EDM, 5-Axis Milling, and Vertical Drilling Technologies on Display
The GF AgieCharmilles CUT 200 Wire EDM provides faster spark-to-spark wire threading, increases energy efficiency, and boosts productivity when cutting parts of variable heights. The machine also offers higher flexibility through its ability to reliably hold tolerances measured in microns over a wide range of part sizes. The CUT 200 integrates GF AgieCharmilles’ Power Expert smart module, which continuously calculates part thickness, checking flushing pressure and adjusting machine power accordingly. This prevents wire breakage when changing the part thickness being machined.
The machine also offers an optional Renishaw touch probe that allows users to inspect finished parts while still on the worktable in the machine, eliminating the need for part inspection with a CMM. The CUT 200 accommodates wire diameters ranging from 0.07mm to 0.33mm and can handle part tapers of up to 45°, regardless of part thickness. The machine’s digital CC generator enables surface finishes as fine as Ra 0.1μm and an optional power module can boost cutting speed to 37.2 in2/hr.
Additionally, the Econowatt 2 smart module provides energy savings by allowing operators to define conditions in which the machine will automatically shut down or awaken to complete thermal stabilization prior to production.
Also on display will be the FORM 20, a cost-effective solution that combines ease of use with exception performance; the HSM 400U LP, a 5-axis, high-speed milling center, and the DRILL 20 high-speed vertical drill.
EASTEC BOOTH #1224
GF AgieCharmilles
Lincolnshire, IL
gfac.com/us
Direct-Drive Rotary Systems
The Hardinge direct-drive rotary systems provide flexible, high-speed, super-precision rotary parts positioning. These rotary tables have zero backlash, permitting rapid bi-directional movement without the loss of time used to compensate for position over-travel, which means more time in the cut. A frameless torque motor wraps around the spindle, eliminating the need for a separate motor extension, resulting in a smaller footprint. An encoder capable of ±0.077 arc second resolution is mounted directly to the spindle enabling ±3.000 arc second system accuracy for extremely accurate positioning with 4.000 arc second repeatability. A rugged cross-roller bearing provides super rigidity.
Three sizes of the rotary systems are available. The DD100 high-speed positioner has a 5C, A2-4 spindle nose and is ideal for drill and tap and laser processing with speeds of up to 4,200°/second or 700 rpm continuous rotation. The DD200 and DD300 rotary tables include a spindle clamp to handle aggressive off-center drilling and other high-force machining operations. All three models have a Hardinge collet-ready spindle for quick changeover from collets, step chucks, expanding collets, jaw chucks, and face and fixture plates. The DD200 (254mm) and DD300 (305mm) rotary tables have a 16C, A2-5 spindle nose and come with a precision-ground slotted faceplate in the aforementioned size.
Fourth-axis integration supported by Fanuc and Heidenhain allow operators to take advantage of maximum machine capability including look-ahead programming for high speed machining.
EASTEC BOOTH #5045
Hardinge Inc.
Elmira, NY
hardinge.com
CNC Machine Simulation, Optimization Software
VERICUT is CNC machine simulation, verification, and optimization software that enables users to eliminate the process of manually proving-out NC programs. It reduces scrap loss and rework. The program also optimizes NC programs in order to save time and produce higher quality surface finish. VERICUT simulates all types of CNC machine tools, including those from manufacturers such as Mori Seiki, Mazak, Makino, Matsuura, Hermle, DMG, DIXI, and Chiron. VERICUT runs standalone, but can also integrate with leading CAM systems such as Catia V5, NX, Creo (Pro/E), Mastercam, Edgecam, hyperMILL, and GibbsCAM.
VERICUT 7.1 features significant enhancements to reduce the time required for manufacturing engineers to easily develop, analyze, inspect, and document the CNC programming and machining process. Along with proactively adding new features, CGTech developers and engineers focused on addressing hundreds of customer-driven enhancements. Version 7.1 contains more than 400 customer requests and further improvements to VERICUT’s user interaction, simulation capabilities and analysis, cutting tool creation, and CAD/CAM integration.
