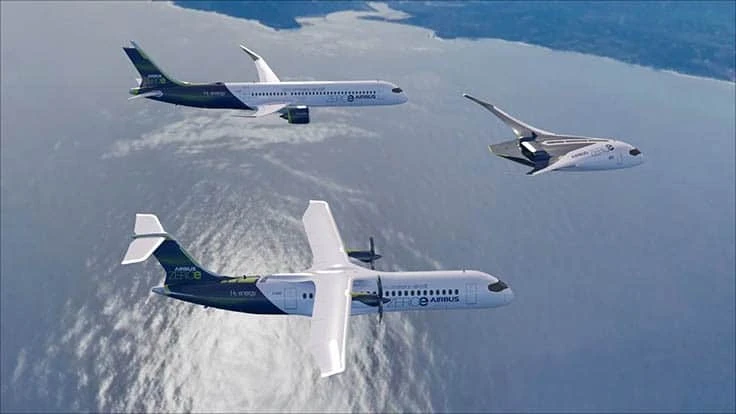
Airbus SE
By 2035, the world’s first zero-emission commercial aircraft could take to the skies. To bring this vision to reality, Airbus is exploring concept aircraft – known as ZEROe – powered by hydrogen, a disruptive zero-emission technology with the potential to reduce aircraft emissions up to 50%.
At first glance, the three recently unveiled Airbus concept aircraft offer little more than a sense of déja vu. One looks remarkably like a classic commercial aircraft – except with longer, more flexible wings. Another resembles a turboprop-powered airliner with its arrangement of eight-bladed propellers. And the third is a blended-wing body design that has seen some traction among engineers over the last year.
Upon closer inspection, the trio features one game-changing difference compared to predecessors: hydrogen propulsion.
“As recently as five years ago, hydrogen propulsion wasn’t even on our radar as a viable emission-reduction technology pathway,” explains Airbus Vice President, Zero-Emission Aircraft Glenn Llewellyn. “But convincing data from other transport industries quickly changed all that. Today, we’re excited by the incredible potential hydrogen offers aviation in terms of disruptive emissions reduction.”
That is the objective. Airbus recently announced its ambition to develop the world’s first zero-emission commercial aircraft by 2035. This means only the most disruptive zero-emission technology to reduce the aviation industry’s climate impact will need to be rigorously tested and evaluated. And hydrogen certainly stands out from the pack: according to internal calculations, Airbus estimates hydrogen has the potential to reduce aviation’s CO2 emissions up to 50%.
In aircraft, there are two broad types of hydrogen propulsion: hydrogen combustion and hydrogen fuel cells. Airbus’ three zero-emission (ZEROe) concept aircraft are all hydrogen-hybrid aircraft powered by modified gas turbine engines that burn liquid hydrogen as fuel. At the same time, they also use hydrogen fuel cells to create electrical power that complements the gas turbine, resulting in a highly efficient hybrid-electric propulsion system. However, each option has a slightly different approach to integrating the liquid hydrogen storage and distribution system. Airbus engineers have conceptualized integration solutions that carefully consider the challenges and possibilities of each type of aircraft.
Turbofan: Two hybrid-hydrogen turbofan engines provide thrust. The liquid hydrogen storage and distribution system is located behind the rear pressure bulkhead.
Turboprop: Similar to the turbofan aircraft, this concept’s liquid hydrogen storage and distribution system is located behind the rear pressure bulkhead. However, two hybrid hydrogen turboprop engines, which drive the eight-bladed propellers, provide thrust.
Blended-Wing Body (BWB): This configuration features an exceptionally wide interior, thereby opening multiple options for hydrogen storage and distribution. In one example, the liquid hydrogen storage tanks are stored under the wings. Like the turbofan aircraft, two hybrid hydrogen turbofan engines provide thrust.
“Hydrogen has a different volumetric energy density than jet fuel, so we have to study other storage options and aircraft architectures than existing ones,” explains Airbus Executive Vice President, Engineering Jean-Brice Dumont. “This means the visual appearance of our future zero-emission aircraft will change. These three configurations provide us with some exciting options for further exploration.”
If hydrogen technology development progresses at the expected rate, Airbus’ first zero-emission commercial aircraft is expected to roll off the assembly line for entry-into-service by 2035.
To meet this ambitious 2035 target, Airbus will need to launch the ZEROe aircraft program by 2025. This time frame gives Airbus engineers approximately five years to mature all the required hydrogen technologies. During the coming months, several hydrogen demonstrator programs – which will test hydrogen fuel cell and hydrogen combustion technologies – are to be formally launched. A full-scale aircraft prototype is estimated to arrive by the late 2020s.
Latest from Aerospace Manufacturing and Design
- Heart Aerospace relocates to Los Angeles
- Fixtureworks introduces Stablelock Clamps
- Piasecki acquires Kaman's KARGO UAV program
- PI Americas’ long-travel XY piezo nanopositioners-scanners
- AAMI project call submission deadline extended to May 12
- Jergens launches cast iron tooling column additions
- Airbus to acquire assets relating to its aircraft production from Spirit AeroSystems
- FANUC America's Cobot and Go web tool