
Aerospace manufacturers and engineers have been working with hydrodynamic seals for 50 years with only mixed success. The sealing technology holds great promise for aviation engineers intent on increasing efficiency and uptime, but applications to date have yet to deliver on the potential of the technology.
Thanks in part to a series of engineered hydrodynamic grooves visible on their face, these seals ride on a thin air film instead of directly contacting the rotor, and rely on that air pressure to separate gases or fluids on either side of the seal. They only maintain contact with the rotor when not in service, but achieve liftoff at low speeds and are therefore non-contact when in service. This reduces wear and costly maintenance while increasing the speed at which the rotor may operate.
Hydrodynamic seals are altitude-sensitive, causing problems including a lack of full liftoff from the rotor, erratic performance, or outright failure. By leveraging experience in dynamic sealing of a new hydrodynamic seal design in 2015, Technetics Group has solved problems plaguing this technology, cutting air leakage of existing hydrodynamic seals, from 0.00035 lb/min to as little as 0.00016 lb/min, while achieving liftoff more than twice as fast.
This means hydrodynamic seals could become the sealing solution of choice for a broad spectrum of aviation applications ranging from propulsion engines to gearboxes to auxiliary power units (APU’s), delivering 10x the usable life along with associated substantial reductions in maintenance and downtime.
An old problem
Ever since the concept was pioneered in the 1960s, hydrodynamics have been of intense interest to the aerospace industry, but they have yet to edge out carbon-faced contact seals and other contact sealing solutions that are reliable but constrain performance and require regular service due to friction and resulting high temperatures. As aircraft operators are under pressure to increase uptime and drive down costs, reducing scheduled maintenance by shifting toward hydrodynamic seals in multiple parts of the aircraft can be an attractive option.
A major Tier 1 aerospace vendor asked Technetics Group to provide hydrodynamic seals for the main shaft and gearbox of one of its APUs. Carbon-face seals have historically been used in this application but must be replaced every 2,000 hours to 5,000 hours of flight due to their contact with the rotor. Technetics’ hydrodynamic seal design is projected to deliver at least 20,000 hours of service.
“The process of replacing a seal on an APU can take days, and in many cases technicians have to remove the engine from the aircraft to do so,” Technetics Group Senior Market Manager Jason Riggs says. “The seal is typically buried near the bearings and replacement is a major undertaking.”
At the point when Technetics entered the program, the competing hydrodynamic seals had failed to achieve the customer’s performance targets during rig and engine tests. According to Riggs, this was not surprising given the difficulties aerospace engineers have historically encountered with hydrodynamic seals.
“Hydrodynamic seals have presented a number of design and manufacturing problems, including the challenges of performing on an aircraft at high altitude,” Riggs notes. “One root cause of these failures was the inaccurate design theory and tools used to optimize the hydrodynamic features in those conditions.”
As the engine spools up and the rotor spins, it creates the required pressurized air film between the seal and the rotor, causing the seal to lift off from the rotor like a tire separating from pavement during hydroplaning. Each hydrodynamic seal will have a liftoff speed – the speed at which the force of the air pressure exceeds the pressure from the spring or bellows that holds the seal to the opposing face when the system is not energized. Designing a seal that lifts off quickly, creating an effective seal more immediately as the engine starts up and remains functional at altitude, had proved elusive.
“One of our competitors has a seal that may not actually lift off completely,” Riggs says. “There is some pressurized film, but the normal operating state is somewhere in between lifting off and full contact. This can marginalize the benefits of a hydrodynamic design.”
Another competing technology keeps the separate seal faces apart by using magnets in the seal face. The system requires very specific lubricants, O-rings, and methods of installation, or catastrophic leakage and bearing failure can result.
Advanced modeling
Technetics Group partnered with an industry consultant to develop a code that could analyze and predict performance at high altitude, relying on modeling software from ADINA, a company founded by Massachusetts Institute of Technology (MIT) professor Klaus-Jürgen Bathe, an innovator in finite element analysis.
“It has a very powerful solver and better algorithms than other modeling tools,” Riggs says of ADINA. “This allowed us to predict the required coning of the seal more accurately than our competitors. We were able to account for distortion due to thermal expansion, mismatches between the carbon and the container for thermal gradients, and centrifugal loads as the parts spin and want to distort. Most tools make theoretical assumptions that are not accurate when you have high altitude with thin air and low absolute pressures. We were able to make more informed assumptions and design an optimal hydrodynamic groove.”
Because the groove is static while altitude naturally changes, Riggs says the team considered various altitudes and speeds in their model, but primarily designed around the highest altitude where the seal would need to perform.
Absolute precision required
Designing the hydrodynamic seal was only the first challenge. The team at Technetics quickly learned that traditional manufacturing equipment and processes were not precise enough to cut the hydrodynamic grooves at a tight enough tolerance for optimal performance.

