
Complex parts with multiple features to be machined demand high quality computer aided manufacturing (CAM) software to manage processes, but designers still develop simpler parts with manual processes.
Engineers at Umbra Cuscinetti S.p.A., however, decided that using CAM on all parts could optimize operations and ensure the company was using the best possible approaches for even the simplest products.
Since 1972, aerospace supplier Umbra Cuscinetti has designed and manufactured ball screws for aircraft. Umbra also manufactures electric spindles, milling heads, and electromechanical actuators for aerospace and industrial applications. The company’s growth has transformed its parent company in Foligno, Italy, into the multinational UmbraGroup, with four offices in Italy, Germany, and the United States, and a worldwide workforce of more than 1,000 employees. Most of the company’s employees are located at the Perugia factory in Italy and handle the design and manufacture of ball screws from 10mm to 10m long, mainly intended for aviation.

“We export more than 90% of what we produce here in Foligno, Italy to every airline in the world. Every airplane with more than 100 seats has at least one component inside it that has been made in our factory,” says Angelo Radicioni, production manager at Umbra Cuscinetti.
Nowadays, digital drawings are usually provided for production, but many tools and CNC programs for manufacturing simple components are still manually developed, with more complex parts being machined using CAD/CAM software.

“The goal we set for ourselves was to implement a CAM solution for even the easiest parts in order to provide us with the total cycle time to determine the overall efficiency of our processes,” explains Mauro Trasciatti, production supervisor at Umbra Cuscinetti.
Umbra implemented Esprit CAM software by DP Technology for improved CNC programming speed and increased productivity on the shop floor.

High performance CAM
To meet the demands of customers and members of Umbra’s internal design team, the company increasingly pushed for more advanced machine tools to reduce cycle time and improve productivity.
“We needed a machine tool solution that would allow flexibility and speed in standard operations,” says Gianluca Mercuri, turning & milling specialist at Umbra Cuscinetti. “Esprit CAM software provided us with everything we needed to run our advanced machine tools and gave us the ability to save customized milling and turning operations, both for the processes we use most as well as our non-standard processes.”

The field of electromechanical actuators is growing fast for the company so they continue to advance internal and external turning processes and multi-axis milling.
“One of the most complex operations that we accomplished with Esprit CAM was wrap pocketing using a simultaneous 4th axis,” Mercuri adds.
With Esprit CAM software, the company has optimized their CNC machining centers and benefited greatly from certified post-processors. This has allowed Umbra to access full functionality of their CNC machine tools, increase their productivity, and continue to make the high-quality parts their customers demand.

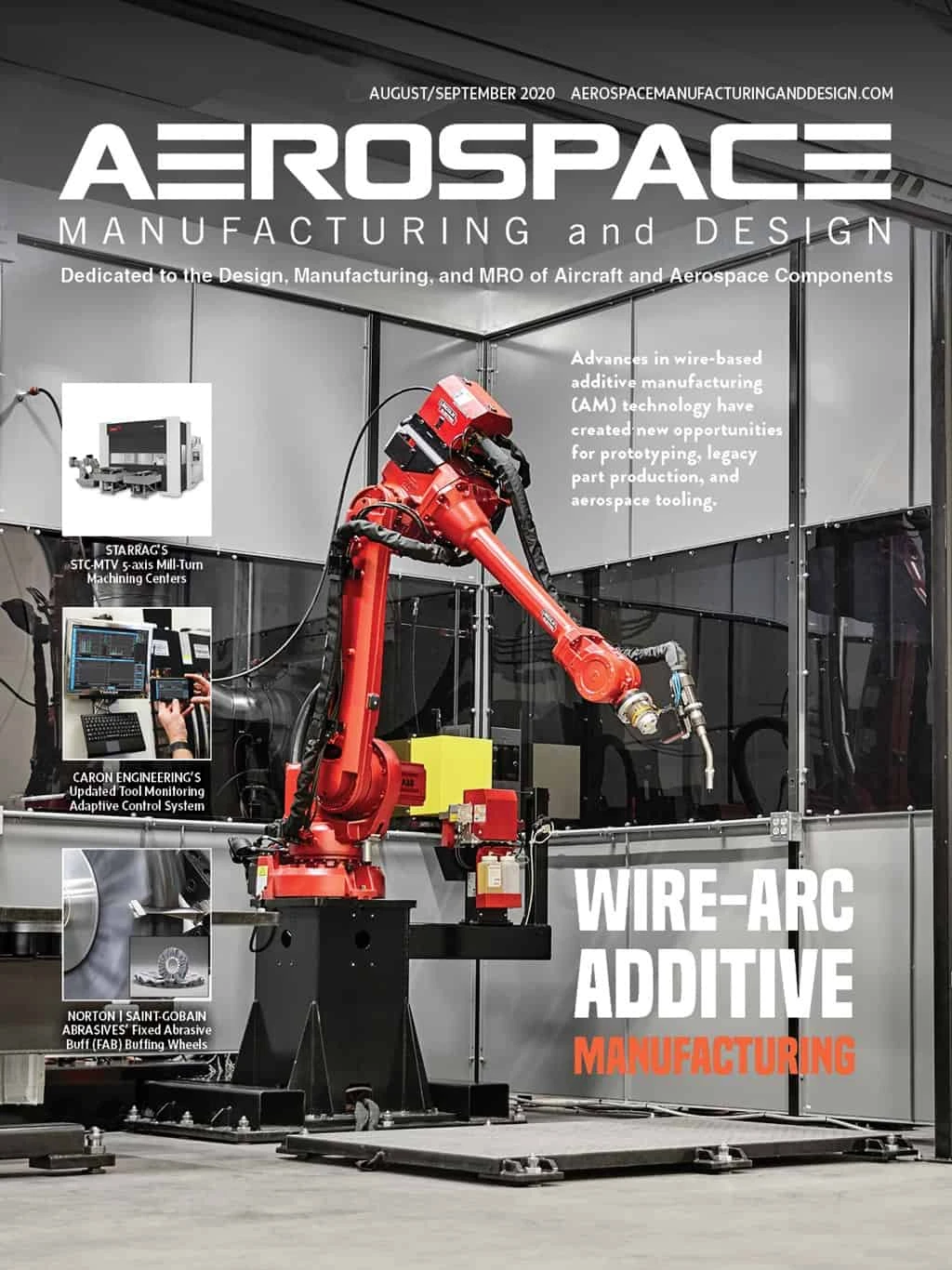
Explore the August September 2020 Issue
Check out more from this issue and find your next story to read.
Latest from Aerospace Manufacturing and Design
- Lockheed Martin completes Orion for Artemis II
- Cylinder CMMs for complex symmetrical workpieces
- University of Oklahoma research fuels UAS development
- Motorized vision measuring system
- Everyone's talking tariffs
- Boom Supersonic to launch Symphony engine testing in Colorado
- Next-generation precision measurement solution
- #60 - Manufacturing Matters: What's ahead in manufacturing in 2025?