
Non-destructive testing (NDT) is crucial to ensure the safety and integrity of components and products in many industries. The process is rapidly evolving as organizations adopt complicated systems to improve accuracy, repeatability, and efficiency. Tasked with developing a highly complex automated NDT system, Arcadia Aerospace Industries (AAI) turned to Stäubli – setting in motion a fruitful collaboration with Stäubli’s Robotics, Electrical Connectors, and Fluid Connectors divisions.
AAI specializes in custom inspection solutions for aerospace and other industries requiring advanced quality control of manufactured products. The company faced a unique challenge when a customer requested a robot-based automated NDT system requiring around 100 DC electrical connections, eight data connections, three high-flow valved fluid connections, and high-powered AC electrical connections. Manually making these connections would increase time and the risk of errors. Additionally, all components had to be housed within a single compact, lightweight unit capable of operating in a wet, dusty environment.
The required electrical, fluid, and data connectors demanded a highly flexible tool changer system that would work harmoniously with equally adaptable robots. The efficiency of the cell would depend on seamless integration of all components with AAI’s Stäubli TX200L robots. While the robots had potential, there was no solution on the market supporting all customer requirements.
A turnkey solution
“We knew it was going to require an automated solution,” says Mark Pope, engineering project manager at AAI. “Therefore, we were looking at a tool changer to add to our Stäubli robots. We’d already used Stäubli Robotics and Stäubli CombiTac connectors and wanted to marry those together.”
Teams from Stäubli Robotics, Electrical Connectors, and Fluid Connectors divisions assisted with several crucial aspects of the project. Ultimately, technologies from all three were integrated to comprise a turnkey solution from a single supplier, simplifying a complex endeavor.
Control with uniVAL drive The automated NDT system needed an elevated degree of control to ensure absolute path accuracy during tests. For this reason, a first step was to equip AAI with a uniVAL drive from Stäubli Robotics, allowing robots to be integrated into existing control platforms controlled by generic industrial multi-axis controllers. It connects to real time Ethernet-based field buses and supports major communication protocols, in this case CANopen over EtherCAT (CoE).
AAI had a multi-axis controller with a custom front end piloting its two 6-axis TX200L robots and two massive gantry systems. The NDT system required the ability to coordinate the actions of 18 different axes, making sure the tool center points follow each other, with each side coming to the same point in turn. The uniVAL drive communicates with the multi-axis controller, enabling the user to control each axis individually.
Tool change time decrease
Stäubli’s MPS robot tool changers are particularly strong in terms of multifunctionality. The team chose an automatic MPS 260 tool changer, which is flexible, allowing the integration of multiple modules for media, energy, and data connection. The MPS 260 also offered a lightweight solution, weighing only 6kg.
The automated tool changer also simplified the time-consuming process of manually switching tools. Previously, this changeover process took 30 to 60 minutes. Using the automated tool changer, it now takes only 30 to 60 seconds.
An optimal solution
The automatic robot tool changer was a natural fit for Stäubli’s unique solution. The team selected the customized CombiTac system to manage electrical and data connections, while fluid connections would be handled through standard tool changer modules.
“The Stäubli CombiTac solution allows me to use a smaller tool changer footprint to accomplish thermographic, conventional UT, X-ray, flash thermography, laser scanning – all these technologies in one very compact package that simply wouldn’t be possible in any other solution,” Pope says. In addition to saving space, the system’s multifunctional design provides optimum flexibility and operating efficiency.
The system operates under challenging conditions including water and carbon fiber dust. In fact, hydrojets are integral to the type of NDT Arcadia’s systems perform. Stäubli’s team designed components to withstand these hazards, including tool covers and water-resistant housings.
Stäubli’s TX industrial robots are designed to be adaptive. The 6-axis arm is fully encapsulated, made possible by a patented hollow shaft gearbox and no external cables. The robot was equipped with an optional pressurization kit for this application, bringing the arm to an IP65 rating, indicating resistance to sprayed water and dust.
Stäubli divisions join forces
The result of Stäubli’s collaboration with AAI is a customized turnkey solution meeting all requirements with the ability to be used for various testing procedures. The synergy between Stäubli Fluid Connectors, Stäubli Robotics, and Stäubli Electrical Connectors has delivered tremendous value for AAI.
Pope expresses complete satisfaction on behalf of AAI: “We’re endeavoring to provide a very flexible and customizable solution for our customers. Working with Stäubli, we’ve found they’ve taken our needs and met them every step of the way, no matter our size. Our needs have been their needs and they come to us with solutions very quickly.”