The traditional method for cutting these hydrodynamic grooves is via erosion media etching.
“We found that we needed to create a proprietary process that can hold much tighter tolerances than what is available,” Riggs says. “It was a major undertaking, but we have designed a process that controls the position, shape, and depth of the hydrodynamic groove through more sophisticated means than we have seen in the market previously.”
Due to the tight project deadline and long lead times for some of the materials, engineering and purchasing had to run concurrently. The 13-week timeline required the company to build prototypes just beyond the raw material lead time.
In on-engine testing conducted by its customer, Technetics Group’s hydrodynamic seals were within a couple of percentage points of modeled performance in liftoff, temperature, and performance at altitude.
“Liftoff speed is a good indicator of performance and design margin, and we achieved liftoff at less than half the speed of the next best option,” Riggs says. “That is significantly better performance than existing hydrodynamic seal options, and our technology also delivers more tolerance for operating conditions. The results of this on-engine testing give us the confidence to deliver these seals for various applications with no design iterations.”
Testing highlighted the durability of the new versus legacy seal designs.
“The seal can handle more vibration and extreme conditions without making contact,” Riggs says. “We also did some endurance testing, and after running about 2,500 hours, and the seals looked brand new. Competing hydrodynamic technologies would show clear signs of wear due to either their higher liftoff speeds and lower film thickness at altitude or their lack of consistent liftoff and contact due to vibration or altitude.”
Wide-reaching implications
The technical innovations in these hydrodynamic seals enable aerospace engineers to more confidently specify in several applications.
“Hydrodynamic seals can now be used anywhere you have a rotating shaft and need to seal a gas to gas or oil-mist to gas,” Riggs says. “You can use them on the main shaft of propulsion engines and APUs as well as other applications such as turbo pumps for rocket motors running with cryogenic fluids, gearboxes, and air turbine starters.”
With a 5x to 10x longer life than existing options, the technology has implications for both commercial and military aviation.
“Our hydrodynamic seals allow our customers to design their assemblies for higher rotational speeds,” Riggs says. “And at higher speed, you get more efficiencies and power out of the same package whether it be an engine or gearbox assembly.”
Future potential
Time will tell how quickly hydrodynamic seals replace contact seals in aviation applications. Under pressure from fleet owner-customers intent on lowering lifecycle cost of aircraft, original equipment manufacturers (OEMs) may rapidly make the switch on new aircraft. According to Riggs, fleet owners may also look to the OEMs to retrofit existing components for hydrodynamic seals to drive down maintenance costs and increase useful service hours.
Technetics Group
About the author: Technetics Group Research and Development Engineer Aaron Glafenhein led development of Technetics’ new hydrodynamic seal. He can be reached at aerospace@technetics.com.
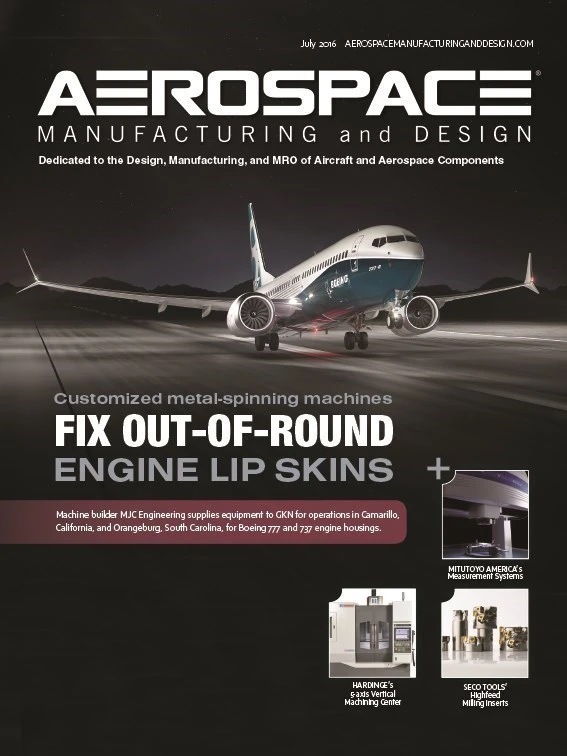
Explore the July 2016 Issue
Check out more from this issue and find your next story to read.
Latest from Aerospace Manufacturing and Design
- Heart Aerospace relocates to Los Angeles
- Fixtureworks introduces Stablelock Clamps
- Piasecki acquires Kaman's KARGO UAV program
- PI Americas’ long-travel XY piezo nanopositioners-scanners
- AAMI project call submission deadline extended to May 12
- Jergens launches cast iron tooling column additions
- Airbus to acquire assets relating to its aircraft production from Spirit AeroSystems
- FANUC America's Cobot and Go web tool