(top) Using a full feed directly into the workpiece, the insert shows significant wear after just two passes.
(bottom) After 15 passes using the roll-in technique, this insert shows little wear.Programming plays a vital role in a manufacturer’s productivity and profitability. Quite often, companies do extensive research on equipment and adopt the perfect mix of machine tool, cutting tools, and automation components, only to integrate cutting programs that fail to take full advantage of the system’s capabilities. In some of these instances, performance is so poor, that it actually negates any cost benefits that could be derived from investing in the best available technology.
Today’s CAM programmer wields substantial power over a company’s profitability. He selects the machining strategy. He chooses which cutting tools to use. He decides the cutting speeds, feedrates, and depths of cut. He defines the cutting paths. In turn, all of these decisions determine metal removal rates, tool and insert consumption, cycle time of a part, and overall quality. That is an incredible amount of responsibility, yet many manufacturers do not focus on providing their CAM programmers with the necessary array of resources to truly excel in their work.
Technological progress is a constant in today’s market. Innovative products are constantly being released and new theories on cutting processes regularly emerge. Even the brightest and most competent of programmers will soon fall behind their peers if they are limited to the vacuum of their own operations. Ongoing training has never been more important. Perhaps training used to be thought of as a tool for those learning the trade, it is now a necessity for anyone who wishes to keep pace with the current rate of technological development.
The industry reflects the increased importance of ongoing education. Machine tool builders, cutting tool suppliers, software providers, and producers of other interrelated technologies have all made dedicated efforts to expand the training opportunities for their customers. In many instances, companies providing complementary products have partnered to develop courses and seminars that demonstrate how to get the maximum performance out of a total system. Often, these valuable sessions are provided free of charge and anyone in the industry may register and attend. Any manufacturer that fails to send its CAM programmers to these types of learning events is missing out on a valuable opportunity that can significantly impact profitability.
.jpg)
As an alternative to the above process, it is now recommended that CAM programmers create a toolpath whereby the tool rolls into the cut in a clockwise direction. This technique changes the way metal is removed and results in chips that become thinner as the tool moves towards exiting the material. The affect on the process is dramatic.
When cutting nickel and titanium alloys, tests have shown that by rolling into a cut, instead of approaching it head-on, significant tool life and productivity gains are achieved. In many instances, insert consumption can be cut by up to 90%. For certain applications, the savings are even greater.
Additionally, elimination of vibration through the new cutting tool path allows for faster feedrates, and a reduction in cycle time by up to 50%. These are dramatic savings and they arise from a very small change that can often be easily integrated with the appropriate knowledge.
The savings represented above are dramatic, but not atypical of what can be achieved by fine-tuning cutting processes with the latest techniques. Perpetual R&D by providers of all manufacturing components is consistently uncovering new insights that offer companies the chance to improve their profitability and competitive position. Ensuring that its CAM programmers are exposed to these breakthroughs should be a top priority of every aerospace manufacturer.
Sandvik Coromant
Fair Lawn, NJ
coromant.sandvik.com/us
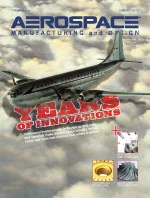
Explore the June July 2010 Issue
Check out more from this issue and find your next story to read.
Latest from Aerospace Manufacturing and Design
- Heart Aerospace relocates to Los Angeles
- Fixtureworks introduces Stablelock Clamps
- Piasecki acquires Kaman's KARGO UAV program
- PI Americas’ long-travel XY piezo nanopositioners-scanners
- AAMI project call submission deadline extended to May 12
- Jergens launches cast iron tooling column additions
- Airbus to acquire assets relating to its aircraft production from Spirit AeroSystems
- FANUC America's Cobot and Go web tool