
In mid-2012, aerospace engine supplier quality requirements were causing great complexity for supply chains. Individual requirements had a common purpose, but different approaches meant suppliers had to have more complex management systems. So, several aerospace engine manufacturers and suppliers began collaborative discussions to find solutions to these problems and improve product quality.
Industry leaders reached out to SAE International as a neutral forum for collaboration, prompting the development of the SAE G-22 Aerospace Engine Supplier Quality (AESQ) Technical Committee. Led by Dr. Ian Riggs, global head of quality assurance for Rolls-Royce plc, the committee began developing standards specific to the aerospace engine supply chain.
“The challenges we were facing were bigger than any OEM could overcome on its own. As the first G-22 Technical Committee chairperson, I knew the solution hinged upon combining our efforts to bring clarity to very clouded processes,” Riggs says.
The first priority for improving supply chain quality and reducing
“The success of AS13000 proved that we were on to something big,” says Earl Capozzi, Pratt & Whitney’s supplier quality discipline chief. “That was the turning point when it became apparent that this approach would vastly improve our supplier relationships, productivity, and overall product quality.”
As the momentum of the G-22 committee grew, it became clear that the same collaboration process could apply outside of standards creation. In October 2015, the original member companies signed an agreement to create the AESQ Strategy Group as part of SAE’s Industry Technologies Consortia (ITC). The SAE ITC specializes in establishing and managing consortia; providing proven processes, tools, and resources that help public, private, academic, and government organizations connect; and collaborating in neutral, pre-competitive forums. The
With expanded abilities, the group took on other inconsistencies surrounding standardization including
Through the SAE ITC, the
“Our relationship with Probitas has been more successful than we ever expected. Our original goal was simply to make training easier, but the results have exceeded that,” Capozzi says. “By providing common training and certification options, we’re seeing individuals stay at shops longer and requiring less training than before. There’s a lot more
To date, more than 4,000 DPRV delegates have completed the training course, surpassing the AESQ’s original goal of having 4,000 personnel complete the course within the first three years. At this rate, the strategy group expects an additional 6,000 delegates will complete the course in the next three years. Additionally, the AESQ enacted a three-year recertification cycle, consolidating certification cycles and creating consistent terms for organizations using DPRV programs.

The benefits have been significant and immediate. Simplified training logistics featuring onsite, in-region, and reduced training time all contribute to supplier and customer cost savings. Coupled with the efficiencies gained from the standards that started it all, the AESQ’s single training program has saved the industry more than $50 million by reducing travel expenses for delegates training, lowering downtime spent on training, and eliminating redundant customer training programs. At AESQ Supplier Forums, participants saved, on average, several thousand dollars per DPRV delegate in lost work time and travel expense reductions.
“The majority of our standards and training users are large corporations. Initially, they were skeptical that the standards would catch on. Now that we’re a few years in, they’re seeing the results really come to fruition,” Capozzi says. “The real turning point was when suppliers began seeing our standards and certification requirements called out in purchase orders – that’s when it took on a life of its own.”
Complementing existing IAQG and ISO standards, the SAE G-22 standards are filling gaps that have historically led to waste. Building off feedback from the initial five standards published, the committee continues working on new standards, with four more expected to be deployed in the next year.
“Before the standards committee and before the strategy group, we were just a group of companies all looking for solutions to a big problem. We had to look beyond our own walls to find solutions for improving supply chain performance,” Capozzi says. “What we’ve ended up with is a flexible roadmap that not only serves our
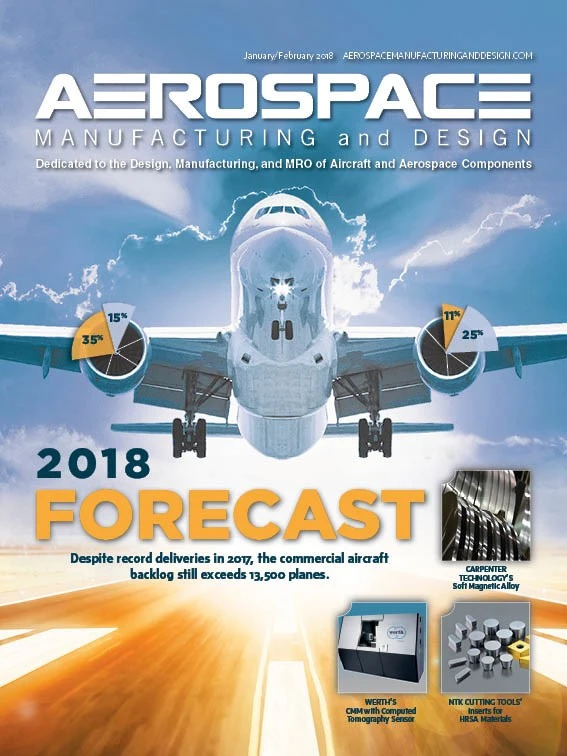
Explore the January February 2018 Issue
Check out more from this issue and find your next story to read.
Latest from Aerospace Manufacturing and Design
- NASA selects instruments for Artemis lunar terrain vehicle
- Twin-cutter boring head
- Bell awarded funding for X-plane build phase of SPRINT program
- Shaft coupling clamps
- #46 Lunch + Learn Podcast with SMW Autoblok
- Gleason Corp. acquires the Intra Group of Companies
- Thread milling cutter reduces cutting pressure, vibration
- Malaysia Aviation Group orders 20 more Airbus A330neo widebodies