As the wise business adage goes, “You cannot manage what you do not measure.” The cribs used to house your equipment quickly turn into bone yards because of outdated utilization management practices. In fact, if all you manage is what is in the crib, it probably accounts for less than 25% of your equipment costs. One must manage the entire test environment holistically.
The largest companies have campus locations that use $100 million or more of test equipment. All too often, engineering executives have very little knowledge about how that equipment is being used, and whether they have the capacity necessary to meet future demand. Opinions rule the day, and there is no agreed-upon method for measuring utilization or capacity – especially in engineering environments. In reality, typical rates at these companies run as low as 6% and rarely higher than 20%. Of course, companies either find out too late that they need more capacity, suffering delivery delays, or they keep spending money on new purchases to ensure they never run short of equipment.
A lack of comprehensive data is the first big hurdle. As a result, managers tend to set cost-saving goals too low. Without a clear picture of the problem, they do not see the full potential for cost reduction.
As an example, say you do have accurate, thorough, test equipment data. Most equipment management initiatives, are still destined to fall short of their full potential. Why? Because they put almost all of their focus on what they know how to do – piecemeal tactics disconnected from a larger strategy that attacks the real root of the problem.
Technical organizations tend to focus on what they know – technical content. That is not bad, but it is not enough. Instead of managing an integrated whole, they manage portable analyzers, wind tunnels, and product-specific fixtures or cables in separate practices as if that equipment was not all used together. While they bar code equipment, enter it into a database, and calibrate it – some of the necessary components, to be sure – they do not get at the root cause of the poor utilization and higher cost.
Meanwhile, the root of the test equipment management challenge is not the test equipment itself; it is the deeply embedded habits and practices of the people who use and manage the equipment – such as hoarding. If test engineers do not believe they will get the equipment they need when they need it, they tend to stockpile equipment they might need. Change those habits and you will drive lasting, positive change.
To succeed in your initiative, you need a focused commitment to the holistic management of the entire test environment – not just the equipment, but the people involved, the practices they follow, and the tools they use to help them.
Key Components
Essential actions of successful test equipment management include designing the right set of practices, refining peoples’ roles and incentives, using tools that increase the efficiency and ease of performing the practices, and continuously assessing their results.
Pay particular attention to the following areas, all focused on the people in your organization.
Creating practices for identifying, measuring, and then acting to change the behavioral dynamics that produce barriers to success, such as hoarding equipment or moving it without authorization. You will need continuous practices to track where process breakdowns occur and provide closed-loop feedback to resolve those issues – therefore, injecting trust into the new processes;
Developing practices for directing and managing change and producing strategic alignment – including continually assessing the satisfaction of all constituencies; developing narratives that mobilize action around the plan and institutionalizing the change through ongoing measurements and governance; and Providing managers, practitioners, engineers, technicians, finance, property, purchasing, etc. with processes or metrics that take care of the issues they care about. These efforts will help ensure that these constituencies continue to embrace and abide by the new system over the long term.
In short, you need to ensure that your people have some sense of vision for the changes that need to be made, and can see the part they must play in it while being motivated to move forward. The new practices must ultimately make getting tests done easier for users of test equipment.
While the issue of cultural change can seem soft, the solutions are hard, enabled by effective practices and software tools. Engineering-focused organizations often lack the full array of skills necessary to succeed. Ask yourself whether these skills exist in your company, or whether you may need to look outside for support.
Getting Started
The first step should make a lot of sense to any data-driven engineering organization. It is critical that detailed process maps be complete prior to tool integration. Until you understand the full scope of the challenges in your test environment, you cannot craft an appropriate solution. The startup must begin with the development of detailed process maps, metrics, and tool specifications. It is advantageous to build these maps on a foundation of proven success.
If you introduce a new process that promises to increase utilization, your engineers will be rightfully skeptical because they have seen past cost reduction initiatives create havoc with their schedules. Rigorous upfront process work and analysis supplies you with the knowledge to help you confidently communicate the capabilities of the new set of processes, which is important because users will not trust you if you cannot speak confidently and show them how it is going to work.
Even with the best processes in the world, you will need continuous, effective communications to maintain that trust. Starting with your foundation of detailed, refined process maps – including a clear understanding of who is accountable for what task – you can begin to share this information. Not all constituents care about the same thing, and they all need to be communicated with in a way that specifically addresses their concerns.
Conversely, effective communications will mobilize action and accelerate results. However, doing so requires skills in developing complete and compelling narratives. The complexities of what needs to be communicated, how it needs to be communicated, and to whom it needs to be communicated are significant.
Ultimately, nothing builds the required trust better than results. The example at the beginning shows that building and maintaining trust in its program is through consistently getting the engineers the equipment they need, when they need it, so that they are free to drive the innovation that is critical to the company’s success. The approach detailed here has recurrently reduced capital budgets and equipment on the books by 50%, while decreasing cycle times by up to 25%. Smart companies use these savings to their competitive advantage.
At a time of intense competition in the aerospace industry, is the precise time that a company should seize the opportunity to achieve similar productivity improvement?
The Sente Group.
Suwanee, GA
sentegroup.com
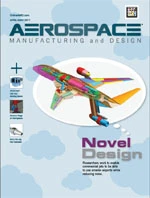
Explore the May June 2011 Issue
Check out more from this issue and find your next story to read.
Latest from Aerospace Manufacturing and Design
- Season's greetings
- 2024 Favorites: #7 Article – Deep drawing aerospace components
- 2024 Favorites: #7 News – GKN Aerospace completes sale of St. Louis facility to Boeing
- 2024 Favorites: #8 Article – Beyond uptime
- 2024 Favorites: #8 News – NASA, Lockheed Martin reveal X-59
- 2024 Favorites: #9 Article – 5 tips for upskilling your aerospace machinists
- 2024 Favorites: #9 News – Siemens acquires Altair Engineering
- 2024 Favorites: #10 Article – How 3D-printed aviation parts can accelerate return to air