The actual ViaSat antennae system is assembled in the United States and used on aircraft all over the world.The demand for broadband via satellite is growing in demand every day. Every time a new broadband satellite launches there is a spike in subscribers immediately afterwards, which almost as quickly caps out in key geographic areas. The need for high-capacity, Ka-band satellite systems that allow for the increased demand for media-rich Internet access over the next decade has to be met. ViaSat is one company that has put its design engineers expertise to the test in finding a solution to this challenge.
Challenges
Providing satellite service to military transport, private, and commercial aircraft has not been an easy task, but through the use of the latest technologies, satellite service is advancing forward at an alarming rate. Even though the electronics for the three-axis positioning control of a satellite dish is available, there are mechanical elements that must also meet the demands and the challenges that on-aircraft components must meet.
Mitch Blalock, one of the design team members and manager of positioning products for ViaSat explains: “Our system is for airborne applications where a 12" to 18" dish sits on the jet and tracks satellites for communications purposes.”
Needs of the System
The communications tracking system includes the modem, the antennae (satellite dish), and the positioning control system. Blalock, an mechanical engineer, had to come up with a way for the satellite dish to physically move in a way that accurately followed the electronics control. If the mechanical system fails for any reason, the electronics are essentially useless.
“One of the major challenges was to allow the antennae to move in an X, Y, and Z motion smoothly and efficiently. Plus, the motion had to be performed within the volume of the radome, which has about a quarter inch of clearance for the antennae’s motion,” Blalock says.
The larger the antennae, the greater the bandwidth, so it was essential that the ViaSat team be able to use the largest dish they could. Because most systems hold to the dish on the end of a stationary arm, there is little space left inside the radome. This means that a smaller antennae has to be employed, as it is mounted to the end of the yoke.
ViaSat holds the patent on Blalock’s design, which mounts the satellite dish directly to the mechanical motion system through the use of cam followers and gears. In this way, the company can use the larger 12" or 18" antennae, and still have enough clearance to spin rapidly.
The three-axis system uses cam followers and gears manufactured by Intech. “We made our own axis bearings using the cams,” Blalock says.
How the Design Began
ViaSat started with a blank sheet of paper. Blalock designed in the cam followers in the initial model because he needed components that could work within low temperatures, required no lubrication, and could handle being exposed to the environment. “I experimented with metal cam followers first, but they did not meet the required characteristics for the application,” Blalock says. In all, one system uses 20 cam followers and four gears manufactured by Intech.
“Intech was very supportive on the front end of the design. They helped with the design of the components, which included a semi-custom design based on their iCamFollowers. Intech knows the material specifications and their own manufacturing capabilities, and worked closely with us to create the right part for the application,” Blalock explains. “The components had to be easy to install, as well. Even though the system is assembled by experts, a reduced build time helps to keep overall costs reasonable. I was surprised how much load, for their small size, the Intech cam followers can carry.”
Bringing it All Together
The precision machined Intech Power-Core material installed over high quality ball bearings that makes up the cam followers, operates great at the low temperatures found at high elevations. The components can operate from -55ºC to 70ºC. The components also handle thermal shock well. For some of the military planes, they could be parked on the tarmac in the desert and then fly to 30,000ft or more soon afterwards. The cam followers and gears have to be able to handle this type of change without warping or swelling.
The dish antennae needs to move at a maximum of about 30°/second, but is continuously tweaking to maintain the best signal. This constant movement puts a lot of hours on the mechanical system, which makes long life an important characteristic. The overall accuracy of the system while flying, is less than a tenth of a degree, and must remain within 2° for the overall system.
The systems are designed and assembled in Atlanta, GA, and go through stringent testing and evaluation in order to make them 100% operational before they are installed on the aircraft.
Intech Corporation
Closter, NJ
intechpower.com
ViaSat
Carlsbad, CA
viasat.com
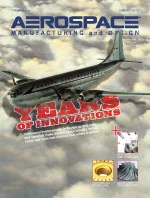
Explore the June July 2010 Issue
Check out more from this issue and find your next story to read.
Latest from Aerospace Manufacturing and Design
- DEMGY Group acquires Tool-Gauge
- OES’ dual-axis yaw pitch stages
- Mastering high-temp alloys with Kennametal Inc.
- Boeing to sell portions of digital aviation solutions
- SMW-Autoblok’s KNCS-matic 3-jaw power chuck
- 3 Questions with an Expert with Allied Machine & Engineering
- Electra raises $115M to pioneer Ultra Short aircraft
- Walter’s WT26 partial- and full-profile thread turning inserts