
For K&G Manufacturing, one motto remains front and center throughout the shop: Our next order depends on the quality of our last shipment.
The shop prides itself on its ability to meet the needs of the most demanding customers in their industries, thanks to high-speed machine spindles, cutting tools, and toolholders.
The company primarily focuses on aerospace, marine, and defense, with other customers from medical, heavy equipment, high-tech, and recreation industries. Customer loyalty is maintained by minimizing defects and maintaining high on-time delivery rates.
Tool Crib Manager Joe Pleskonko oversees K&G’s $500,000 tool inventory that supports its 41,000ft2 manufacturing facility’s diverse range of jobs performed on high-performance machine tools. The company also designs and produces tooling and fixturing in-house.
Pleskonko, like all K&G team members, takes the company’s motto seriously, working hard to find ways to speed up operations and optimize production.
“We run high-performance milling chucks, and we like to get jobs done as quickly as possible, so we push our tools hard,” Pleskonko says.

The various hydraulic holders used, however, couldn’t keep up with the 20,000rpm and faster spindles in the company’s machine tools. Seeking a solution, Pleskonko worked with K&G Manufacturing supplier Productivity Inc.
“We work with our customers to identify solutions and prove them out on their parts and machines,” says Patrick Miller, outside sales specialist at Productivity. “Seeing the solution perform gives them the confidence they need to make a decision. At K&G, they do a lot of high-end, high-rpm work, so precision is paramount.”
Miller and Pleskonko considered numerous solutions but decided to see how the powRgrip System from Rego-Fix Tool Corp. performed. Rather than heat or hydraulic-based solutions, powRgrip relies on the mechanical interference between holder and collet to generate up to 9 tons of clamping force to grip tools and keep run-out less than 0.0001" for more than 20,000 cycles.
To test the powRgrip system, K&G selected a job that ran five days a week for 50 weeks. With the previous toolholding, K&G achieved about 15,000 to 20,000 cutting inches of tool life, requiring a tool change about every three days for 83 tools per year. With powRgrip, tool life more than tripled, achieving 60,000 to 70,000 cutting inches of tool life and 21 tools per year.
“That translates to 62 tools saved a year, and at $60 per tool, that’s an annual savings of $3,720,” Pleskonko says. “And that’s just one tool. Plus, operators don’t have to change tools as often, which prevents changeovers that impact precision and/or add to setup time.”

The heat-free process is even faster with K&G’s PGU 9500 automatic clamping unit, which enables safe, secure clamping and unclamping with the touch of a button.
However, benefits of the powRgrip system extended beyond tool life or setup time. With the shop’s previous toolholder, the tool would begin producing heavy burrs after 15,000" of cutting. The powRgrip, on the other hand, delivers superior clamping force, rigidity, and balance, preventing burr formation and producing consistent surface finishes. Reducing deburring time frees employees for other benchwork.
Ryan Morris, manufacturing engineer at K&G, appreciates the powRgrip system’s runout prevention and looks forward to finding new applications for the toolholders.
“I’d like to use it on a lot of roughing tools, where I know I’ll achieve significant gains,” Morris says. “In seven months we have not had any tools pull out or move around on us, like we do with traditional systems.”
Pleskonko was so pleased with the results of the powRgrip system that he’s considering other solutions from Rego-Fix. “For hogging out parts – big, big castings – we’re going to be pushing our tools harder and faster to just remove material. The faster we cut the better. So we’ll definitely be looking into other solutions like secuRgrip.”
Typical workpieces weigh 5 lb to 75 lb and include everything from relatively small components to 28" long engine blocks. Job lot sizes can vary from 50 to 500 a month, and the shop primarily works with cast and billet aluminum, though it also machines some steels and cast irons.
K&G’s aerospace work generally involves fuel housings and fuel pumps for larger aircraft, necessitating high-volume production of high-precision parts, while its medical jobs are often small components with functional surfaces. Its marine industry side of the business handles virtually all the machining and assembly of whole inboard and outboard motors.
To keep up with this wide range of jobs, Pleskonko, Miller, and the rest of the team constantly re-evaluate equipment. So far, the Rego-Fix powRgrip toolholding system has passed every test.
“We always keep lists of pros and cons of the equipment and tooling we use,” Pleskonko says, “and I still haven’t put anything in the con column for powRgrip. It just keeps knocking everything else out of the water.”
Get curated news on YOUR industry.
