
The European Space Agency (ESA) and U.S. National Aeronautics and Space Administration (NASA) are building and transporting delicate, heavy, and unwieldy objects. Teams work in pristine cleanroom environments to protect sensitive equipment from contamination that could cause millions of dollars in damage. There’s no margin for error here. A single particle of dust could be catastrophic.
They need a material handling solution that ensures the safe movement and positioning of sensitive and expensive equipment in a cleanroom environment without causing damage. ESA and NASA use pallets with air casters, like a hovercraft or air hockey table, to move loads easily with little risk and maintain faultless cleanroom conditions.
Clearing the air about air casters
Aerospace equipment and vehicles such as satellites and spacecraft are built, tested, and maintained in cleanroom environments since they contain fragile electronics and vulnerable lenses and mirrors that must remain immaculate to function properly. Potential threats include exposure to residues, condensation, off-gassing, electrostatic forces and discharges, microscopic particles leading to de-calibration of equipment, underperformance, or outright failure.
Air casters work in these environments by lifting heavy loads on a thin layer of air in a flexible donut-shaped airbag. The compressed air-filled bag snaps into place, and creates a secure seal around the floor with excess air seeping between the bag and the floor. The result is a thin film of air less than 0.005" thick, enough to reduce the friction coefficient to less than 1%. Frictionless movement allows single operators to safely move loads weighing as much as 5,000 lb. Operators don’t require training or certification since standard shop air inflates the air casters.
Air casters are cleanroom-friendly material handling options because they’re relatively small, self-contained, and can move omnidirectionally, including rotating in place. They don’t need the space of a forklift and they’re much more flexible and less expensive than cranes. They produce no particulates and control particles on the floor with a skirt attachment that fits around the air caster and hooks into a vacuum system. Air casters don’t produce exhaust emissions, don’t contain any bearings to be greased, or create volatile organic compounds (VOCs), and have no impact on condensation, humidity, or electrostatic accumulation.

Before Orion crew vehicles fly, they float
Orion crew exploration vehicles are constructed in a facility designed for air casters and to support missions to the International Space Station (ISS) as a joint project between Lockheed Martin and NASA.
“Orion is a critical component for NASA’s deep space exploration plans,” NASA officials wrote on the transfer of Lockheed Martin’s ownership of the Orion spacecraft for the Artemis I mission. “During Artemis I, the spacecraft will launch on the most powerful rocket in the world and fly farther than any spacecraft built for humans has ever flown.”
NASA assembles Orion spacecraft at the Neil Armstrong Operations & Checkout (O&C) Building at Kennedy space center in Florida, which includes a Class 100,000 cleanroom and portable cleanroom facilities.
“We have learned a lot about how to design and manufacture a better Orion… Driving down cost and manufacturing them more efficiently and faster will be key to making the Artemis program a success,” says Mike Hawes, vice president and Orion program manager for Lockheed Martin Space.

Material handling challenges disappear
Air casters provide smooth and frictionless movement while avoiding interference with equipment calibration. The frictionless motion of air casters allows handling heavy loads without jarring or vibration and isolate the load from imperfections in the floor that could transmit vibrations or shock.
Air casters fit underneath and within the footprint of the load, evenly distributing it, reducing surface loading so air casters can work on fragile raised floors or floors with expensive surface treatments, protecting against wear and formation of grooves and divots.
“A lot of the things we did to the facility was to make it more flexible,” Lockheed Martin’s former director for Orion assembly Jim Kemp says. “The investment that you make when creating a facility this way – which is actually less expensive to build –is that you have full flexibility in reconfiguring your factory. And if you design all your tooling and equipment to move very readily in that factory, you can redesign the building in rapid fashion.”
