
Editor’s note: Part 1 in the June 2017 issue (https://goo.gl/NpNXhD) examined industrial air quality in the aerospace industry. Part 2 offers solutions to air quality challenges.
Aerospace manufacturers have many options to maintain air quality. The best one depends on the specific processes and facility. When evaluating mitigation strategies, manufacturers should first look at the current state and the specific risks associated with their processes. Some questions to ask include:
- What processes are being used (for example: welding, blasting, machining, grinding), and what is the volume of particulates produced?
- What is the size of the components being worked with and can they be contained under a hood or on a bench?
- Are the processes manual or robotic? When, where, and how are humans exposed to particulates?
- What is the chemical makeup of the particulates, and what are permissible exposure limits (PELs) for these compounds?
- Are particulates combustible?
- Where are particulates generated, and where do they end up in the facility?
- What are the airflow patterns in your facility, and what influences them (heating/air conditioner or ventilation systems, facility layout, etc.)?
- What mitigation systems are in place already, and how are they working?
- How much flexibility is needed to reconfigure manufacturing lines?
Options for mitigation

Indoor air quality (IAQ) mitigation options fall into a few broad categories that can be understood as choices in a two-dimensional matrix:
Filtration vs. exhaust: Exhaust and makeup air systems push dirty air out of the facility and pull in clean(er) air. If particulate volumes are low and heating and cooling costs are not a consideration, this option is inexpensive and easy to implement. However, if makeup air must be heated or cooled to indoor temperatures, exhaust systems can quickly drain the energy budget. Depending on the type and volume of particulates, they may also put the facility out of environmental compliance.
Filtration systems pull dirty air into a dust collector where particulates are filtered out before clean air is returned to the facility. Filtration is usually the better option for facilities with high volumes of particulates and temperature-controlled indoor environments.
Source capture vs. ambient: Source capture systems collect particulates close to the source as they are generated, before they escape into the ambient air in the facility. Ambient systems turn over air for the entire facility. In general, source capture will be less expensive; the less air that needs to move, the lower the equipment and operating costs will be. For some applications, such as resistance welding of very large components, ambient may be the only option. Ambient systems can also be used along with source capture solutions for secondary air quality control.
Start with source capture
Source capture should be used as the first line of defense whenever possible, however the best source capture system depends on the application.
Robotic welding: For robotic welding of small- to medium-size components, hoods keep fumes contained and out of the facility at large. Hoods are paired with a dust collector to extract and filter dirty air. Large centralized collectors are highly efficient and can be ducted to several robotic weld cells. If more flexibility is needed, smaller units such as the RoboVent Spire, can be directly ducted to each robotic cell and moved along with the cell as lines are reconfigured. To reduce air movement requirements and costs, make sure hoods are properly sized for the application. If the application cannot be hooded and uses metal-inert-gas (MIG) welding, a fume extractor tip can sometimes be added directly to the weld-torch head. These systems can capture up to 70% of fumes as they are generated but must be customized to the individual robot and application for maximum efficiency.
Manual welding (small components): Manual welding requires an option that keeps weld smoke out of the welder’s breathing zone. Hoods should not be used for manual welding unless they are paired with personal protective equipment such as a powered air purifying respirator (PAPR) system. Small components that can be placed on a bench for welding have several options. Backdraft or side-draft tables pull welding fumes away from the welder’s breathing zone using an intake plenum. Fume arms are another option. They work well for small parts that do not need to be repositioned. When working on larger parts, the welder must remember to reposition the arm as the welding torch is moved.

