Evolving from a simple compressor, combustor, and usually single-stage turbine, today’s aircraft engines continue to combine advances in many engineering disciplines including mechanical design, aerodynamic design, metallurgy, protective coatings, materials, and manufacturing processes.
This includes holemaking and hole finishing. Keeping 21st century aircraft engine turbines together and cool requires holes – thousands of holes that must be sized precisely, aimed exactly, and made in hard-to-work alloys.
Fortunately, hole-finishing processes are improving as well. Hole-finishing processes like abrasive-flow machining (AFM) have evolved from pure deburring functions to polishing and radiusing to very close tolerances. Add new developments in machine controls, abrasive media, and flow targeting, and the results continue to get much more precise.
Machined holes, including intersecting holes in aerospace applications, require surface improvement and typically a lot of polishing to achieve required tolerances. However, when considering holes in turbine engine components that rotate at very high speeds, any smeared metal or micro-cracks at the surfaces – created using both conventional and non-conventional machining processes – increase the risk for diminished performance or failure.
Aeronautical engineers factor AFM surface finishes into many component designs, especially where laminar flow, boundary layer turbulence, compressive residual stresses, and edge conditioning are important factors. Even in inaccessible areas, surface-finish improvements from an original 120μ" to 16μ" or better are possible.

Further research and development in AFM at Extrude Hone has resulted in MicroFlow AFM, where lower-viscosity media and smaller abrasive particle size allows finishing and edge radiusing of holes down to 50μ". Fuel-spray nozzles in fuel injectors, for example, can have defined edge radiuses that improve fuel spray distribution for better engine performance.
Abrasive-flow machining is also valuable in overhaul and repair applications. Aircraft engine rebuilders use AFM to remove carbon deposits and restore flow characteristics to original specifications.
Kennametal
Latrobe, PA
kennametal.com
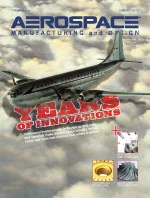
Explore the June July 2010 Issue
Check out more from this issue and find your next story to read.
Latest from Aerospace Manufacturing and Design
- Address the challenges of machining high-temperature aerospace components
- Elevate your manufacturing operations with April’s Manufacturing Lunch + Learn
- America Makes announces IMPACT 3.0 Project Call worth $4.5M
- Updated parting and grooving geometries from Sandvik Coromant
- AIX showcases the future of air travel
- Sunnen Products' PGE-6000 gage
- #41 Lunch + Learn Podcast - SMW Autoblok
- Revolutionizing aircraft design without sacrificing sustainability