One of the new features added, at the request of customers, is a 3D Reviewer. With the VERICUT Reviewer, 3D simulations can be shared with anyone in the company – without using a license. The Reviewer can play forward and backward while removing and replacing material. Error messages and NC program text is highlighted when a collision on the stock or fixture is selected. A toolpath line display is optional. The user can rotate, pan, and zoom just like normal VERICUT, and the cut stock can be measured using all the standard X-caliper tools.
EASTEC BOOTH #5344
CGTech
Irvine, CA
cgtech.com
Multi-Feed Technology OffersChoice of Tool Feed Methods
The Sunnen multi-feed honing technology gives users a choice of tool-feed modes to achieve the shortest cycle times, lowest part cost, and longest abrasive life. Multi-feed combines Sunnen’s controlled-force tool-feed with its controlled-rate feed system. The two different tool-feed modes allow the user to select the better option to suit the workpiece geometry, material, and tool type/size. Multi-feed technology is available as an option on new machines in Sunnen’s SV-1000 and SV-500 Series, as well as a retrofit for existing machines in these series.
Controlled-force honing, a new feature in multi-feed, works like cruise control to ensure the optimum cutting load on the honing abrasive throughout a cycle, irrespective of the incoming part’s hardness, geometry, or size variation. Depending on the application, controlled-force honing cuts cycle times by as much as 50%, lengthens abrasive life for lower consumable cost, and allows finer control of surface finish parameters than before. Controlled-force technology eliminates glazing of the abrasive, due to too little force, and maintains a steady, free-cutting, self-dressing condition for maximum metal removal in the shortest possible cycle time.
EASTEC BOOTH #2111
Sunnen Products Co.
St. Louis, MO
sunnen.com
Three-Dimensional Waterjet Cutting Technology
The Flow Mach 4 cutting system combines Flow’s HyperJet pump, rated at 94,000psi, with Dynamic Waterjet XD, a high-precision flat stock and 3D waterjet cutting technology. This combination improves part cycle time and accuracy two to four times over standard non-Dynamic systems.
Flow’s HyperJet pump rated at 94,000psi, delivers a stream of water at nearly four times the speed of sound. Pressure equals productivity: waterjets equipped with HyperPressure systems, running continuously at 87,000psi, cut up to 50% faster while using less abrasive than conventional waterjets. Cutting parts with a lower cost per part enables completion of more jobs in less time.
EASTEC Booth #1412
Flow Int'l Corp.
Kent, WA
flowwaterjet.com
High-Tech Cutting Tools
On display will be the line of high technology cutting tools, including the three-flute coolant-through Mega Muscle carbide drill, the HY-PRO CARB 3D and 5D drills, and the VGx and UVX endmill series. The HY-PRO CARB VGx variable geometry endmill is a milling tool with capabilities of chatter-free and stable consistent milling in mild to severe milling operations.
OSG’s three-flute coolant-through Mega Muscle drill is designed specifically for drilling at feedrates one-and-a-half to two times faster than a two-flute drill. It may also be used at lower rpms, which decreases the amount of wear while prolonging tool life, while also leading to higher hole accuracy with less work hardening, giving secondary operations such as tapping even more tool life.
EASTEC BOOTH #5463
OSG Tap & Die Inc.
Glendale Hts., IL
osgtool.com
Various highlights during EASTEC will be:
5-Axis Hole-Making – A new routine for 5-axis hole-making operations, aided by enhancements to GibbsCAM’s automatic feature recognition, hole manager and hole wizard, makes programming 5-axis drill cycles much easier and much more efficient. Programming drill cycles at off-axis orientations will be very easy and will take a fraction of the time taken by other methods.
5-Axis Toolpath Conversion – A new Operation Modifier allows converting 2.5- and 3-axis toolpaths for machining in 5-axis, which enables use of shorter tools to achieve smoother toolpaths at certain surface intersections and other geometric conditions.
5-Axis Machining Styles – Additional swarf cutting capabilities have been added, as well as a new 5-axis trimming (wireframe) strategy.
