engine. The rotor assemblies are accelerated to designated engine speeds while various excitation methods are used to produce resonant blade vibrations that simulate engine blade-to-stator interaction, producing of various bending, torsional, axial, t-shirt, etc. modes.
Blade validation testing under these more realistic end-use conditions better simulates strain gradients, untwist, blade/rotor interaction, etc when compared to current methods such as shaker tables and static tensile testing. Testing can be in ambient or high temperature (isothermal or gradient) conditions. This unique capability has become very beneficial as manufacturers accelerate research and development of high-efficiency engines using new innovative materials.
The specific range and control of spin testing includes a maximum speed of 160,000rpm, with an accuracy of ±0.01% at maximum speed for over-speed testing and ±1rpm for vibration mode (Dynamic Spin Testing). Drives for speed ranges are 20,000rpm, 30,000rpm, 40,000rpm, 60,000rpm, 100,000rpm, and 160,000rpm.
Testing
During dynamic spin testing, high cycle fatigue conditions can be introduced in a very controlled manner for accurate measuring with non-intrusive stress measurement systems. Design of the test system is to dwell at specified resonant frequencies for more than 100 million cycles in order to perform Goodman Validations. By producing realistic resonant vibration, dynamic spin testing can accurately confirm expected modal frequencies. Precise speed control allows for very slow resonance crossings as well. This slow sweep capability helps to initially identify modes, distinguish between coupled modes, accurately measure amplification factors that take time to build, and determine damping (Q factors), – allowing for very effective damping analysis and validation. Finally the ability to hold resonance for long periods of time often results in broken blades, allowing for blade failure analysis, crack growth propagation, and validation of surface treatment and various repair methods.
While dynamic spin testing creates precise simulations, live engine testing remains the most comprehensive method of evaluation; however, it is risky and expensive, costing up to $100,000/hr in operating and staffing charges and, given the harsh operating environment and lack of accessibility, may not provide clean data for component evaluation. An additional problem with engine testing is the danger of damage to the entire engine if an individual component should fail.
Dynamic spin testing can provide critical performance data to speed project completion, reduce total testing costs, and lower the risk of in-service component failure. This form of testing is becoming increasingly critical, in the rush to get new engines through certification as quickly as possible.
Test Devices
Hudson, MA
testdevices.com
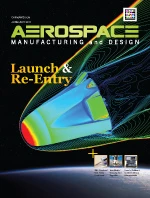
Explore the July 2011 Issue
Check out more from this issue and find your next story to read.
Latest from Aerospace Manufacturing and Design
- Ralliant to establish global headquarters in North Carolina
- Philatron MIL-DTL-3432 military cables
- Beyond Aero refines its hydrogen-electric light jet
- Americase's advanced protective solutions
- Social media - what are your thoughts
- GE Aerospace secures Air Force engine contract
- Thomson Industries' online sizing and selection tool
- #53 - Manufacturing Matters - 2024 Leaders in Manufacturing Roundtable