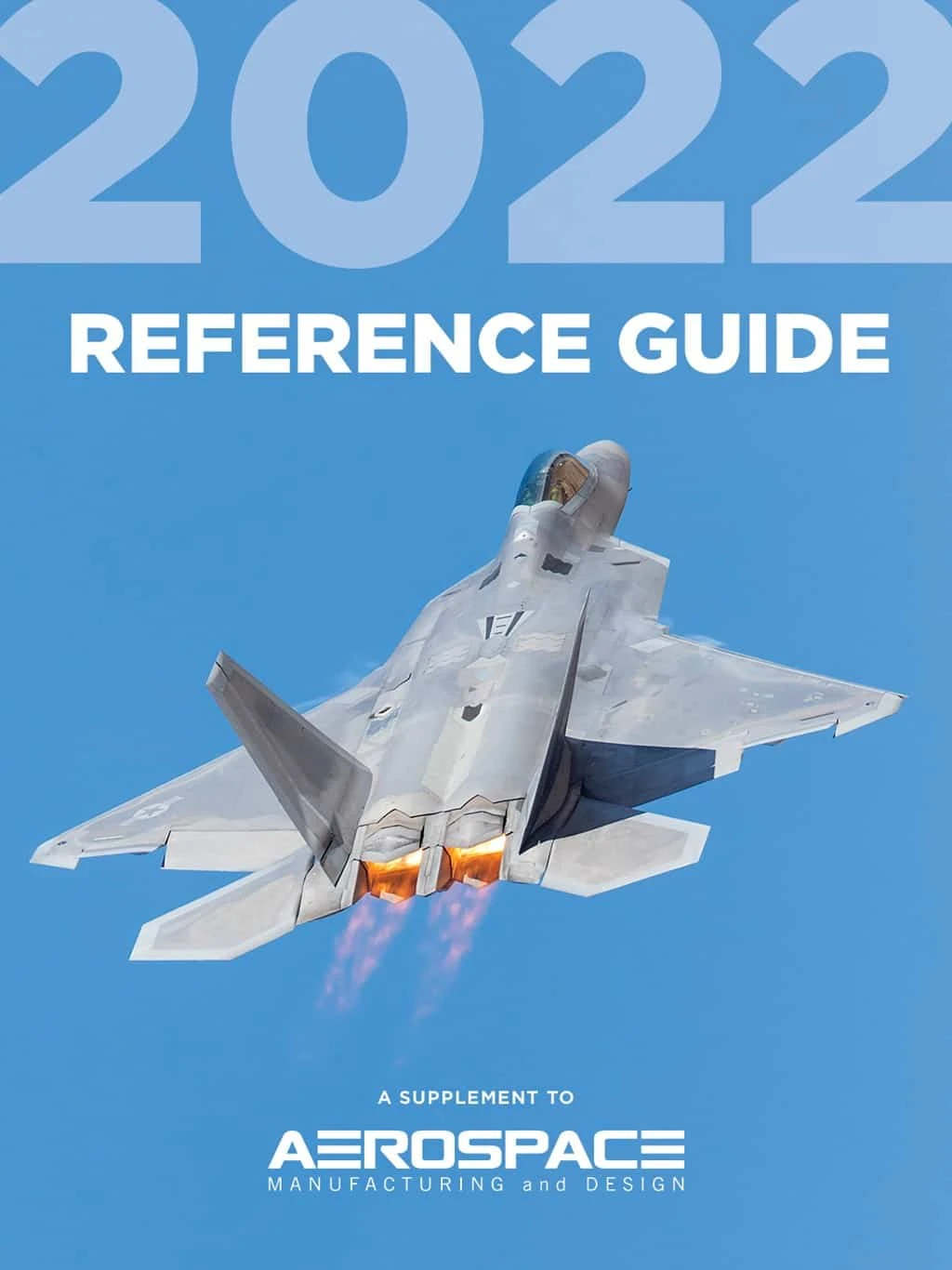
Explore the AMD Reference Guide 2022 Issue
Check out more from this issue and find your next story to read.
Latest from Aerospace Manufacturing and Design
- Piasecki acquires Kaman's KARGO UAV program
- PI Americas’ long-travel XY piezo nanopositioners-scanners
- AAMI project call submission deadline extended to May 12
- Jergens launches cast iron tooling column additions
- Airbus to acquire assets relating to its aircraft production from Spirit AeroSystems
- FANUC America's Cobot and Go web tool
- Chicago Innovation Days 2025: Shaping the future of manufacturing
- High-density DC/DC converters for mission-critical applications