After assessing extent and degree of damage, and removing the damaged materials, the original core materials and faceskin laminate plies will be replaced to form the repair patch. Source: Abaris TrainingThe basics of composite repair remain largely the same regardless of where they are used or how they are made.
They are:
- Inspect to assess damage (extent and degree);
- Remove damaged material;
- Treat contaminated material;
- Prepare repair area;
- Complete composite repair; (e.g. replace damaged material and bolt or bond a patch);
- Inspect repair for quality assurance (e.g. delaminations, inclusions, proper cure, etc.); and
- Restore surface finish.
However, the decisions made in designing a composite structure, such as thickness, solid laminate or cored construction, shape and curvature, and use of bonded integral stiffeners, all affect what types of inspection and repair will be cost-effective and even possible, in turn affecting overall life-cycle cost.
Bonded Repair
Many composite structures on aircraft consist of thin skins bonded to honeycomb or foam core. These always use bonded repairs, because thin composite laminates do not handle lateral bearing loads well, such as those transmitted by mechanical fasteners in bolted repairs. Bonded repairs are typically called tapered or scarfed repairs because they require tapering the repair area around the removed damage plies in preparation for adhesively co-bonding a composite repair patch. This provides the best load transfer and helps to ensure a sufficient adhesive bond by maximizing bond surface area.
Meticulous surface preparation is also required. Bonded repairs use elevated temperature cures. This is because the bonded repair patch replaces the original composite laminate, which is commonly made from uni-directional or fabric reinforcement, pre-impregnated with 250°F or 350°F cure resin. These higher temperature cures are achieved using portable repair equipment, typically called hot bonders. They require electrical power and clean compressed air for vacuum, and use thermocouples and computer control programs to manage heat blankets, heat lamps, ovens, or other heat sources. Vacuum is used in the fabrication and repair of composite structures, both to extract air and volatiles and to apply compaction pressure for minimum voids and maximum mechanical properties.
Bolted Repair
Composite structures that do not use a core are typically referred to as monolithic, a term that may also imply a thicker laminate where all of the plies are roughly the same material (e.g. all carbon fiber prepreg). The new Boeing 787, Airbus A350, and Bombardier C-Series commercial airliners feature many large, monolithic composite structures. However, most of the in-service damage to these aircraft will be similar to the most common types of damage on current airliners, namely to wingtips, control surfaces, landing gear doors, radomes, etc. These structures are similar to composite structures on current aircraft, and will be repaired using current techniques. The large, thicker, monolithic structures will most likely be repaired with bolted repairs. This is because the taper (scarf) distance necessary for load transfer is determined by the thickness of the laminate.
A crude rule of thumb is to taper sand from 0.25" to 0.5" of area per ply of composite laminate. For thick laminates – e.g. 100 plies – the large areas required to be scarfed (taper sanded) require too much time and cost to be practical. In general, laminates with a thickness of 0.125" or less should use bonded repairs, unless the local fastener area thickness is built up, while laminates over 0.500" in thickness should use bolted repairs.
This is a very general discussion and the actual recommended procedures vary greatly with the specific details of each structure and repair.
Bolted composite repairs require a greater edge distance to prevent fastener pull-out and use different fasteners than those used with aluminum sheet metal. The general rule for fasteners in aluminum is that they must be spaced at least two times the fastener diameter from the edge. For composites, this required edge distance is four times the fastener diameter (e.g. 0.125" diameter hole requires 0.250" edge distance in aluminum but 0.500" in composites).
Special large-head, expanding-sleeve fasteners are also required, designed to be squeezed versus bucked during installation for an interference fit so as not to cause delamination in the composite plies. Cadmium-plated steel fasteners, commonly used in aluminum aircraft structures, will deteriorate due to galvanic corrosion if used in carbon fiber composites. This is because cadmium and aluminum are adjacent on the scale of corrosion potential, while carbon fiber is at the opposite end. Therefore, fasteners used in bolted repairs to carbon fiber composites may be stainless steel, monel, titanium, or other non-corrosive metal. This is not an issue, however, with fiberglass or aramid fiber composites.
For quality assurance, bolted repairs are easier to inspect than the adhesive bond of a scarfed repair, however, they are easily noticed, are heavier, and disrupt a structure’s aerodynamic surface. They are heavier not only due to the addition of fasteners, but also because the fastener holes disrupt the composite’s continuous reinforcement, reducing strength and stiffness and creating local stress concentrations. All of this must be addressed in the design of the repair patch.
Other Considerations
What repair is specified depends on the type of structure (e.g. flight-critical primary or non-critical secondary), size of damage, and time frame. Manufacturers are exploring bolted and bonded repair options, and some may offer quick composite repairs as well. Bolted repairs for the newer, thick monolithic structures will include mechanically fastened doublers made from titanium, aluminum, and composite materials. Airframe manufacturers are also trying to validate bonded repair capability. There are several repair techniques using non-autoclave processes to obtain high-quality, very low porosity repair laminates. Some of these techniques have been in existence for many years, and are now being tested and refined specifically for the thick, monolithic composite structures on the latest commercial airliners. These techniques enable bonded repairs to be cured in place on the aircraft using only vacuum bagging and normal hot bond curing equipment.
Quick composite repairs would only be for small areas of damage to non-critical structures, and would use a repair patch kit to enable bonding a composite repair patch to a damaged area possibly within one hour. Explicit limits for the types and sizes of damage repairable with this type of kit would be published in the Structural Repair Manuals for each specific aircraft.
Before a repair can be made, the extent of damage has to be determined. Ultrasonic testing (UT) equipment is the most common method for inspecting damage on composite aircraft structures. It sends high-frequency sound waves into the composite laminate and analyzes the reflections for damage and defects. Interpretation of the data demands careful analysis, requiring extensive skill, training, and experience. However, in conjunction with the effort to develop quick composite repair kits, it has been reported that a large manufacturer of UT equipment has developed a handheld ultrasonic tool, easily operated without intensive training, which will diagnose whether damage must be repaired. This greatly simplified tester could be used to scan the damaged area, giving a green light if the laminate is good and a red light if the damage must be repaired.
Another consideration that aircraft manufacturers are dealing with is the issues involving low energy impacts, such as a tool drop. This type of impact may cause the structure to be slightly damaged within the laminate, while no damage is visible on the exterior. If the damage is not visible then it may not be detected, and in turn not repaired, until a heavy check is performed – one that is designed to detect this level of damage. We will discuss this issue of non-visible and barely visible damage further in our next article, specifically the requirements of designing for repair access versus damage tolerance, including implications on weight, aircraft down-time, and life-cycle cost.
A more detailed discussion about repair is provided in the free, online composite repair course offered at abaris.com/repaironline, with no sign-in required.
Abaris Training
Reno, NV
abaris.com
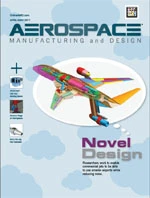
Explore the May June 2011 Issue
Check out more from this issue and find your next story to read.
Latest from Aerospace Manufacturing and Design
- Essential strategies to protect your data
- NASA selects instruments for Artemis lunar terrain vehicle
- Twin-cutter boring head
- Bell awarded funding for X-plane build phase of SPRINT program
- Shaft coupling clamps
- #46 Lunch + Learn Podcast with SMW Autoblok
- Gleason Corp. acquires the Intra Group of Companies
- Thread milling cutter reduces cutting pressure, vibration