5-Axis Milling on Turning Machines – Support for B-axis (tilting live tooling) enables programming of 5-axis milling with Y-axis offsets on lathes and multi-task machines equipped with a live-tooling B-axis.
EASTEC BOOTH #5433
Gibbs and Associates
Moorpark, CA
gibbscam.com
Next Generation Digital Indicators
The enhanced µMaxum II line of Mahr Federal indicators includes a wide range of features, including: dynamic max, min, tir; two point difference measurement; multiplier factor for ratio measurements; indicator serial number identification; resolution to 10µ"; selectable continuous output; and longer battery life.
Versatility of the µMaxum II indicators is enhanced in a number of ways. Resolution is selectable in increments from 0.001"/0.020mm down to 0.00001"/0.0002mm to accommodate differing application requirements. Two point difference measurements allow comparison of different readings or calculation of measured values. The addition of Multiple Factors for ratio measurements allows chordal-type measurements, which are useful for making ID/OD measurements using a V plate or for gage fixtures using lever-type non-direct contacts.
The µMaxum II line of Digital indicators is available in two models, the µMaxum II, and the µMaxum II XL, which provides longer measuring ranges. Weighing as little as 6oz, all µMaxum units are lightweight and ruggedly built to withstand hard use. The gasketed case, crystal, and stem assemblies resist fluid contamination.
Also on display will be the MarCheck measuring and evaluation unit for Mahr's high precision Linear 100 universal length measuring instrument, a new generation of its line of MarCal digital calipers, and the Digimar 816 CL Height Gage.
EASTEC BOOTH #3019
Mahr Federal Inc.
Providence, RI
mahr.com
Creep Grinding Applications
Designed for the aerospace industry, the Model 800 machine configuration is optimized for creepfeed grinding processes that require three linear axes. Specifically, it is a traveling column design with a Y-axis ram traveling on the Z-axis, and a stationary workpiece. This configuration allows for a very small machine footprint while allowing all three structural guideway rail mating components to have a large closed-box cross-section, which maximizes grinding stiffness and geometric accuracy. This configuration allows for easy implementation of common creepfeed grinding options such as CDCF grinding and indexing table part loading.
Standard 800 series features include:
- Fanuc CNC control;
- Precision roller ways for all axes;
- Linear glass scales for all axes;
- Ability to use any abrasive;
- Liquid cooled grinding spindle;
- Spindles available from 3hp up to 150hp;
- Full machine enclosure;
- X-axis – 24" up to 240" of travel in 12" increments;
- Y-axis – 12" up to 36" of travel in 6" increments;
- Z-axis – 6" up to 24" of travel in 6" increments; and
- Table top up to 36" wide and 24" long with other sizes available in 6" increments.
EASTEC BOOTH #1427
Campbell Grinder Company
Spring Lake, MI
campbellgrinder.com
Groove 'n Turn Toolholders
The line of Thinbit GROOVE ‘N TURN toolholders are available in 0.750" and 1.00" square and are used for machining of undercuts and thread reliefs at a 30o/60o angle. The toolholders can be used on conventional, Swiss, and CNC machines for grooving inserts in sizes from 0.004" to 0.150". They are available in three grades of material: D2 for steels, D5 for non-ferrous and HSS. TiN, TiCN, TiAlN are available. Full selection of radius and special configurations are available. The entire THINBIT line of cutting tools will also be on display.
EASTEC BOOTH #5348
Kaiser Tool Co.
Fort Wayne, IN
kaisertool.com
Pump Models Deliver 90,000PSI Waterjet Cutting
The X-Stream produces 50% more pressure than a 60,000psi intensifier pump, resulting in a 40% to 50% increase in productivity for many materials. Compared to a 60,000psi pump, typical operating pressures of 75,000psi use 30% less water, 30% less power, and up to 50% less abrasive, resulting in a 40% reduction in operating costs. The xP90-50 is capable of producing flow rates of 0.7gpm and supports up to a 0.011" orifice. The xP90-100 is capable of producing flow rates of 1.45gpm and supports up to a 0.017" orifice.