Manual welding (large components): For large components, the best option is usually a fume gun. Modern fume guns such as the RoboVent Extractor, collect 90% or more of fumes at the source, keeping them out of the breathing zone and eliminating the need for PAPR equipment. Fume guns can be used for manual MIG welding.
Machining: Machining lubricants create dangerous oil mists when heated, requiring specialized collection equipment and filters. Regular filters quickly become saturated and ineffective when oil mists are mixed with dry particulate. Packed bed filters, also called coalescing filters, are the most effective filters for most oil mists.
Cutting, grinding: While weld fumes can be captured as they rise, heavier particulates from cutting and grinding will quickly settle downward. Downdraft tables are effective for many cutting and grinding applications.
Blasting: Blasting applications, such as those used to clean and refurbish engine parts, produce large volumes of heavy, toxic dusts. When refurbishing jet engines, small components can usually be contained in a booth that separates workers from the blasting material. Larger components, such as the engine frame, should be blasted in a contained area to keep particulates from migrating to other parts of the facility. Workers will need to have PAPR equipment when working in the blasting room or booth, which should be ducted to a powerful dust collector to pull excess particulates out of the air.
Ambient options
Ambient filtration can be used as a stand-alone system when working with larger components that cannot be hooded or as part of a hybrid system that also includes source capture. There are three main options to look for in ambient filtration systems:
- Ducted push-pull systems rely on a system of ducts near the ceiling, creating air currents in the building that continually pull contaminated air away from personnel
- Ductless systems, such as RoboVent’s Vortex, rely on stand-alone dust collectors that sit on the factory floor. Each dust collector creates its own circular local airflow pattern, pulling dirty air in and pushing clean air out
- Ductless ceiling mounted systems, such as the RoboVent Vista360, combine the advantages of a ductless system with the floor space savings of a traditional push-pull system. They may also work better in facilities where overhead cranes are used
Design for cost control

A well-designed air quality system can protect companies from legal liability and government fines and sanctions while keeping employees happy and healthy, but it’s not always easy to determine which approach will provide the best value for the money. A qualified air quality engineer can help aerospace manufacturers find the best solution for their specific applications and challenges.
Sometimes, engineers use computer modeling to design the solution, helping companies avoid over- or under-engineering an air quality solution and finding the best solution for cost and effectiveness. RoboVent’s VentMapping process optimizes placement of source and ambient capture equipment, making sure the final solution will meet the company’s air quality goals.
Aerospace manufacturing has a lot of challenges, but air quality shouldn’t be one of them. With thoughtful planning and a strategic approach, aerospace manufacturers can find a solution that keeps fumes under control without breaking the bank.
RoboVent
Get curated news on YOUR industry.
Enter your email to receive our newsletters.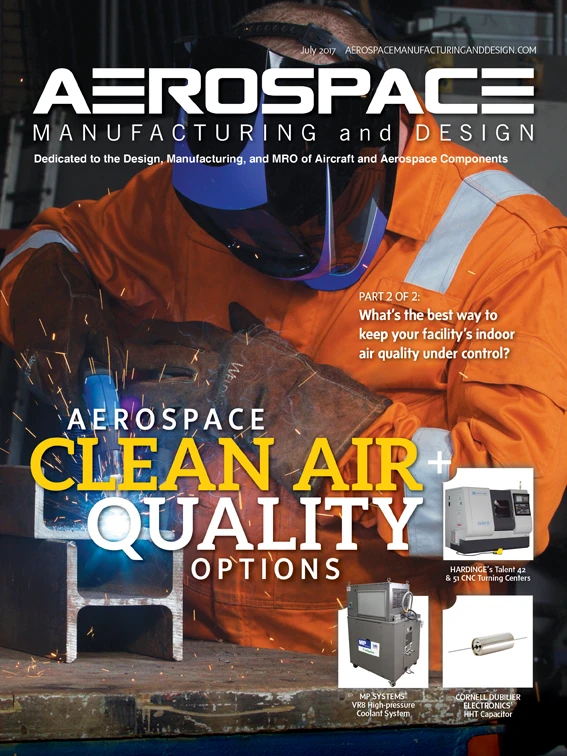
Explore the July 2017 Issue
Check out more from this issue and find your next story to read.
Latest from Aerospace Manufacturing and Design
- AIX showcases the future of air travel
- Sunnen Products' PGE-6000 gage
- #41 Lunch + Learn Podcast - SMW Autoblok
- Revolutionizing aircraft design without sacrificing sustainability
- GE Aerospace awarded subcontract for FLRAA next phase
- KYOCERA Precision Tools publishes 2025-2026 Indexable Cutting Tools Catalog
- BOC Aviation orders 120 Airbus, Boeing jetliners
- Mazak’s INTEGREX j-Series NEO