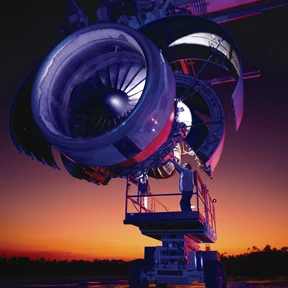
Whether you look at civil and military aviation or at space travel, every sector of the industry faced severe and painful cuts in the aftermath of the 9/11 terrorist attacks. Passenger numbers fell and the majority of airlines found themselves in a critical financial situation, a development that also hurt suppliers. Now, the industry has begun to bounce back and seems to be taking off.
UPWARD TREND
Global passenger traffic is forecasted to grow by 4.8% to 5.3% annually until 2024. Never before have so many people flown, and the numbers continue to increase. Based on average economic growth, the International Civil Aviation Organization (ICAO) and the European Development Fund (EDF) estimate 3.5 billion passenger miles for 2015 and between 8.5 and 14 billion by 2050. Assuming a world population of 10 billion in 2050, this would mean the average person would travel 880-1,400 miles per year by plane. This trend is similar for airfreight volumes; Airbus experts are expecting an increase of between 5.9% and 6.2%.
Boeing has already sold out of their 787 Dreamliner production through 2011. They estimate that the current global fleets of around 16,200 aircraft will expand to over 35,000 aircraft by 2024. Bearing in mind that around 7,200 aircraft will be replaced in this time frame, the industry will need another 18,500 aircraft, predicts Dirk Herrmann, a KÖRBER SCHLEIFRING expert in the market research working group of the Association of German Machine Tool Plants (VDW).
COMPLEX PRODUCTS, TOUGH MATERIALS
The majority of all activities in the aerospace engine industry are concentrated in Europe and North America. Although there is continuous talk of moving production units to Asia, so far the main focus there has been on developing service centers and limited revenue partners. The few primary engine manufacturers, along with their primary suppliers, have maintained their competitive edge by constantly updating their knowledge of the various special processes required to manufacture complex parts from advanced materials.
Aerospace manufacturers are also pushing into advanced materials for airframes and skin. For example, with a target to reduce fuel consumption by 20%, the Dreamliner's skin is comprised of two layers of composite with a thin center layer of titanium. According to John Bunting of Precorp, chips from the metal can interfere with drilling composites and carbide does not hold an edge when machining composites. So, drilling rivet holes in the Dreamliner's skin requires PDC drills. Precorp offers a proprietary tip geometry and a PCD cutting edge for this application. Composites also figure big in military aircraft like the Joint Strike Fighter, further contributing to the demand for PCD tooling.
Composites are even being used in the "cool section" of aircraft engines now, where temperatures are about 250°F. General Electric saved 400 lbs. in their GEnx engine by using composite fan blades.
STRONG PARTNERS
The United Grinding companies have always been important to the turbine and aerospace industries, providing necessary grinding and process expertise. They have unique expertise in this field, based on a large number of installations worldwide, ranging from fully automatic grinding cells to stand-alone special purpose machines. Many of these installations were developed in close cooperation with the leading turbine manufacturers.
Pratt & Whitney offers a good example: these engine specialists and their parent company United Technologies work closely with United Grinding, using machines from Blohm, Mägerle, Studer and Walter. Their Turbine Module Center in East Hartford, CT uses 38 Blohm Profimat MC CNC creep feed grinders to produce turbine blades and vanes for the "hot zone" of the engine. The Profimat MC provides a common machine platform for 3-axis and 5-axis grinding applications using plated and vitrified CBN wheels. In Pratt's case, all the machines are configured identically to meet Pratt's particular chucking needs and demanding quality requirements. The partnership continued long after machine development and installation, as United Grinding keeps a full time service technician at the Pratt & Whitney facility to maintain 95% uptime.
Many aerospace components are coated with Tungsten Carbide Cobalt or other blends, often using the High Velocity Oxygen Fuel (HVOF) technique. These coated surfaces must be ground with special super abrasive technologies, and Studer has risen to the Challenge. Studer has also addressed a variety of other cylindrical components made with titanium alloys. In the last few years, Studer has satisfied the growing need to grind the highly precise spool valves required in sensitive flight controls.
Both EWAG and Walter have responded to the growing need for PCD cutting tools with machine innovations designed to increase both productivity and geometric flexibility. For example, EWAG offers in-process wheel regeneration that boosts the ability to grind PCD tools up to 30% for both inserts and "round" tools.
Walter has introduced software that enables erosion and grinding of all the high-tech solid drill geometries. These machines are being purchased by both aerospace firms themselves and by the specialized tool manufacturers who support them.
Get curated news on YOUR industry.
Enter your email to receive our newsletters.
Explore the January 2007 Issue
Check out more from this issue and find your next story to read.
Latest from Aerospace Manufacturing and Design
- Pemamak's PEMA Vision 3D software
- Aerospace Industry Outlook - Spring 2025, presented by Richard Aboulafia
- Panama’s National Air and Naval Service selects Embraer Super Tucano
- Model 5770 Linear Abraser
- #42 Lunch + Learn Podcast - Quell Corp
- RECARO Aircraft Seating showcases advanced comfort solutions at AIX 2025
- Mitutoyo America’s MiSTAR 575 Shop Floor CNC CMM
- Korean Air finalizes Boeing widebody order