
GKN Aerospace will relocate its North America additive manufacturing (AM) Center of Excellence to the Lone Star Commerce Center in Fort Worth, Texas. The move will strengthen its position as an additive technology leader with a larger facility, plans for an additional larger AM cell, and increased collaboration within the aerospace ecosystem.
The 100,000ft2 facility will initially house research and development of laser metal deposition with wire (LMD-w) AM technology for large-scale titanium aerostructures. GKN Aerospace will transfer existing equipment and personnel from Oak Ridge National Laboratory’s Manufacturing Demonstration Facility in Tennessee to the new site in Texas. GKN Aerospace expects to transform the facility into its fourth Global Technology Center to complement existing centers in Sweden, the Netherlands, and the UK.
GKN Aerospace will renovate the facility with office space and equipment during the next two years, while the City of Fort Worth will provide grant funding based on qualified R&D investment. When at full capacity, the center will support up to 100 personnel.
GKN Aerospace
Expanding additive manufacturing capabilities for aerospace customers

Visser Precision purchased Sapphire printers from Velo3D to expand 3D-printing capabilities for aerospace customers. One printer is the first Sapphire printer calibrated for Haynes 214 (UNS N07214), a nickel-based superalloy available as a powder for Velo3D customers. The other Sapphire printer is calibrated for Inconel 718, commonly used in aerospace and industrial applications for its high strength and corrosion resistance.
Velo3D
Visser Precision
Weber State University installs 3D printer to advance aerospace research
Weber State University, Ogden, Utah, is using 3D printing to advance its research on composite materials supporting northern Utah’s aerospace and defense ecosystem.
The university’s Miller Advanced Research and Solutions Center recently upgraded and installed the Impossible Objects Composite-Based Additive Manufacturing system, or CBAM-2. The machine prints composite materials that can then be used to design parts for high-tech applications.
Located near Hill Air Force Base, Utah, the MARS Center brings together Weber State students and faculty with industry experts who can apply innovative solutions to real-world problems, especially in the realm of national defense.
The leap in technology from the center’s previous CBAM printer will be a valuable tool in aerospace research among academia, defense, and commercial partners.
A recent example of 3D-printed parts via Impossible Objects includes a strap that keeps first-aid kits secure inside aircraft currently flown by the U.S. Air Force.
The MARS Center opened in August 2022 thanks to a $3.5 million donation from the Larry H. & Gail Miller Family Foundation. The CBAM 3D printer from Impossible Objects is among the first advanced manufacturing technologies to be installed and used at the new facility.
Weber State University College of Engineering, Applied Science & Technology
Impossible Objects
Get curated news on YOUR industry.
Enter your email to receive our newsletters.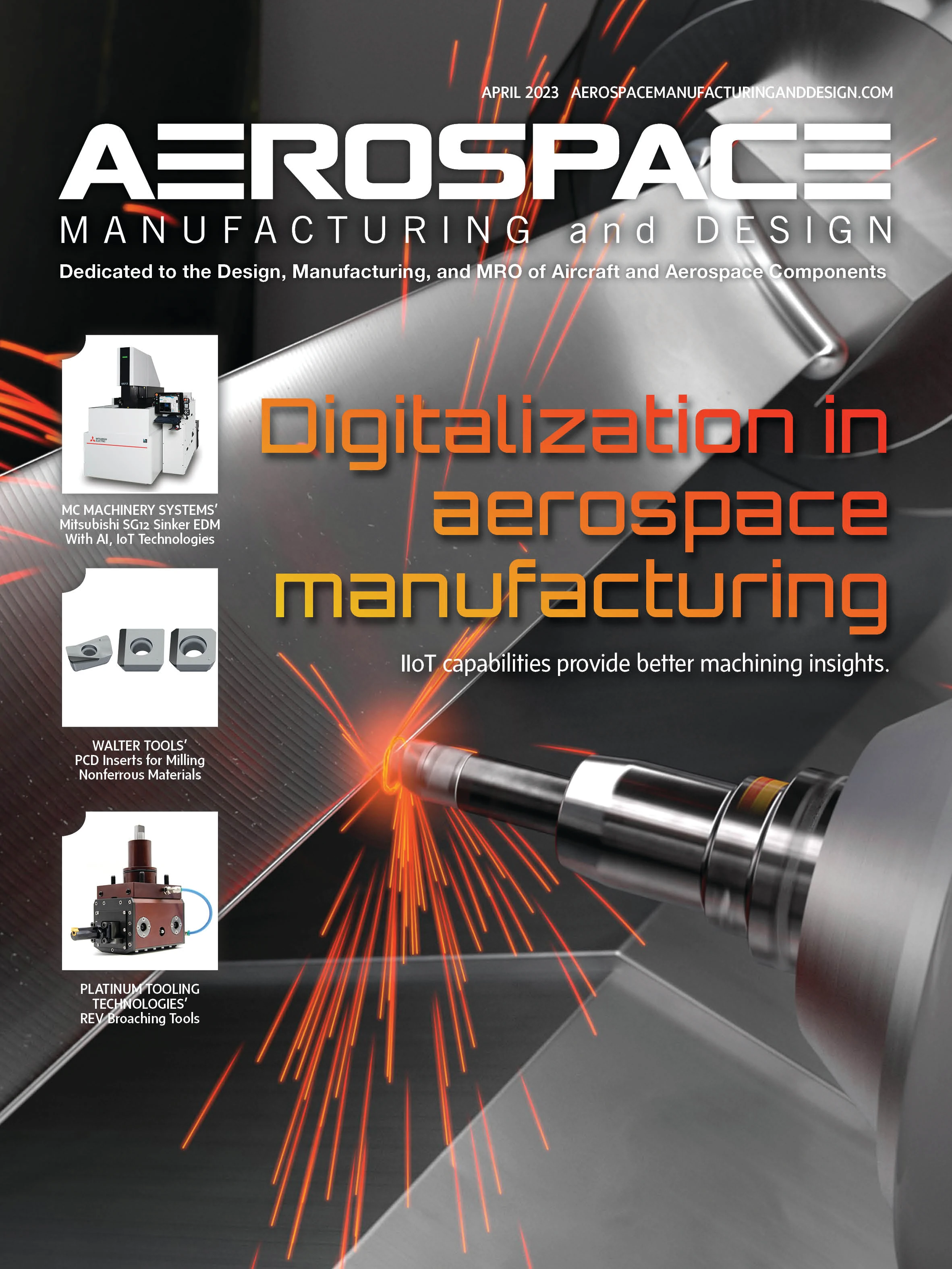
Explore the April 2023 Issue
Check out more from this issue and find your next story to read.
Latest from Aerospace Manufacturing and Design
- Philatron MIL-DTL-3432 military cables
- Beyond Aero refines its hydrogen-electric light jet
- Americase's advanced protective solutions
- Social media - what are your thoughts
- GE Aerospace secures Air Force engine contract
- Thomson Industries' online sizing and selection tool
- #53 - Manufacturing Matters - 2024 Leaders in Manufacturing Roundtable
- Join us for insights on one of the hottest topics in manufacturing!