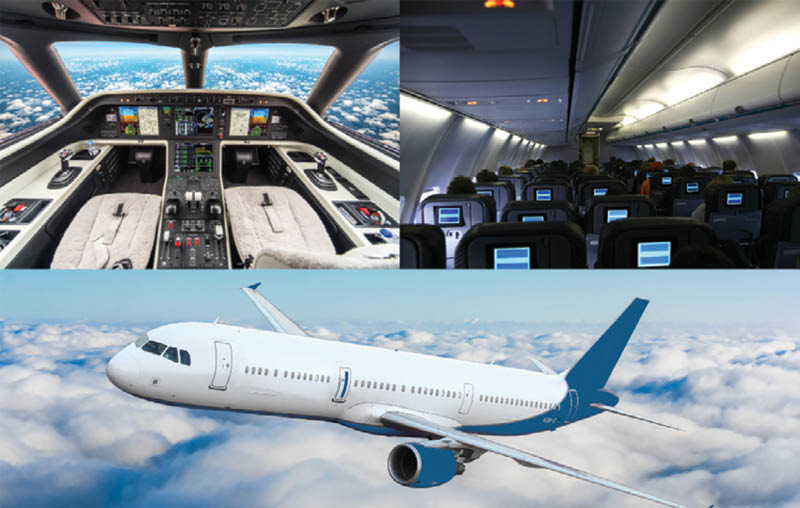
Motion control design in aerospace systems must strive for precise, power-dense motion while withstanding extreme conditions. Typical specifications require motors in aerospace systems to withstand extreme temperature ranges, operate under severe shock and vibration conditions, and fit in constrained space while maintaining high performance levels.
Three motor technologies are frequently used for motion requirements in aerospace applications: brush DC coreless, brushless DC (BLDC), and stepper. Engineers often choose brush DC coreless and BLDC motors for their higher efficiency and lower weight – with BLDC motors being available in cylindrical and flat forms – along with using slotted and slotless winding technologies. Stepper motors are also ideal for precision but may be chosen for price-to-performance value.
Challenges
These three technologies are adaptable to challenging performance requirements of typical aerospace applications, but they’re also resilient to extreme environmental conditions. Temperature requirements are a key example, as they can range from -55°C (-67°F) to 200°C (392°F). This means all motion control components must be specially designed to survive in extremes while sustaining high-performance levels throughout the entire operational range. Advancements in materials, particularly metals used in motor housings, special bearing lubricants, specialty coatings for electronics, and plastics for insulating the coils allow reliable operation of these mini motors.
High shock and vibration environments present a second common challenge. Special design considerations allow miniature motors to perform in extreme environments, as even small movements of the motor coils can lead to motor damage. Motor design should guarantee secure positioning of critical internal components such as the rotor, shaft, and bearings, as well as connected elements such as gearboxes and encoders when exposed to severe shock and vibration conditions.
A third possibility for motor failure is exposure to potentially hazardous materials. Motor design engineers seek to incorporate advanced materials coupled with specialized sealing designs within the motor. An optimal design ensures the motor can operate at peak efficiencies in these extreme environments and, more importantly, the motor operates safely and reliably.
Critical functionality
Aerospace applications can be separated into three categories: commercial aerospace; military aerospace and defense; and spacecraft and rockets. The common element is the need for power-dense, lightweight motor designs providing a form of actuation.
Various types of valves and actuators are used on aircraft vehicles to perform critical functions, including regulating the flow of fuel to the engine and controlling the airflow into the aircraft cabin. Due to their physical location in the aircraft, these devices are typically exposed to extreme environments and demand maximum power density and dynamic response from the motion system. Typical design considerations include:
- Modifications to the magnet material to ensure magnet strength doesn’t degrade as temperatures elevate
- Lamination material selection to ensure motors can withstand extreme temperature ranges
- Properly selecting lead wires that connect motors to system electronics ensures they remain pliable in extreme cold and don’t melt in extreme heat
Design considerations
To ensure high-performance operation throughout the aircraft’s life cycle, one must consider each of these motor design modifications capable of withstanding wide temperature extremes. Many legacy and current generation valve designs use either stepper motors that finely regulate position or brush DC motors that are an ideal fit for on/off valves. However, next-generation designs are gradually transitioning to brushless DC motors for smart actuation applications due to the BLDC motor’s precise positioning capabilities that can provide data on several operations, monitor any abnormal behavior, and supply maintenance information – improving overall reliability and equipment performance.
