
Designing aerospace electronics requires engineers and designers to operate within limitations on available components, material types, equipment capabilities, board fabrication, and printed circuit board (PCB) assembly methods. Aggressive deployment and production cycles are forcing avionics engineers developing PCBs for critical systems to rapidly iterate designs.
That pressure on the design and development of aerospace systems, electronics, and the PCBs embedded in them is a major catalyst for strict regulations. Failure to adhere to these rules may result in aerospace products prematurely failing or unable to get off the ground at all. Navigating through regulatory requirements can be difficult. Fortunately, there is a set of design guidelines that will help aerospace designers and engineers create safer, more reliable PCBs and help to more efficiently and correctly employ design for manufacturability (DFM) methods for product development.
PCB design guidelines
Aerospace PCBs must operate in harsh environments without the ability to perform maintenance and repairs, requiring a greater emphasis on the manufacturing process.
Several design guidelines and best-practices define the most important considerations for board fabrication, component selection and acquisition, and PCB assembly:
- Choose high-quality materials because boards must meet applicable rigid, rigid-flex, or flex standards and thermal and electrical requirements for reliable operation
- Ensure boards have adequate spacings, clearances, and drill holes
- Choose a contract manufacturer (CM) with DFM guidelines in place to check for these specifications
Board component selection and acquisition also are important considerations when developing PCBs. Counterfeit and low-quality components abound and are among the most serious threats to safe and reliable deployment and operation of aerospace systems. Choose a CM that only sources materials from companies that adhere to regulatory standards and testing, have traceable supply chains, and meet required performance criteria. Inadvertent use of counterfeit components could result in increased regulatory scrutiny of a company’s supply chain, or even worse, may result in being blocked from supplying the industry.

Maintain quality control
Quality control is essential to aerospace PCB assembly – component and board durability contribute to the success of aerospace electronics in flight. To supply systems, electronics, and PCBs to the aerospace industry, companies must have a well-defined and documented quality management system (QMS) in place. The ability to meet the QMS standard depends on in-house quality management and the quality control instituted by CM partners.
Quality control also includes the design – the accuracy of component placement during PCB assembly is directly correlated to the accuracy of the PCB layout. Engineers and designers should follow board layout tips in line with their CM’s capabilities. However, CMs typically are not privy to factors such as circuit operation and will most likely be unable to identify errors such as incorrect component locations that can severely affect a board’s functionality. Footprints and silkscreens that accurately reference identifiers, Pin 1, and polarity indicators are necessary to ensure that a CM can properly align the selected components. Regulations also govern where logos and other markings may be placed.
Standards, regulations
Engineers and designers should research and familiarize themselves with the applicable standards and regulations for supplying parts and systems to aerospace industry organizations. The manufacturing process is a major component of key aerospace industry standards, including the AS9100D QMS standard and ISO 9100, the universally recognized International Organization of Standardization (ISO) baseline for QMS from which several other standards are derived. Developed and regulated by the Society of Automotive Engineers (SAE), AS9100D defines the QMS requirements for suppliers to the aerospace industry. It covers in-house and outsourced manufacturing processes and management responsibilities, emphasizing customer satisfaction.
Other aerospace-specific industry standards applicable to PCB development include AS5553A, which puts forth requirements for every organization in the supply chain that procures or integrates components that will be used in aerospace platforms, and AS478N, which specifies the type and placement of markings for aerospace components.
To be considered a preferred developer of aerospace products, it is crucial to have a collaborative relationship with an aerospace CM that also supports, understands, and is compliant with these standards.

Conclusion
By employing these design guidelines, engineers and designers can avoid the most common mistakes that could delay or ground their aerospace PCB design. Because aerospace PCB design and development are heavily regulated and require suppliers to ensure their CM is qualified, it is imperative for engineers to choose a partner that will work alongside them to navigate industry regulations, source materials from reputable companies, and assist in providing critical feedback that will ultimately help them improve their designs.
Tempo Automation
http://www.tempoautomation.com
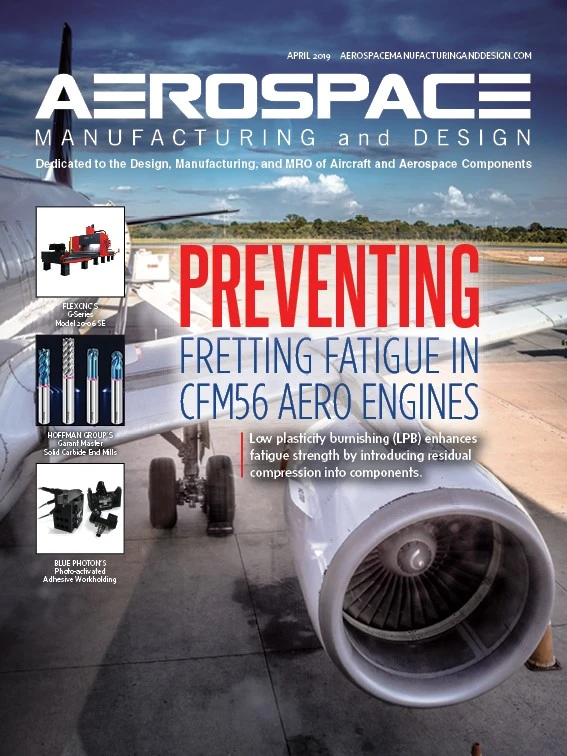
Explore the April 2019 Issue
Check out more from this issue and find your next story to read.
Latest from Aerospace Manufacturing and Design
- April Manufacturing Lunch + Learn with Iscar
- April Manufacturing Lunch + Learn with Insaco
- Archer unveils vision for New York air taxi network
- Siemens launches its machine tool digitalization software portfolio MACHINUM in the US
- #58 - Manufacturing Matters - 2024 Metrology's Latest Advancements with Starrett
- Strategies to improve milling and turning for medical components
- Being proactive about your business despite uncertainty
- Optimizing production of high-precision components through collaboration