Also shown will be the 90,000psi (6,200bar) X-Stream waterjet intensifier pump and the Mid Rail Gantry precision waterjet cutting machine. Capable of producing complex parts out of virtually any material, the Jet Edge Mid Rail Gantry waterjet cutting machine features an exposed tank that easily accommodates overhead loading. It comes standard with one abrasive-jet cutting head; while the option to add a second cutting head allows an increase in productivity.
The Mid Rail Gantry is ballscrew-driven for higher accuracy, while the sturdy heavy-wall tubular steel construction eliminates vibration and increases longevity. The Mid Rail Gantry utilizes an industrial PC controller and all three axes are fully programmable (Z optional). It also features direct-couple AC brushless digital servomotors and single or double carriages. Protection of critical bearing components with heavy metal covers with brush seals and positive air pressure ensure accuracy.
EASTEC BOOTH #1128
Jet Edge
St. Michael, MN
jetedge.com
Efficient Trunnion Table with 5-axis Technology
The VMX30U 5-axis machining center, TMX10MY high performance multi-tasking turning center with sub-spindle, and the 3-axis VM20 equipped with a rotary table will be on display and will be featuring the benefits of WinMax8, the newest release of Hurco software that powers its integrated control.
The VMX30U offers an efficient trunnion table design, with an advanced 5-axis technology that simplifies the complexities of producing parts and molds with swept surfaces and contours. For customers who do not have simultaneous 5-axis work right now, Hurco 5-axis machines include the five-sided solution that will make each part more profitable.
The multi-tasking TMX10MY saves time at every turn – less setups, less material handling, faster servo turret instead of hydraulic, faster rapids, and more horsepower. The TMX10MY also delivers high surface finish with all digital controls, drives, and motors with absolute encoders on all linear axes.
The VM20 has an incredibly small working footprint (96.8" x 70.8") for such a large work envelope (40" x 20" x 20"). The VM20 includes a 40-taper, 10,000rpm spindle and a 20-pocket, swing-arm tool changer.
The VM20, TMX10MY, and VMX30U feature the integrated Hurco control powered by WinMax software.
EASTEC BOOTH #1205
Hurco Companies Inc.
Indianapolis, IN
hurco.com
CNC Programming Solutions
CAMWorks 2011 provides significant capabilities including enhanced automation, improved knowledge-based machining information, and smarter toolpaths. CAMWorks 2011 introduces VoluMill, a high-performance toolpath plug-in engine for high-speed milling for 2.5-axis and 3-axis roughing operations. It is ideal for prismatic parts and complex 3D shapes, as its algorithms result in more intelligent toolpaths to machine pockets, slots, and arbitrary shapes.
For the mold and die industry, Geometric has introduced an optional electrode design solution ElectrodeWorks, which automates all aspects of the calculation and design of EDM electrodes including design, management, documentation, and manufacturing. Its seamless integration with SolidWorks/CAMWorksSolids assures complete parametric association of data.
Feature Recognition is used to identify areas to be machined, has been upgraded to find more features while decreasing computation times by more than 50% over previous CAMWorks versions.
Additional enhancement with CAMWorks 2011 includes improved performance and enhanced feature recognition of slot features with fillet and taper as well as slots with islands. Users can now define customized turn inserts when it is not possible to machine, completely, a turn part using a standard turn insert. Such custom turn inserts can be defined for inner as well as outer diameter.
EASTEC BOOTH #5458
Geometric Technologies
Scottsdale, AZ
geometricglobal.com/products
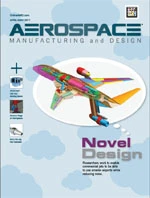
Explore the May June 2011 Issue
Check out more from this issue and find your next story to read.
Latest from Aerospace Manufacturing and Design
- Lithuanian airline Jump Air orders 20 ERA aircraft
- Last call for July’s medical manufacturing Lunch + Learn!
- Piper Aircraft receives its largest ever domestic trainer order
- Miniature, high force-to-size linear voice coil servo motor
- MagniX, Robinson to develop battery electric R66 helicopter
- Zero-point clamping modules
- Hartzell electric engine propeller earns FAA approval for AAM
- Thin profile flame and thermal barrier