Working closely with two large suppliers has given Airbus advantages on several levels. In building new production capacities, the aircraft industry is relying heavier on key suppliers that can realize large turnkey work packages. The new Airbus plant in Tianjin, China, is playing a pioneering role in that. Working with Airbus, partners Dürr and EDAG built an assembly line there for the Airbus 320 in only 13 months. Dürr is also supplying the platform systems for the painting facilities in Tianjin.
Built by a Chinese Airbus partner, the hangar – in which the final assembly line (FAL) was installed – is 250m x 70m x 30m. Four large stations in the line were installed by Dürr and EDAG and are connected with sections that Airbus itself provided.
At the first station built by Dürr, the two pre-assembled fuselage halves are positioned together atop four fuselage jack pads. This is performed with precision to prepare the halves for the joining process. The two fuselage pieces are then deburred and riveted.
At the second station, wing assembly, Dürr also contributed its specific expertise in systems for exact positioning to within tenths of a millimeter. The key element of this station is the wing cars, which, like the fuselage jack pads, are supplied by the Dürr plant in Wyhlen, Germany. In addition to the wings, the undercarriage is also installed at the second station.
The two subsequent stations were supplied by EDAG, with whom Dürr established the Prime Contractor Consortium (PCC) in 2007 specifically for the Tianjin project. At the third station, structural and system components are installed, while outfitting of the interior begins. That is followed by an extensive inspection of the electrical and hydraulic systems, and the cabin’s leak tightness is checked. The dock station, also supplied by EDAG, is the end of the assembly process in the hangar where the carpeting is laid, seats and baggage compartments are mounted, and the interior outfitting is nearly completed.
Aircraft are then painted, with another plant for painting the tailfins. Dürr has supplied the platform systems for that. In the final phase station, the aircrafts are equipped with the engines. With final assembly details carried out, and customer requirements are reviewed.
Customer Advantages
Working closely in a project partnership with two large suppliers has given Airbus advantages on several levels. Dürr and EDAG installed the four ordered stations in time and on budget – and with lower coordination efforts than in the case of other large projects. During peak times, up to 150 people were working on the project. Airbus is completely satisfied not only with the execution and project management, but also with the quality of the systems in ongoing operation. “The customer gave us very positive feedback when the first pieces were placed in the plant and everything went perfectly from the start,” says Werner Lotz, head of EDAG’s aircraft assembly division.
According to Dürr Aircraft head Dr. Uwe Siewert: “The magnitude of what Dürr and EDAG supplied as a single source in Tianjin is something new in the field of aircraft construction. Dürr and EDAG have exactly the capabilities needed for such projects: system and product expertise, the ability to deal with large volumes, and project management with global presence.” Against this background, the two companies have further intensified their partnership and founded the joint venture Dürr EDAG Aircraft Systems GmbH.
Dürr Systems GmbH
EDAG GmbH & Co. KGaA
Stuttgart, Germany
durr.com
Get curated news on YOUR industry.
Enter your email to receive our newsletters.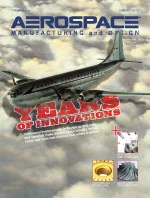
Explore the June July 2010 Issue
Check out more from this issue and find your next story to read.
Latest from Aerospace Manufacturing and Design
- America Makes announces QTIME project call
- Innovation meets precision for 40% faster machining
- Upcoming webinar: Pro tips from a supply chain strategist
- Heart Aerospace relocates to Los Angeles
- Fixtureworks introduces Stablelock Clamps
- Piasecki acquires Kaman's KARGO UAV program
- PI Americas’ long-travel XY piezo nanopositioners-scanners
- AAMI project call submission deadline extended to May 12