Productivity has been a manufacturing buzzword for decades. So it might be hard to imagine that it has taken on an even more heightened sense of urgency among some manufacturers, but it has at Kennebec Technologies.
Kip Tjelmeland (pronounced “Chum-land”), CNC programmer and process engineer for Kennebec, explains that his company’s aerospace and defense manufacturing contracts frequently call for percentage reductions in piece part pricing every year. Becoming more productive is essential, especially if you want to avoid having the project you won this year becoming a drag on profitability next year, and beyond.
For the past decade, the company has been responding to the challenge of increasing productivity: first by installing good CNC equipment; next by standardizing all programming on a solid CAM system; and then by transferring a substantial amount of manufacturing to advanced multi-axis systems.
Recently, Kennebec has put versions of its CAD/CAM system, Mastercam, at the fingertips of specialists involved not only in programming, but also quoting, manufacturing engineering, and process optimization. Each of these specialists can access the CAD/CAM files, and they work together – both formally and informally – to improve productivity, not only during product development but throughout the life of a program.
Across All Phases
Kennebec Technologies is a full-service, high-precision machine products manufacturer specializing in complex, high-value-added parts and assemblies. The company’s milling, turning, and grinding is particularly well suited for parts that fit roughly within an 18" cube envelope. With partially – attended workstations and twin-spindle, 13-axis, four turret machines, Kennebec can optimize cycle times for competitive pricing of high-precision parts, while maintaining a high level of service and quality.
Kennebec Technologies selected Mastercam as its CAD/CAM package in 2001 when it decided to replace its existing system, which was very complex because it also incorporated civil engineering capabilities. For the better part of the decade, Mastercam has been primarily used for programming the CNC equipment. However, over the past few years, users at every critical point in the company’s workflow have been cross-trained in Mastercam. It is this development that has played a pivotal roll in Kennebec’s efforts to strip inefficiencies from every phase of its manufacturing processes.
Quoting Process
A single person at Kennebec handles all the quoting, which are then reviewed and accepted by the engineering manager. This ensures that all of the administrative details involved in government and aerospace contracting are handled consistently.
Nearly all the work that comes into Kennebec’s quotes specialist is in the form of a CAD model or digital print. Most of these are readily imported into Mastercam at the quotation stage. If the file is a digitized drawing in a TIFF format, this can also be readily imported into the program, and if the file is proportional to the workpiece, it can be used as the starting point for creating the solid model used for CNC programming.
Once it has been successfully imported, the quotes specialist saves the CAD file on the server for everyone on the team to use. The CAD model allows the team to better visualize the part, as well as the CNC machine, setups, and operations that will be used to manufacture it. If anyone has any questions, they will confer with the manufacturing engineer and/or programmer who now have access to the same file. Files are stored in specific file folders with levels of security for file storage and control.
Manufacturing Engineering
For the past two years, manufacturing engineers at Kennebec have been relying on Mastercam as their primary working environment. This represents a significant change that required all the manufacturing engineers to pursue dealer training and self-instruction to become CAD-proficient, with the process starting in 2006.
When Kennebec wins a job, the manufacturing engineer accesses the quote file from the server. The ME then verifies that the CAD file does indeed refer to the part in the purchase order. Then the manufacturing process is built, which includes machine selection, tool sheets, setup, and a detailed fixture design – all with the help of Mastercam. When this work is completed, the enhanced model is saved as a customer file, along with the part number in the production area of the server.
“Using solid models to create fixtures really works well for us since we have to deal with a lot of challenging thin-walled castings,” Tjelmeland says. “While machining, we need to hold the castings securely, but we cannot dent or distort them. We also need to allow for wide ranging tool access to avoid additional setups (that is, access the part in multiple machining planes), so we orient the part within Mastercam generally with the 3-2-1 datum point system for locating it, and build the fixture design and clamps around that part model. Then we remove the part from view, explode the fixture and clamps, and do all of the dimension work. It is not only an efficient process, but allows for more part orientation access in the manufacturing process.”
