Unison Engine Components - Asheville was having difficulty generating a consistent chamfer on a specific component used in aerospace manufacturing. Their chamfer lacked accuracy, added time, and compromised the quality of the product being manufactured.
The application was a high pressure Inconel 718 turbine stator that was a blind hole. This challenge became more apparent as measured accuracy was not being achieved at a regular level. The goal was to deburr the top and bottom of the first hole, as well as the top of the second hole, while maintaining a consistent chamfer size of 0.005" to 0.015".
In the past, the customer had been using a hand-made deburring tool driven by a pencil grinder. This operation took way too much time and proved to be very inconsistent – not to mention that it did not garner the results they were required.
The handheld pencil grinder deburring tool was very difficult to use and required that a skilled craftsmen spend more than 30 minutes per part completing this process. This amount of time obviously added to the cost of producing the high-pressure turbine stator.
Due to the fact that this was a unique application, there was not a machined tool to pull from the shelf. Unison Engine Components-Asheville approached E-Z Burr with the challenge to provide a custom-built micro tool to meet their standards and requirements.
E-Z Burr Tool Co. built a custom micro tool to deburr the three surfaces while maintaining a consistent 0.005" to 0.015" chamfer size. They had to also ensure that the arbor pilot length did not damage the blind hole, while still removing the burrs and that it generated a consistent chamfer in the required size range. Design modifications to the arbor and blade were made to achieve the perfect solution.
The tool proved to be successful and delivered the consistency the customer required. In addition, the attention to detail also allowed the avoidance of damage inside the blind hole.
Unison Engine Components-Asheville now has an Inconel 718 component that meets their standards for quality and consistency. They are proud to offer a unique product that may offer increased sales of this component. The timesaving alone added productivity to the manufacturing process, and made producing this component a more profitable operation.
E-Z Burr
Plymouth, MI
ezburr.com
Unison Engine Components
Asheville, NC
unisonenginecomponents.com
Get curated news on YOUR industry.
Enter your email to receive our newsletters.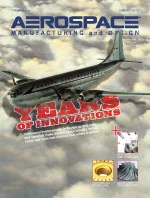
Explore the June July 2010 Issue
Check out more from this issue and find your next story to read.
Latest from Aerospace Manufacturing and Design
- Piasecki acquires Kaman's KARGO UAV program
- PI Americas’ long-travel XY piezo nanopositioners-scanners
- AAMI project call submission deadline extended to May 12
- Jergens launches cast iron tooling column additions
- Airbus to acquire assets relating to its aircraft production from Spirit AeroSystems
- FANUC America's Cobot and Go web tool
- Chicago Innovation Days 2025: Shaping the future of manufacturing
- High-density DC/DC converters for mission-critical applications