
Phillips Service Industries Inc. (PSI) metal additive manufacturing (AM) solutions subsidiary Sciaky Inc. has delivered an industrial- scale Electron Beam Additive Manufacturing (EBAM) 110 system to Airbus. The aircraft manufacturer will use the metal 3D printing system to produce large titanium structural parts.
Starting with a 3D CAD model, the unit’s articulated, moving electron beam heat source deposits metal via wire feedstock, layer by layer, producing a near-net shape part with minimal material waste, ready for heat treatment and post-production machining.
The EBAM 110 system’s work envelope is 70" x 47" x 63" (1,778mm x 1,194mm x 1,600mm). Sciaky EBAM systems can produce parts ranging from 8" (203mm) to 19ft (5.79m) in length, with gross deposition rates ranging from 7 lb to 20 lb (3.18kg to 9.07kg) of metal per hour.
The Interlayer Real-time Imaging and Sensing System (IRISS) monitor and control system senses and digitally self-adjusts metal deposition for consistent part geometry, mechanical properties, microstructure, and metal chemistry. www.sciaky.com; www.airbus.com
Spatial, Renishaw update QuantAM
Dassault Systèmes subsidiary Spatial Corp., a provider of 3D software development toolkits, and industrial automation and process control supplier Renishaw have released a new version of Renishaw’s QuantAM software.
QuantAM build preparation software is used to generate the printer’s laser scan paths that fuse the powder layers to additively form a part. Instead of relying on a slice tessellation language (STL) CAD export format describing a part as a collection of connected triangles, QuantAM uses 3D ACIS modeling with CGM Polyhedra and 3D InterOp development toolkits.
“The STL format can cause issues, typically with broken descriptions that need healing, or with low triangle density impacting print quality,” says Stephen Anderson, director of group software at Renishaw.
The collaboration with Spatial allows high-quality healing on STL files, direct import of various CAD formats, precise B-rep and polyhedral hybrid modeling capabilities, and the ability to edit 3D models directly.
“Rather than rely on a triangulated view of the 3D model, a far better approach is to work on the native geometry, preserving the original design intent of the model,” says Brian Rohde, Spatial’s marketing manager for the 3D ACIS modeler. www.renishaw.com; www.spatial.com; www.3ds.com
Aerospace 3D printing market to grow at 55.85% CAGR to 2020
Analysts forecast the global aerospace 3D printing market to grow at a compound annual growth rate of 55.85% during the period 2016 to 2020. Contributing to the market’s growth is increasing demand for production of lightweight and smaller engine components for greater fuel efficiency and lower operating cost.
Another market trend is 3D printing of aircraft interior air ducts, wall panels, and seat framework. By combining features in one part, 3D printing reduces material usage, attachment hardware, and overall weight. Carriers can accommodate more passengers by adding lightweight 3D-printed seats with complex geometries and organic shapes.
The Global Aerospace 3D Printing Market 2016-2020 report analyzes five major companies and provides 23 data exhibits. www.reportsnreports.com
Get curated news on YOUR industry.
Enter your email to receive our newsletters.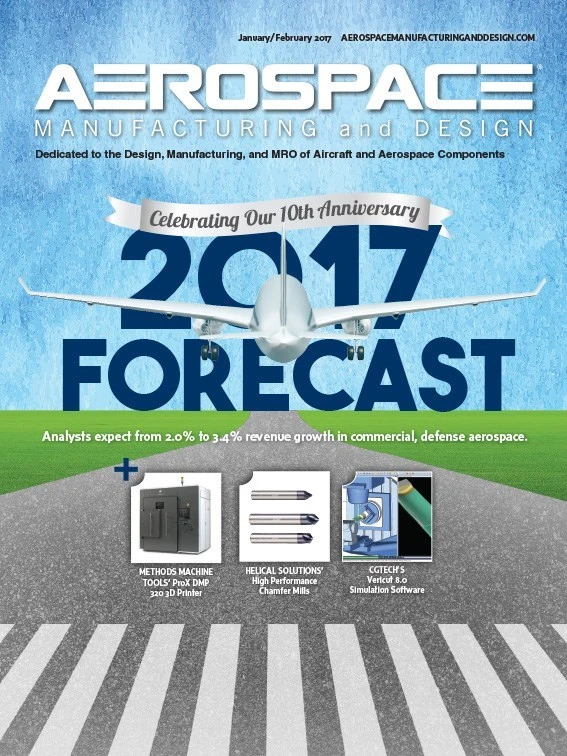
Explore the January February 2017 Issue
Check out more from this issue and find your next story to read.
Latest from Aerospace Manufacturing and Design
- Beyond Aero refines its hydrogen-electric light jet
- Americase's advanced protective solutions
- GE Aerospace secures Air Force engine contract
- Thomson Industries' online sizing and selection tool
- #53 - Manufacturing Matters - 2024 Leaders in Manufacturing Roundtable
- Join us for insights on one of the hottest topics in manufacturing!
- You can still register for March’s Manufacturing Lunch + Learn!
- Ohio creates Youngstown Innovation Hub for Aerospace and Defense