Electromechanical control of window shades and seat actuation drives expanding innovations for private and commercial aircraft. This aims to provide passengers with ease of use and grants airline personnel greater control. These systems allow the passenger to conveniently raise or lower the shade or seating surface at the touch of a button; they also allow flight attendants to control the cabin ambient light and assume proper seat position during takeoff and landing. Due to their high-power density, low noise, and low-temperature rise, DC coreless motors are primarily used in these cases. The ability to operate motors without any control electronics is a clear cost advantage, while the high efficiency and low weight of the motor reduces power and fuel consumption.
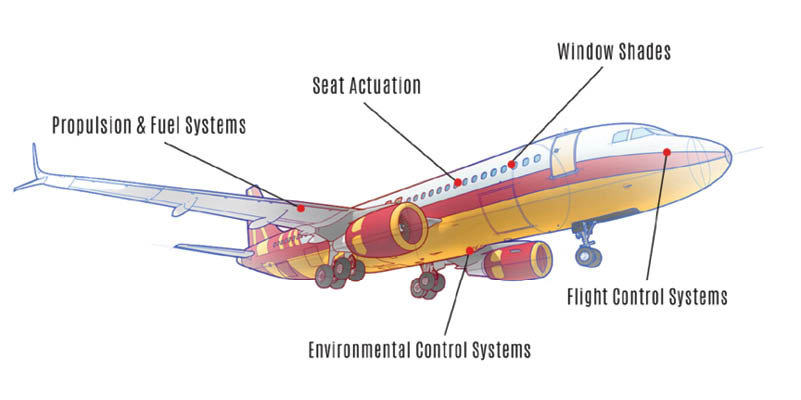
For simple motion systems, brush DC motors are the most cost-effective solutions to meet application requirements such as performance, size, and extended life. For more complex requirements, a fully customized BLDC motor is likely the best solution.
Solutions
Precision motors manufacturers for the aerospace market must provide custom motor designs optimized for each specific application. Motor design engineers must thoroughly understand how to optimize specific design criteria according to the application requirements and can modify existing designs to meet environmental conditions such as space, weight, and power (SWaP). Custom or modified commercial-off-the-shelf (COTS) motors are ideal for aerospace applications, as they provide high power density in small, lightweight designs. Manufacturers offering various motor technologies can analyze the specific demands of the requirement across technologies and offer multiple motion control solutions to the customer.
Aerospace systems continue to expand with advancements in technology. Refining motor designs with evolutions in material to provide optimized motion control solutions will continue to be a challenge when addressing the future demands of this ever-evolving market.
PortescapPRODUCTS
9D LADAR on an AGV
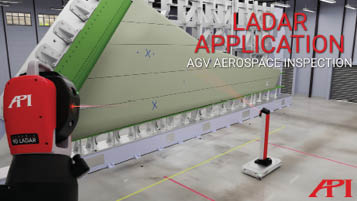
Automated Precision Inc. (API) offers a transformative approach to aerospace manufacturing inspections with its Dynamic 9D LADAR mounted on an autonomous guided vehicle (AGV).
When integrated with an AGV, the 9D LADAR system offers flexibility and coverage across the manufacturing floor, navigating autonomously and adjusting its measurement height as needed. With a 25m range and a scanning speed of 0.2 seconds/cm², this non-contact system precisely captures dimensional and surface geometry data.