CNC Programming
By the time the job/file is forwarded to programming, it contains all the information needed to generate the CNC toolpaths for making both the part and/or fixture. This includes machine, setup, and tooling information that is necessary to program the job. This also allows programming to be the second look at interpretation of this information, which saves time and reduces the possibility of human error.
After reviewing the information, programming can focus on the primary task of creating a CNC program that will operate as efficiently as possible.
This is accomplished by applying toolpaths that have worked well in the past on similar materials and geometries. There are literally dozens to choose from, and the programmer can readily modify any of the toolpaths to accommodate unique machining requirements of the geometry at hand. Once the programmer has completed the program, he can run Mastercam’s backplot feature, a computer simulation that allows the programmer to ascertain that the program will run safely on the chosen CNC machine, and to accurately estimate how long it will take to actually manufacture the part. Tjelmeland believes that time estimates based on the backplot feature are accurate to within 3% (generally erring on the high side). If the programmer is not satisfied with the machining time, he can then apply different toolpaths to areas where he would like to improve efficiency. This can be done in any order without sacrificing any of the other toolpaths that will remain in the program.
An example of the high speed machining toolpath that Tjelmeland uses frequently to improve efficiency is Morph Spiral. Nominally speaking, this is a pocketing toolpath but “that terminology can be misleading,” he says. “When you say pocketing, most people think about cutting an area out, but you can also use pocketing to create an external section. You just treat them as islands. Morph Spiral is very good because it never buries the tool more than what you tell it to. So if I want to run stainless steel at 250ipm or aluminum at 400ipm and I do not want to exceed a certain depth and blow the tool, I will use the Morph Spiral toolpath.”
Program Generation
Once the program has been written, the programmer uses one of six post-processors to generate a program for operating a particular CNC on the shop floor. The program is then stored in the production area of the server. Kennenbec’s goal is to have a CNC program that can be downloaded from the server to the machine tool and run without modification on the shop floor. Sometimes scheduling problems require that a different machine be used for a subsequent production run – perhaps using a horizontal instead of a vertical machine. The programmer simply regenerates the NC code using one of the other postprocessors and no additional CAM programming is required.
Tjelmeland used to be the primary programmer at Kennebec. Now he spends a substantial amount of his time doing manufacturing engineering work – primarily process optimization.
“There is no such thing as an acceptable loser,” Tjelmeland states. “If it is running five minutes longer than what you quoted, that is not acceptable. So if the process is not frozen, we go back to the drawing board and try to get it to meet our quoted time while maintaining quality.”
Most of this work involves revising the toolpaths by selecting something else that has worked well before in similar instances, or delving into the latest Mastercam product release to try something that the company has not used before.
One of the best ways to take significant amounts of time out of a job is to shorten roughing time. “For aluminum parts, we have done this with a trochoidal pocketing toolpath. It actually takes small arcs instead of going in a straight linear move, and we can really improve stock removal rate without breaking end mills or loading them up with aluminum,” Tjelmeland explains.
“There is always a tradeoff between how much material you want to remove and how quickly you want to do it. This software helps us push our tools to their limit, but not further. It just takes a couple minutes to put a different toolpath in a program and repost it. Then we run it to see if the results are acceptable. If we do not like what we see, we back off a little.”
At this point, the process has come full circle. Optimizations created in the CAD/CAM system fulfill machine cycle expectations that were originally established in the quote stage – all within the same CAD/CAM environment.
CNC Software Inc.
Tolland, CT
mastercam.com
Kennebec Technologies
Augusta, ME
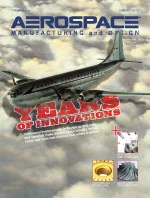
Explore the June July 2010 Issue
Check out more from this issue and find your next story to read.
Latest from Aerospace Manufacturing and Design
- AAMI project call submission deadline extended to May 12
- Jergens launches cast iron tooling column additions
- Airbus to acquire assets relating to its aircraft production from Spirit AeroSystems
- FANUC America's Cobot and Go web tool
- Chicago Innovation Days 2025: Shaping the future of manufacturing
- High-density DC/DC converters for mission-critical applications
- #59 - Manufacturing Matters: Additive manufacturing trends, innovations
- ACE at 150: A legacy of innovation and industry leadership