The push for larger, lighter, and more fuel efficient airplanes creates real opportunities for alert aviation supply-chain manufacturers to be able to do a better job machining titanium – including the new 5553 grades. In the new 210-330 passenger Dreamliner, for instance, the ratio of titanium to steel and aluminum is three times higher than in earlier generation aircraft. Where once you saw high tensile steel in the landing gear, now you find titanium; where once you saw aluminum airframes, you now find composites and titanium; where once you saw the bogy beam and slider made from high tensile steel 300M, you now find Ti 5553 or Ti 10-2-3. But, that is not all. Wherever you find composites or plastics, you are more likely to find the adjoining members in titanium, because of its closer match in thermal expansion characteristics and better bond strength.
These trends are already causing a logjam in airplane parts manufacturing. Why? Because under even the best conditions, the more familiar titanium alloys take ten times longer to machine than aluminum, and perhaps four times longer than high tensile steel. Usually it requires more horsepower per unit removed, and a machine with higher torque. Next is the new titanium 5553 (5Al, 5V. 5Mo, 3Cr) grades, which are 20% to 35% stronger than mainstay Ti 6Al, 4V, but even more difficult to machine by a factor or 4:1. As use of Ti 5553 grows, so will the machining logjam in aircraft production.
That logjam can be your best business opportunity in this tight economy.
Titanium is well known as the go-to metal for its high strength to weight ratio. That means weight savings, which directly translates into higher fuel efficiency and lower greenhouse-gas emissions. Small wonder that the use of titanium is growing faster than any other metal, with no real end in sight. Market demand for titanium machining capacity is definitely on the rise, and is clearly here to stay, so if you master titanium machining and market it well, you will pretty much secure your future.
The bad news is that, titanium is more difficult to machine than aluminum or stainless. The reasons for its lower machining rate are many. Its high strength means more power is required to produce the chip. With a relatively low modulus of elasticity, titanium tends to deflect away from the cutting edge more than aluminum or steel, therefore needing a sharper cutting edge to hold tolerance. The metal also tends to crater upon tool entry and exit, unless the cutting edge remains sharp. Its low coefficient of thermal conductivity means more heat buildup in the cutting zone, which leads to smearing, welding, and built-up edge, all of which undermine the tool and workpiece.
The good news is that Iscar has already developed a complete line of milling, turning, and holemaking tools specifically optimized for titanium work. It is no exaggeration to say that these tools can improve material removal rates in all popular titanium alloys by more than 40% on average.
Anatomy of a Tool
The common attributes of these advanced tools include very sharp edges with honed flanks to delay built-up edge; helical cutting edges to ease the insert into the workpiece; as well as heat-resistant coatings and internal coolant directed right at the cutting zone. A choice of substrates enables you to optimize either wear resistance on tight machines and optimal cutting conditions, or toughness to withstand impact loads and chatter in less-rigid cutting systems, long overhangs, and interrupted cuts. In both cases, the emphasis is on predictably long life, so the tool runs securely over machining cycles measured in days rather than minutes. One aerospace fabricator reports double the edge life on both titanium and other super alloys by switching to the IC380 grade, with no other changes to the process.
Two of the typical characteristics of cutting edge wear that occur while milling titanium are chipping and cracks on the cutting edge, reducing the insert life. In order to prevent the cutting edge from chipping, Iscar’s R&D division developed a very tough reinforced carbide substrate.
When it comes to rough and tough milling applications in titanium, the tougher carbide substrate exhibits longer tool life. In some applications, when compared to any other available carbide grade, the tool life is even three times longer. This is very important for the production of parts demanded by the aerospace industry.
Contributing to that extra reliability is the Sumo Tec coating treatment, introduced in late 2007, which improves tool performance by smoothing out the coating and reducing friction in the cutting zone. Most Iscar milling, turning, and holemaking inserts for titanium work now feature that treatment. Early users in the airframe fabrication business report 25% to 40% better tool performance in titanium, due to that coating treatment alone.
Other recent tooling developments for titanium machining:
- For 90º milling, the new Helido cutter features double-sided inserts with four cutting edges rather than two.
- Helitang tangential milling cutters, which target heavy rough milling, are now available with sharp edged inserts with polished flanks ideal for titanium. They have delivered extremely high removal rates in facing, shouldering, slotting, and side plunging. The tangential orientation presents the insert’s strongest cross section to the main force vector and the helical curve on the cutting edge providing the soft clean entry, which is vital for titanium work.
- For heavy rough milling of deep pockets (in order to decrease part weight), where long tool extension is essential (very common in the aerospace industry), a recent spin-off is the Helido-Feedmill H600 double-sided inserts. These feature a special geometry to facilitate milling at very high feeds for high volume metal removal, ensuring fully effective cuts. The resultant cutting forces are directed axially towards the spindle, providing greater stability under high cutting loads and enables milling at high feeds.
- When solid carbide mills are required for accuracy and finish, the Feedmill cutter line offers styles specifically for titanium work. The basic shank design and asymmetric flute pattern permit heavier cuts in tough titanium without jeopardizing the cutter itself. More of the cutting forces are axial to reduce deflection that can snap a solid carbide tool in a heartbeat.
- Similarly, additions to the Finishred family of roughing/finishing solid carbide endmill qualify it well for titanium work. Two continuous smooth flutes enable it to handle roughing and finishing in the same pass – ensuring fast metal removal plus fine finish. The dual purpose cutter also saves one spot in the tool magazine and eliminates one more cycle stop for tool changes.