Automated Precision Inc. (API)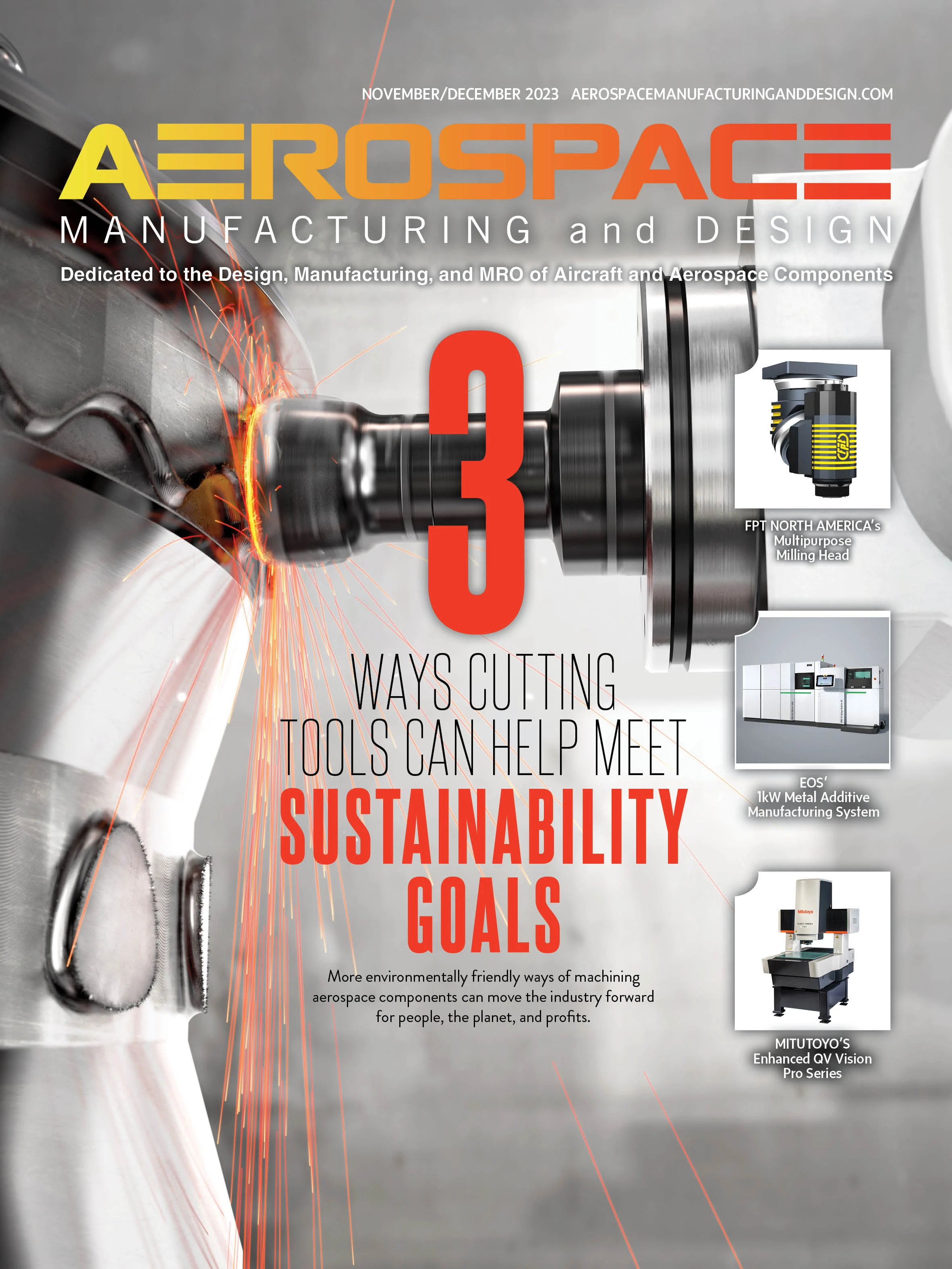
Explore the November December 2023 Issue
Check out more from this issue and find your next story to read.
Latest from Aerospace Manufacturing and Design
- Archer unveils vision for New York air taxi network
- Siemens launches its machine tool digitalization software portfolio MACHINUM in the US
- #58 - Manufacturing Matters - 2024 Metrology's Latest Advancements with Starrett
- Strategies to improve milling and turning for medical components
- Being proactive about your business despite uncertainty
- Optimizing production of high-precision components through collaboration
- An inside look at the defense maritime industrial base
- Safran inaugurates advanced manufacturing and engineering hub