For safety and reliability, it’s important to understand how a rotorcraft will perform during operation. Engineers need to identify failure risks early to adjust the design or configuration with minimal cost and resources. Similarly, engineers also look for ways to understand how variable conditions impact the performance of aircraft systems already in operation.

Currently, most life-prediction methods are empirically based and deterministic, and only consider the final stages of crack propagation in drive system components (gears, bearings, and spline shafts). This approach limits actions that can be taken to prevent further damage to the system and increases maintenance activities. Empirically based methods cannot readily account for the drive system components’ manufacturing process, lubrication effects, materials, and service conditions, which are essential to the fatigue life prediction process.
Decoding the material genome
“Cracks initiate deep within the microstructure of the materials long before damage can be seen at the surface,” says Ward Thomas, president and CEO of Sentient Science. “So, we set out to decode the material genome in a similar way that molecular biologists decoded the human genome.”
Specialists at Sentient Science, headquartered in Buffalo, New York, developed a materials science-based prognostic technology that builds multiphysics-dynamic models of the critical components of the drivetrain. The software, DigitalClone, simulates how the manufacturing process, contact pattern, lubrication effects, stresses, microstructure, and material variability impact the lifetime performance of the rotorcraft. DigitalClone quickly analyzes thousands of test data points to predict the projected life of the drivetrain during operation.
Advanced drive system development programs funded by the U.S. Department of Defense on the Black Hawk and Apache platforms included Sentient involvement to compare physical test data with DigitalClone analysis to assess any unidentified risks.
“The U.S. Government was our first investor, and we’ve continued that relationship during the last 15 years. Our DigitalClone prognostic technology was developed to ensure safe, reliable, and efficient operation and maintenance of rotorcraft drive systems for the military,” Thomas says. “We’re taking that application and beginning to sell it to commercial vertical lift operators who want to use it to forecast maintenance and spare part replacements to reduce costs and extend their maintenance-free operating periods (MFOP).”
Thomas notes that engineers currently use the software to accelerate innovations at reduced cost and time by identifying operational failure risks early in the design process.
Toward zero maintenance
Sentient is developing a solution that integrates DigitalClone’s prognostic technology with a platform’s health and usage monitoring system (HUMS) data. Enhancing HUMS capabilities will facilitate a transition from reactive maintenance practices to extended MFOP.

“The goal is to integrate prognostic model fatigue life results with existing on- and off-board processors and HUMS for improved safe operation – and to reduce operations and maintenance costs,” Thomas says. “Extended MFOP will be supported by increasingly automated inspections, monitoring, and management of remaining useful life.”
Aviation science and technology strategic plan initiatives call for the transition from condition based maintenance (CBM) to enhanced CBM with extended MFOP and eventually to zero maintenance. DigitalClone Live capabilities will assist by providing life-extension actions at the pilot, depot, and enterprise levels.
For instance, during rotorcraft operation, prognostics provide system health state warning with critical component description and remaining useful life. The recommended action for a pilot could be continue a mission if it fits within the mean time to observable damage. If not, then it would be told to return to base.
At the depot, maintenance crews can confirm predictions with system feedback and repair, replace, or inspect components predicted to show signs of wear or fatigue.
Applications for prognostics for the enterprise level include:
- Inventory management for critical spare parts
- Changes in maintenance programs to extend life, save costs
- Analyze supplier offerings, make changes based on life impact
- Asset-specific health state simulations based on historic usage
Prognostic modeling’s uses include safe design, operation, and maintenance of rotorcraft – and can reduce costs through better logistics planning – moving from a reactive maintenance strategy to preventative maintenance practices.
Sentient Science
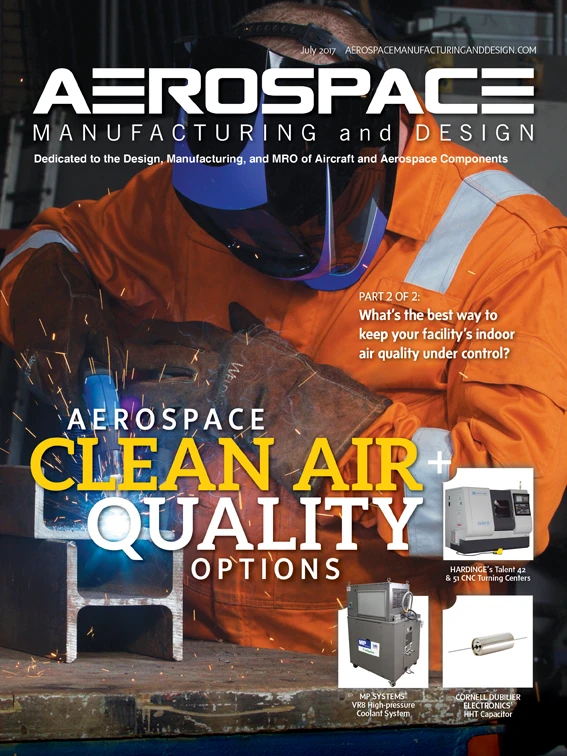
Explore the July 2017 Issue
Check out more from this issue and find your next story to read.
Latest from Aerospace Manufacturing and Design
- GE Aerospace awarded subcontract for FLRAA next phase
- KYOCERA Precision Tools publishes 2025-2026 Indexable Cutting Tools Catalog
- BOC Aviation orders 120 Airbus, Boeing jetliners
- Mazak’s INTEGREX j-Series NEO
- Embraer tests wing for new technologies demonstrator
- Mitutoyo America’s SJ-220 portable surface roughness tester
- #55 - Manufacturing Matters - A Primer on Defense Contract Manufacturing
- Registration is open for April’s Manufacturing Lunch + Learn!