
Concept Systems
Historically, deburring and material removal has been done manually. However, with today’s standards requiring high levels of consistency, parts must be manufactured with a material removal process that increases throughput and reduces risk. Incorporating automation with the right robot and the right tooling deburrs parts faster, more efficiently, with fewer risks or errors.
Working with aluminum may seem daunting due to its challenges; it’s soft and prone to high levels of rework and scrap. With a robotic material removal system, manufacturers can achieve a higher level of process control when producing to specifications.
Concept Systems, a system integrator in Albany, Oregon, serves manufacturing companies across many industries, streamlining challenges and delivering platform-independent solutions that increase yield, decrease waste, and promote higher levels of productivity and efficiency.
Despite scores of successful applications, integrators often face challenges in getting customers on board with new technology. Concept Systems designed and implemented an automated material removal system for a well-known manufacturer in the aerospace industry. The customer was using manually-operated die grinders to apply an edge-break to machined aluminum components, but felt uncertain about moving to an automated material removal system after using manual techniques for so many years. Concept Systems had to verify the proposed solution would meet or exceed the customer’s current specifications for quality and throughput as part tolerances and specifications are critical in aerospace.
Many manufacturers believe drilling and grinding by hand are best because human hands can feel and compensate for variation in part geometry, however, work can be inconsistent, leading to high levels of rework and scrap. Manual work can also be affected by the ever-widening skills gap, as high turnover can lead to more quality issues and potential injuries. Automating material removal processes can address these issues.
Fanuc robots and ATI Industrial Automation’s robotic deburring tools helped Concept Systems bring its vision for robotic material removal to light. From an operation side, Concept Systems’ design yields higher quality finished goods and dramatically increases the customer’s throughput.
“We were able to produce parts under real-world tolerance stack-ups at a consistency we believe to be about twice as fast as the manual process,” says Ryan Wasmund, Concept Systems sales and marketing director.
Such results can help manufacturers maintain a competitive edge. The potential is even more significant for aluminum manufacturers because working with aluminum can be more complicated than other materials.
Aluminum has a high strength-to-density ratio, so it is commonly used in automotive and aerospace manufacturing. When machined, the softer metal produces burrs that have sharp, uneven edges of the workpiece that influence the dimensions and create a hazard for workers handling them. Aluminum deburring processes must remove burrs and break edges without gouging into the material – which is arguably why manual methods are so popular. A successful robotic material removal system would have to balance several factors: aluminum’s malleability, tooling speed, and robot agility.
The system
Concept Systems integrated the Fanuc M710iC and ATI’s RS-340 radially compliant deburring tool in their material removal system. ATI’s RS-340 light-duty, general purpose tool is well suited for aluminum deburring tasks. The right amount of speed and handling provides enough power to remove material and validate the edge break while maintaining low cycle times and reducing scrap. The single-axis compliance of the RS-340 ensures that the tool returns to a repeatable center and maintains surface finish by reducing chatter in the part path.
With ATI deburring tools, Concept Systems developed a robotic material removal solution for its customer, enabling them to produce higher quality parts in less time. The solution reduces scrap and rework and alleviates safety concerns associated with hand-grinding parts. For operators, the robotic process comes with a transition to more engaging jobs and opportunities for growth and skill development. At its best, automation makes processes easier for everyone involved.
See the Fanuc MC 710iC deburring process in action: https://tinyurl.com/y279rrw9

Thomson Industries expands
Mechanical motion control solutions maker Thomson Industries is consolidating operations from a Connecticut subsidiary to its Marengo, Illinois, facility, bringing more than 50 new assembly, soldering, machine operation, buying, and planning jobs to the region.
“With some 225 employees, the Marengo plant is the largest Thomson plant in the U.S., and we take great pride in the talented people who work here,” says Thomson President Scott Benigni. “They have contributed significantly to our steady business growth and global reputation for impeccable product quality.”
The plant expansion is the result of moving the Thomson-affiliated Warner Linear product line from its current location of New Hartford, Connecticut. Thomson and Warner Linear rod-style electric linear actuators are used to control push/pull type motion in various products.

Positioning cylindrical products
Hydraulic upenders with V-cradle design position rolls of coils, spools, tubular tanks, and other cylindrical products. With a 6,000 lb capacity, these ergonomic positioning devices have enough power to re-position heavy loads, while the V-cradle keeps the load intact during movement. All Verti-Lift hydraulic upenders feature 0° to 90° tilt angles, hold-down tabs on all corners; heavy-duty cylinders for maximum service life; 110VAC single-phase motors with 15A draw; and standard hand controls for lowering/raising tilt. Optional accessories include foot control, oversized platforms to suit specific material handling requirements, roller conveyors, accordion skirts, remote power units, and programmable logic controller (PLC). Hydraulic upenders are also suitable for the safe re-positioning of pallets loads and odd-shaped objects.
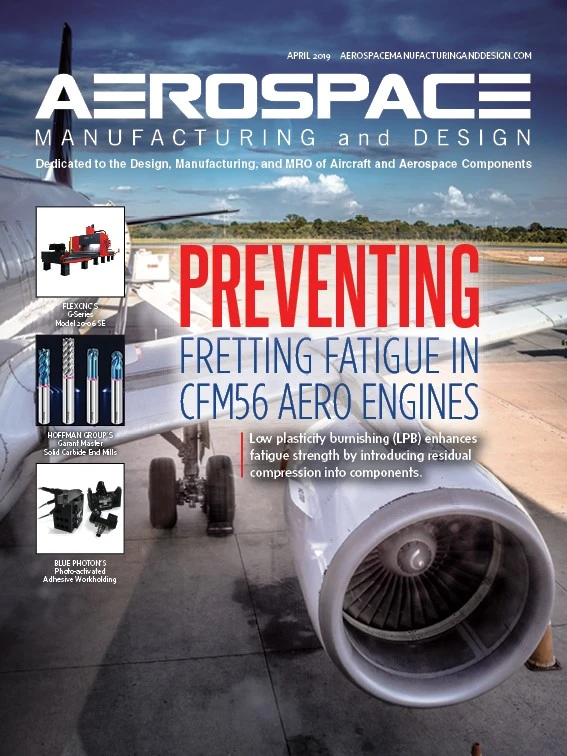
Explore the April 2019 Issue
Check out more from this issue and find your next story to read.
Latest from Aerospace Manufacturing and Design
- Drop in for an interactive webinar on automation in manufacturing
- SW’s wing rib technology for the aerospace industry
- Mach Industries launches Mach Propulsion
- Murata Machinery USA's MT1065EX twin-spindle CNC turning center
- Electra reaches 2,200 pre-orders for its Ultra Short aircraft
- Heule's DL2 tooling for deburring of small bores
- Ralliant to establish global headquarters in North Carolina
- Philatron MIL-DTL-3432 military cables