Composite materials have gained popularity in high-performance products that have a need to be lightweight, yet strong in harsh conditions, and many new types of aircrafts have composite material structures which include the wing and fuselage parts. Composite materials provide distinct advantages in the manufacture of advanced products, but they are easily damaged unless machining is properly performed. By their nature, composite materials are non-homogeneous, anisotropic, and reinforced with abrasive components – making composite materials much more difficult to machine than metal alloys – and categorized as difficult-to-machine-materials. The composite material workpiece can easily suffer intolerable damage during cutting, and the tool wear rate can turn out to be unacceptably high.
Cutting composites may incur more damage to the workpiece (like delamination of bottom layers when drilling) if not done carefully or correctly.
Highly advanced milling and boring tools provide complete solutions for machining composite materials, Iscar’s PCD (polycrystalline diamond) tools have become the popular choice, as they wear less.
Latest Developments
When machining jet engine parts, different and better solutions are available – based on advanced products – enabling much shorter machining times and with a reduced number of tools.
A new line of tools, designed to overcome the above-mentioned difficulties, are tools designed for use with high pressure coolant, 70 bars to 120 bars. These tools can improve productivity by enabling increased cutting speeds of approximately two to three times, with no reduction of insert life, while significantly improving the chipbreaking results. The line is designated as Jet HP line (HP = high pressure) offering a selection of ISO tools, groove-turn, and parting off.
Today, the main machine builders are able to fulfill the customer’s demands by equipping their machines with standard built-in high pressure pumps in a range of 60 bars to 100 bars. Modern machines, equipped with high pressure pumps, will give the customers a massive advantage by using the right tooling with these machines. The benefits include increased cutting speeds, improved chipbreaking, maintenance of low machining temperatures, and long extended insert life.
Groove-Turn Tools
Groove-turn tools, such as Cut-Grip, are very well-known by customers in the aviation industry. Utilizing their design and structure for multi-directional machining in grooving, turning, and profiling operations for the most complicated parts and shapes, requires only a minimum number of tools. The design with the strong prismatic clamping mechanism ensures rigid clamping and allows use of the groove-turn tools also for machining deep cavities, where other conventional tools are not even able to penetrate due to their limitative dimensions and structure.
This combination of advantages, together with the high pressure option, dramatically increases the productivity of machined parts. For example, on titanium you can reach high speeds of approximately 150mpm as compared to 60mpm with regular low pressure cooling.
Holemaking Tools
Being involved in new projects in machining keeps companies aligned with worldwide trends, providing the most effective, productive, and suitable solutions.
Updating the Dr-Twist line with the latest geometry for machining aluminum parts, are the SOGX inserts with four cutting edges, which can be mounted on the same pockets of standard bodies. Peripherally ground, with extremely sharp cutting edges and a chipbreaker dedicated for aluminum machining, AL inserts allow dramatic increases in the cutting speeds and feeds while holding high accuracy requirements of the holes. Polished surface finish of the AL chipbreaker allows elimination of the built-up edge phenomenon and increases the tool life of each cutting edge, as well as maintaining accurate drill performance.
This line has proved its performance in titanium machining as well. Twisted bodies with high strength and high flute helix angle for easy chip evacuation, in combination specific grades, allows increases in the cutting speed while keeping the same tool life and hole accuracy.
A new drill body, for the Sumocham line, offers improved rigidity and high helix angle flutes, with extremely high surface quality for easy chip evacuation. This, combined with ICM geometry for titanium and Inconel alloys, enables much higher cutting parameters while still retaining high hole accuracy. Also, the heads clamping mechanism allows for longer tool life and a high number of head indexes on one drill body, meaning an economical solution.
For aluminum parts, the ICN geometry heads have a high positive rake angle and polished chip gullet area for excellent chip control and minimizing built-up edge phenomenon.
Where a reaming operation is needed, the Bayo-T Ream line has variable geometries that will match any possible geometrical requirement of the machined hole.
As a very user-friendly and economical solution suitable, for any material, it is specially designed geometry for titanium machining comes in an uncoated grade with extremely sharp cutting edges and special lead angle – providing the ability to work with much higher cutting speeds and feeds.
Closing the Capacity Gap
These are just a few examples of Iscar’s recent tooling developments that aim to close the capacity gap in titanium machining. Most have been introduced or upgraded within the last two years. Continued development, dedicated tools, and methods for the aerospace industry help provide the most advantageous and productive machining solutions for customers.
Iscar Metals Inc.
Arlington, TX
iscar.com
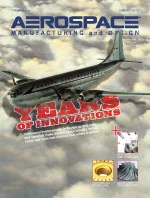
Explore the June July 2010 Issue
Check out more from this issue and find your next story to read.
Latest from Aerospace Manufacturing and Design
- Trelleborg acquires Aero-Plastics
- Industrial automation products, enclosed encoders
- #61 - Manufacturing Matters: CMMC roll out: When do I need to comply?
- AIX shows aircraft interiors are a strategic priority for global airlines
- Machine Tool Builders Roundtable: Turn equipment into expertise
- No time to waste: How to machine MedTech parts more efficiently
- The 5 Best and Fastest Spindle Repair Services
- Mill smarter, not harder: How collaboration optimizes production