Arcadia Aerospace Industries (AAI)Stäubli
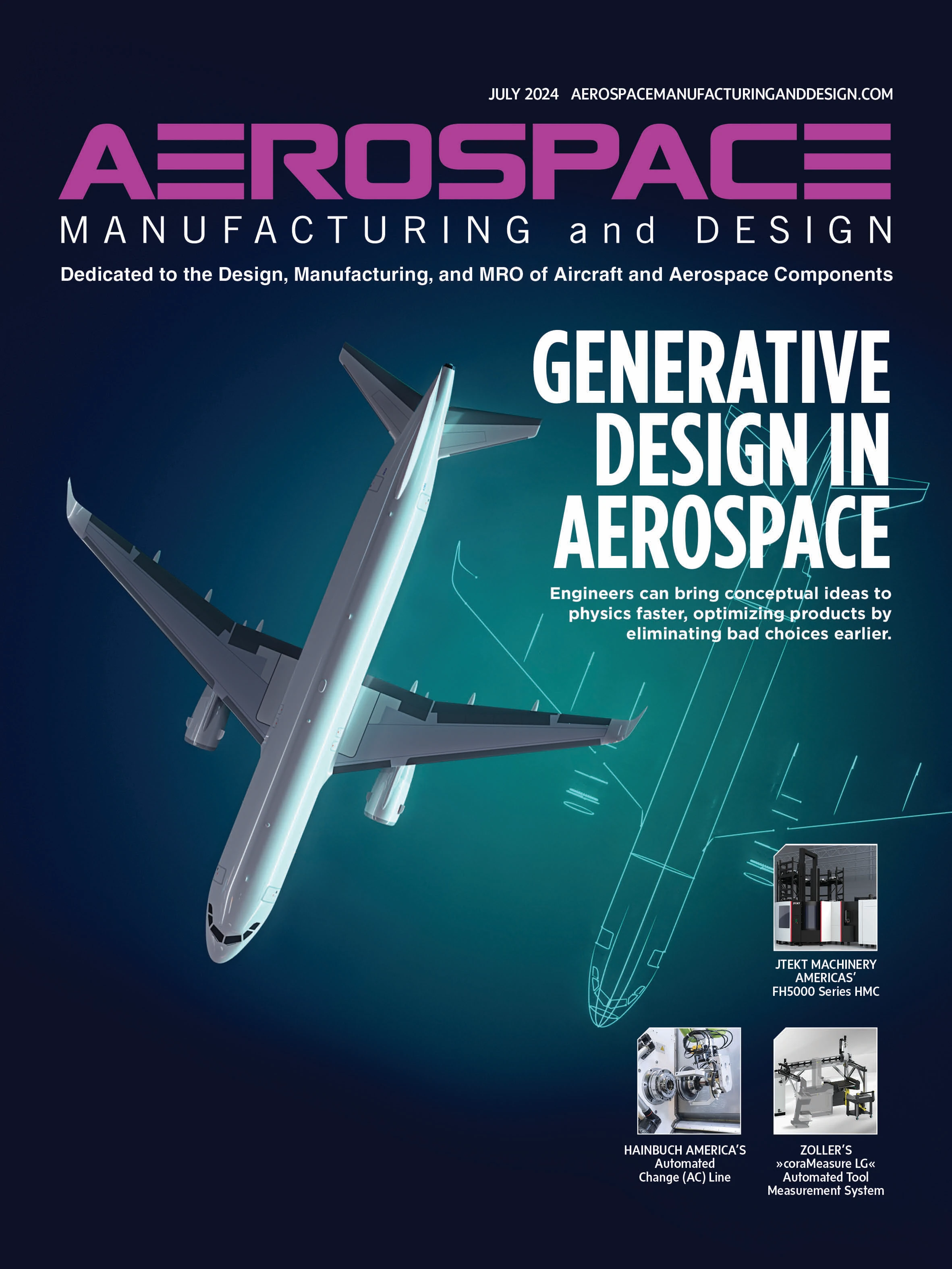
Explore the July 2024 Issue
Check out more from this issue and find your next story to read.
Latest from Aerospace Manufacturing and Design
- America Makes announces QTIME project call
- Innovation meets precision for 40% faster machining
- Upcoming webinar: Pro tips from a supply chain strategist
- Heart Aerospace relocates to Los Angeles
- Fixtureworks introduces Stablelock Clamps
- Piasecki acquires Kaman's KARGO UAV program
- PI Americas’ long-travel XY piezo nanopositioners-scanners
- AAMI project call submission deadline extended to May 12