
Developments in nanotechnology have resulted in improved film and coating solutions for protecting aircraft interiors. Designed to be durable, lightweight, and easy to clean, film products can resist flames, chemicals, moisture, or scuffs. Therefore, film products should be an essential element in plans to extend aircraft interior life and improve overall functionality.
Films, laminates, coatings
Films and similar laminates and coatings are pliable products made from a layer or layers of coated fluoropolymers, polyesters, or foils. Installed on glass, metal, and plastic surfaces inside an aircraft, aerospace films are often designed for internal insulation structures such as window interiors, lavatories, galleys, and bulkhead partitions as well as surfaces requiring a moisture barrier. Each aerospace film, laminate, or coating is developed in collaboration with original equipment manufacturers (OEM) to meet the needs of the aircraft and stringent industry regulations.
Applications, benefits
Windows – The airline industry, along with the Federal Aviation Administration (FAA) and the International Civil Aviation Organization (ICAO) set industry standards to ensure passenger safety, including the vertical burn test on windows to ensure that films applied to interior surfaces are heat- and flame-retardant.
Reputable film manufacturers work directly with independent labs to design products that pass the tests and ensure passenger safety.
Interior window films add a layer of comfort and safety for passengers. Afternoon and morning flights are often exposed to the blinding sun from takeoff to landing, yet completely closing the hard-cover blind is not an ideal solution.

Galleys – Polymer films are flexible and can be customized for each aircraft’s needs, including the galley and flight attendants’ jump seat area. Film manufacturers determine the ideal material, thickness, width, and end-product properties. These properties can include anything from anti-bacterial to
Lavatories – Correctly applied film provides added durability and protection, so surfaces become tougher, and the need for replacement parts becomes less frequent. Adding a layer of film can make the cleaning process faster and easier. Films provide a clear surface that takes the beating for the plastic underneath. Expedited cleaning allows faster flight boarding and

Certain polymer films also have antimicrobial properties. Since lavatories are highly public areas of the aircraft, the filmed surface can offer enhanced protection. Antimicrobial films provide a clean, durable surface that is protected to an enhanced degree.
Overhead Bins – Aircraft carry thousands of passengers and their baggage every day, and certain areas of the plane take a beating, namely the overhead bins. Wheels, zippers, and hard exteriors of suitcases constantly scrape overhead storage areas. Films with self-healing properties, widely used in the automotive industry, provide protection to high traffic areas, minimizing scrapes and dings, and extending the
Summary
Films, laminates, and coatings offer solutions for all aircraft – commercial airlines, military, helicopters, private jets, and spacecraft. Although virtually invisible to passengers, the benefits are real, improving air travel experience and protecting aircraft interiors from costly maintenance and repairs.
Madico Inc.
www.madico.com
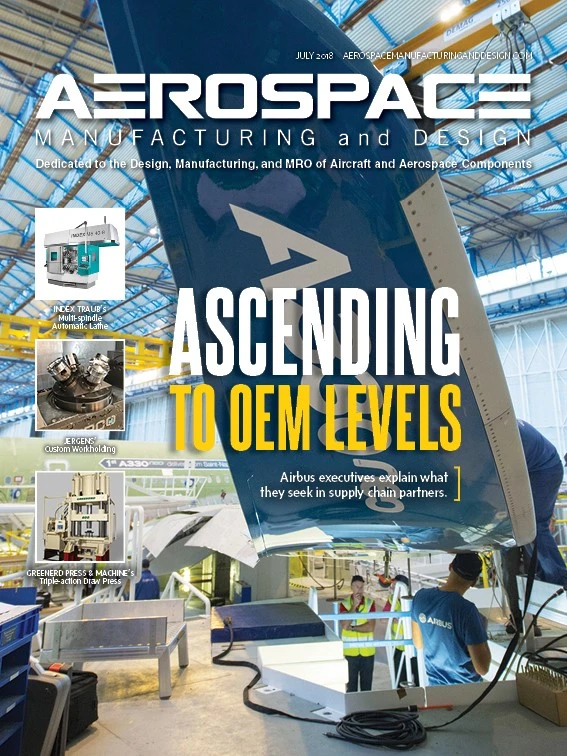
Explore the July 2018 Issue
Check out more from this issue and find your next story to read.
Latest from Aerospace Manufacturing and Design
- March Manufacturing Lunch + Learn with Quell Corp.
- March Manufacturing Lunch + Learn with SMW Autoblok
- SwRI addresses critical aging aircraft issue
- Walter adds tools to its PCD milling cutter range
- Archer Aviation, Palantir partner on next-gen aviation
- Fairlane Products’ TG GripSerts and accessories for low-profile clamping
- Boeing to build US Air Force’s sixth-generation fighter jet
- Sandvik Coromant introduces CoroMill Plura barrel