
small-sized, pilotless aircraft made using additive layer manufacturing is Airbus’ testbed for futuristic aircraft technologies. The mini aircraft project, Testing High-tech Objectives in Reality (THOR), uses 3D-printed structural parts, advanced aerodynamics, and artificial intelligence.
The initial THOR version weighs approximately 21kg and can fit in a 4m square. It is powered by two 1.5kW electrically driven propellers, and 90% of its structural components were 3D-printed from plastic polyamide powder.
“This mini aircraft does not represent an actual airliner design Airbus is considering, rather it is a platform to enable low-risk and fast-track development of different technologies in real flying conditions,” explains Detlev Konigorski, director of the THOR project for Airbus’ Emerging Technologies & Concepts activity in Germany. “The first version was to test whether the slogan ‘print me an airplane’ can be converted into reality.”
A major advantage for THOR is the short lead time of 3D-printing, which significantly reduced development time for producing the technology demonstrator compared to traditional manufacturing methods. Using an existing design concept, it took approximately seven weeks to print the THOR aircraft’s 60 structural segments, followed by approximately one week for assembly and three days to fine tune the electrical systems before it was flight-ready.
THOR’s initial flight occurred in November 2015, and the mini aircraft is resuming testing following its display at the recent ILA Berlin Air Show.
“The first flight was simply about flying,” Konigorski says. “Now, we want to generate basic data on things such as altitude, speed, and acceleration in a turn.”

Follow-on THOR versions currently are being assembled at the new Center of Applied Aeronautical Research (ZAL) in Hamburg, Germany, in which Airbus is a major partner and shareholder. These aircraft will feature a modular design allowing for greater flexibility in airframe and structural testing.
For example, the second THOR version will accommodate interchangeable wings, including concepts for a hexagonal wing with support structure derived from a honeycomb design; a metallic aluminum wing; and a flexible wing made from carbon-fiber reinforced plastics.Once wing testing is complete, the THOR project will focus on artificial intelligence in collaboration with the Airbus Defense and Space business unit of Airbus Group. The goal is for a THOR aircraft to land completely on its own, identifying obstacles on the runway and determining whether it is safe to touch down.
Another important aspect of the THOR project is the team’s willing-to-fail approach, which helps push the envelope of experimentation. The goal is simple: implement high-risk ideas on flying vehicles as soon as possible.
“If a THOR aircraft takes off, and after 30ft makes a nose-dive back to the ground, our attitude is: ‘good, let’s sweep it off the runway and come up with a better idea,’” Konigorski says. “In a few weeks, we can print a new aircraft!” www.airbus.com
![]() | The Garden Center Conference & Expo, presented by Garden Center magazine, is the leading event where garden retailers come together to learn from each other, get inspired and move the industry forward. Be sure to register by April 17 to get the lowest rates for the 2025 show in Kansas City, Missouri, Aug. 5-7.
|
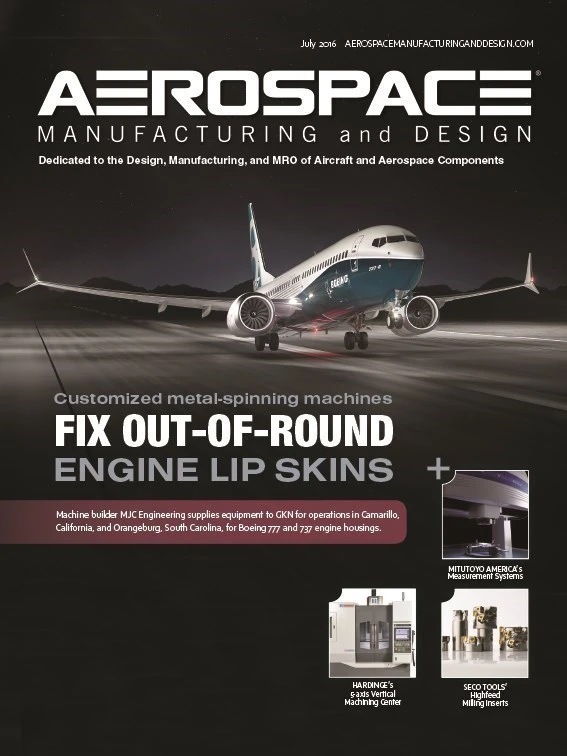
Explore the July 2016 Issue
Check out more from this issue and find your next story to read.
Latest from Aerospace Manufacturing and Design
- GE Aerospace awarded subcontract for FLRAA next phase
- KYOCERA Precision Tools publishes 2025-2026 Indexable Cutting Tools Catalog
- BOC Aviation orders 120 Airbus, Boeing jetliners
- Mazak’s INTEGREX j-Series NEO
- Embraer tests wing for new technologies demonstrator
- Mitutoyo America’s SJ-220 portable surface roughness tester
- #55 - Manufacturing Matters - A Primer on Defense Contract Manufacturing
- Registration is open for April’s Manufacturing Lunch + Learn!