

In modern gas and aircraft turbines, combustion temperatures of more than 1,000°C are common, requiring very stringent standards for the surfaces and materials used, as well as on manufacturing and finishing processes. Safety and reliability are of the utmost importance in all processing stages.
Because of the demands placed on quality, complex components are often finished manually, but disadvantages are high costs and more importantly, fluctuations in the finishing results. However, with the right machine, reproducible results can be achieved with high surface quality in short processing times and with more consistent quality than what can be achieved by hand.
OTEC’s stream finishing machine can deburr, round, and smooth turbine blades in a single processing stage. After they have been manufactured, turbine blades exhibit considerable initial surface roughness and excessively sharp edges and must undergo high-precision surface finishing before they can be used in an aircraft. This entails both smoothing the surface and rounding the edges.
In OTEC machines, several workpieces can be clamped in the machine at the same time to ensure high throughput. Workpieces are lowered into a rotating container filled with a grinding or polishing medium that flows around the workpiece, which also rotates independently. The surface is homogeneously smoothed, generally to Ra <0.4µm and often to Ra <0.25µm.
It is especially important to ensure that the shape of the blade is not damaged. Further, the edges can be rounded to a predefined dimension without excessively rounding the blade corners. Process times are 2 to 30 minutes.


OTEC machines also offer advances in processing speed and precision in finishing gear wheels. An objective with gear wheels is to smooth the tooth flanks or round a tooth tip. Finished gear wheels have considerably lower friction values. Gear wheels finished in OTEC machines have shown lower friction, increasing energy efficiency. A further benefit is that oil change intervals are much longer because there is less metal abrasion.
With short processing times and reliable processes, OTEC stream finishing machines are also suitable for selectively smoothing blisk surfaces.
OTEC USA
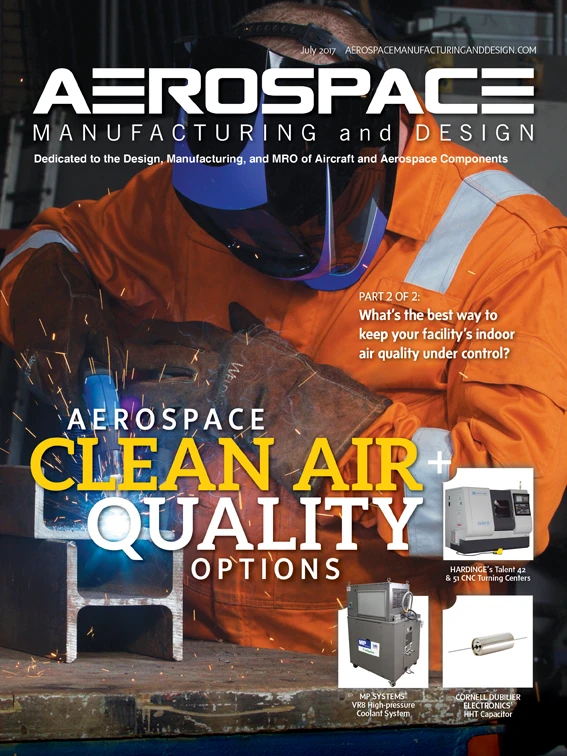
Explore the July 2017 Issue
Check out more from this issue and find your next story to read.
Latest from Aerospace Manufacturing and Design
- Taiwan’s China Airlines orders Boeing 777X passenger, freighter jets
- Reamer re-tipping extends life of legacy tooling
- Revitalizing the Defense Maritime Industrial Base with Blue Forge Alliance
- Safran Defense & Space opens US defense HQ
- Two miniature absolute encoders join US Digital’s lineup
- Lockheed Martin completes Orion for Artemis II
- Cylinder CMMs for complex symmetrical workpieces
- University of Oklahoma research fuels UAS development