For assembly lines – of electronic components, passenger seats, or any subassembly – make sure you build in flexibility to incorporate changes later, if needed.
Today’s aerospace industry features a vast array of products and systems, manufactured by thousands of firms – everything from passenger seats to hydraulic and electromechanical flight systems; cockpit electronics to in-flight entertainment platforms; and flight deck tow motors to landing gear and jet engines. To keep aerospace manufacturing lean, flexible, and profitable, how does one ensure that the aerospace workspace – with this much diversity – is outfitted properly to achieve the best result with the least possible waste?
Eliminating Waste
In truth, many companies in the aerospace industry are already executing lean strategies, with good success. The typical low-volume, high-mix product environment in aerospace manufacturing pretty much demands a lean strategy. However, even if you are not extremely well-schooled in lean, a good place to start is to engage your associates in identifying wasteful practices. Even a quick walk through the plant will usually turn up something.
Lean practitioners have identified seven classic types of waste: defects and errors; waiting; inefficient processes; overproduction; excess inventory; wasted motion and movement; and excessive material handling. The most successful companies generally have figured out ways to control waste, and they actively train their employees to recognize it, take action and eliminate it – whether those companies claim to be lean or not. Every plant, regardless of product type, volume, company size, or reputation, has waste.
Many aerospace manufacturing facilities are large, which can lead to lots of wasted motion and movement, as well as excessive material handling.
It may be worth spending a few dollars with a skilled lean consulting firm if you do not have a lot of experience with lean in-house. They can often get you started with the basics in a short period of time. They may have you do a waste walk with your lean leadership team. Take clipboards and notepads, and walk around in specific areas, looking for waste of the seven types mentioned above. You may be surprised at what you find.
Do employees have to take many steps to perform their tasks? Do parts or finished goods, or both, travel significant distances in the plant? If your team identifies waste of this type, then your next step is to dig in further. Take a stopwatch and tape measure with you and follow a process all the way through. The resulting spaghetti diagram will likely offer low-hanging fruit that will allow your team to start re-designing a process right away. In one company, which I am familiar with, one employee was walking nearly 10 miles per day to complete his tasks. Sure, he was lean, but the process was not. Within a month, a few simple decisions and small investments had trimmed his daily walking distance by 89%.
Identify Waste
The most important thing to remember about lean is that it is a manufacturing lifestyle, relentlessly dedicated to the elimination of waste. It is not a fad or a program of the month, and you need to commit to it or you will backslide quickly.
Once you have a feeling for identifying waste, the next step is to take a more systematic look at what you do, for whom you are doing it, and what you think those people are willing to pay for. Value stream mapping works you backwards – from the delivery to the customer through all of the processes in production – helping you identify value–adding processes versus waste along the way. There is no room for conjecture here. If you think a certain process includes waste of any of the seven types, take the time to measure it. Measuring the processes is also a great way to involve associates in the early stages of a lean implementation. Sure, you will have a few who do not like change. However, you will have others who have better ideas about how to do things, and they have been yearning for someone to ask them their opinion. These people are your potential lean evangelists in the plant as the program progresses.
Remember, lean is a culture, and to change a culture you will need change agents. Strong believers in lean on the factory floor will prove to be invaluable.
Excess inventory, both finished and in process, is a key form of waste that needs to be identified and attacked via the value stream map. Charting the build-up of inventory throughout your value stream is critical because you do not want to produce more than your customers need. Again, large factories with a lot of space can fall prey to staging areas everywhere, simply because they have the space to create them. Even if it appears that inventory is simply sitting around, it requires management: checking, moving, accounting, and more. By minimizing waste of one type, you often knock down waste in other areas as well.
Investing in Flexibility
It seems that the last few years have reminded us daily that the only thing constant is change. Yes, it is cliché, but when it comes to manufacturing and assembly, it is a cliché worth paying attention to. Even as you begin to rethink assembly, manufacturing, and material handling processes, you will want to build in the flexibility to make even more changes later.
Simple simulations can often help you prove out some of the proposed changes before you actually start moving workstations and equipment around for real. As long as the parts you are handling are not too heavy, you might even be able to position large shipping boxes upside down as workstations and see how the process flows if you position the different processes in several different ways. It is a great, simple way to work through a process, and often stimulates ideas that you cannot see when you are looking at the process in its current form in the factory.
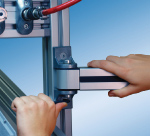
The broad range of sizes among the extruded aluminum elements also accommodates a tremendous range of uses: scaffolds for exterior aircraft assembly processes, roll-around trolleys for airplane seats, and U-shaped or L-shaped lean work cells. Also, new tubular framing systems, some also with a T-slot design, are even lighter in weight and can be cut to length on-site with a chop saw to assemble carts, lightweight benches, and flow racks quickly and easily. In both cases, easy-to-use design software is available that provides a 3D representation of what your finished structure will look like, how much space it will take up, and the parts required to build it. Cutting waste from engineering processes is just as important as cutting waste from manufacturing processes.
If your volumes are high enough that automation is necessary, it is important to build flexibility into your automation processes as well. This might mean that you work with small footprint cell-type automation, or that you consider flexible assembly conveyors based on T-slotted framing instead of high-speed synchronous conveyors made out of steel. Of course, the most important lens through which you should view any equipment purchase is one of waste: Are we creating processes and systems that are the least wasteful over the long term?
Staying on Top
Just as your processes will change constantly to meet customer requirements, you will also want to stay on top of new thinking. You will also need to train people in lean at different levels in order to achieve a common language when talking about processes. Many free resources are available online, with surprisingly detailed information. Bosch Rexroth for example, offers a free lean manufacturing podcast series on their website featuring respected lean practitioners discussing basic lean concepts in 10 minute to 15 minute episodes (boschrexroth-us.com/leanpodcast).
Social media is another area that is becoming extremely valuable in lean circles. LinkedIn is buzzing with activity in lean groups, ranging from company consortiums such as the Lean Factory Group to industry associations, to individual lean consultants. These groups often sponsor webinars, inexpensive hands-on training sessions, white papers, and other lean information. They are great places to share experiences and to pose questions to people who have many years of experience in lean.
Writing any short article on lean is a challenge. The principles do not really change that much, but each factory faces such different challenges that applying those principles always requires customization. By understanding that lean is not a program, but instead a commitment to a culture, you can take the first steps towards productive and positive change.
With the competition we all face in today’s global market, smart deployment of lean techniques is rapidly becoming more than just a foundation for continuous improvement; it is becoming a means to survival. Thankfully, many aerospace companies are well down this path and are leaders in lean thinking. A consistent deployment of lean techniques throughout the industry, however, will help us all benefit from shorter travel distances and lower costs of locally produced, high-quality parts.
Bosch Rexroth Corp.
Hoffman Estates, IL
boschrexroth-us.com
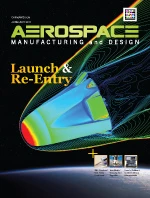
Explore the July 2011 Issue
Check out more from this issue and find your next story to read.
Latest from Aerospace Manufacturing and Design
- Malaysia Aviation Group orders 20 more Airbus A330neo widebodies
- More displacement from space-tested piezo actuators
- Textron Aviation to bring its largest-ever lineup to 2025 EAA AirVenture
- Qualified materials for 3D-printing mission-critical applications
- #69 Manufacturing Matters - Shopfloor Connectivity Roundtable with Renishaw and SMW Autoblok
- Demystifying Controlled Unclassified Information (CUI)
- Simplify your shop floor operations while ensuring quality parts
- Happy Independence Day - July 4th