Enter your email to receive our newsletters.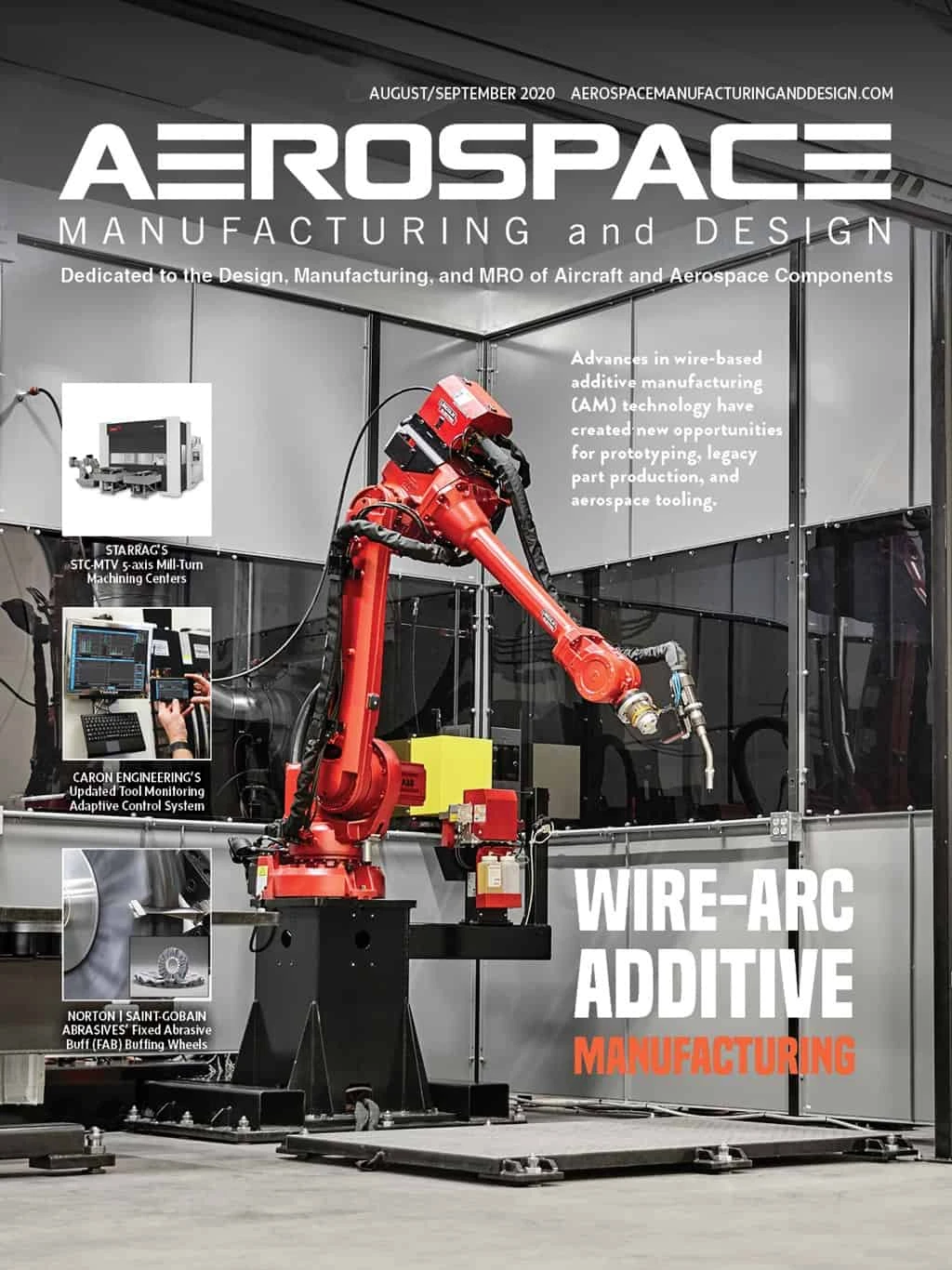
Explore the August September 2020 Issue
Check out more from this issue and find your next story to read.
Latest from Aerospace Manufacturing and Design
- Piasecki acquires Kaman's KARGO UAV program
- PI Americas’ long-travel XY piezo nanopositioners-scanners
- AAMI project call submission deadline extended to May 12
- Jergens launches cast iron tooling column additions
- Airbus to acquire assets relating to its aircraft production from Spirit AeroSystems
- FANUC America's Cobot and Go web tool
- Chicago Innovation Days 2025: Shaping the future of manufacturing
- High-density DC/DC converters for mission-critical applications