
Growing electrification in aerospace increases complexity throughout multiple development phases. Equally important, it impacts regulatory compliance. Key program compliance milestones now carry a high degree of risk, and with aerospace original equipment manufacturers (OEMs) under intense pressure to deliver aircraft on time, electrification further complicates matters.
The dramatic increase is largely due to aerospace OEMs increasingly turning to electrical systems for differentiation. It’s important to understand two distinct facets of electrification: onboard power generation and implementation of new electrical solutions, such as fly-by-wire control systems and advanced multi-function cockpit displays.
Electrical and electronic (E/E) content has grown substantially during the past 20 years, and platform electrical power demand has grown 10x during the last 50 years as electrical solutions replace traditional mechanical, pneumatic, and hydraulic implementations.

Old designs
When designing and integrating multiple electrical systems into an aircraft, as well as demonstrating compliance, old methods don’t scale well as complexity increases. Aerospace OEMs are still using semi-manual methods and physical hand-offs to exchange data between engineering groups – analysis practices established long before modern electrification, when electrical systems were relatively simple. Compliance issues found using old methods often appear late in the design process, forcing expensive iterations and costly setbacks.
In a commercial aircraft, engineers must consider thousands of electronic devices/units, miles of electrical wiring, a multitude of configurations to implement, and numerous safety and certification requirements. Manual or physical requirement hand-offs, work-in-process design data, and final product descriptions are no longer practical.
Digital twin technology
One of the biggest developments to address growing electrification complexity is the digital twin – a virtual representation of a physical product that can be used to analyze and predict outcomes of the physical counterpart. The digital twin provides a core model of the product, the processes used to produce it, and its performance throughout its life cycle.
The potential applications for a digital twin depend on what stage of the product life cycle it models. There are typically three types of digital twin – product, production, and performance (Figure 1, page 30). A digital twin of product, production, and performance provides a core model of the product life cycle, allowing engineers to create, iterate, replicate, and improve valuable programs. It creates data coherency and stability, integration, and advanced automation, which significantly de-risks and streamlines platform electrical system design and integration. As more OEMs employ the digital twin, reliability and time to market will dramatically improve. The digital twin model also offers lifecycle cost analysis and savings, faster maintenance turnaround times, and greater platform operational availability. It also provides feedback throughout the entire value chain.
The digital thread reaches back to the early stages of product design and spreads rich data forward into platform production, maintenance, and operation. It allows designers, fabricators, assemblers, suppliers, maintainers, and operators to create a full, closed-loop decision environment for continuous optimization throughout all aspects of the value chain during the years of platform development and the decades of platform operation.
Compliance
As electrification increases, the importance of compliance and its associated complexities must be addressed in a cohesive and comprehensive manner.
Mentor’s software compliance tool, Capital Load Analyzer, lets OEMs address these concerns. The tool helps engineers address the impact of electrical complexity on electrical loads by leveraging automation and digital data continuity to facilitate regulatory compliance for electrical load analysis. The solution provides comprehensive analysis of safe electrical design for all flight phases – even emergency conditions (Figure 3, page 32). The tool offers a digitalized approach to electrical compliance and creates one integrated report for each configuration.

Looking forward
The Capital suite of E/E tools provides a mature, end-to-end digital thread for electrical system design and integration. Its electrical environment spans the full electrical system value chain – electrical system definition, design, manufacture, support, and maintenance.
As electrification and complexity continue to increase – in electrical system design and compliance – moving to a more automated process can help OEMs and their value chain partners. Adopting more modern methods will allow the aerospace industry to increase production rates, realize tighter cost controls, make more just-in-time deliveries, produce a higher percentage of first-time quality deliverables; and develop a highly functioning supply chain with numerous collaboration and innovation possibilities.
“As more OEMs employ the digital twin, reliability and time to market will dramatically improve.”
Integrated Electrical Systems, Mentor, A Siemens Business
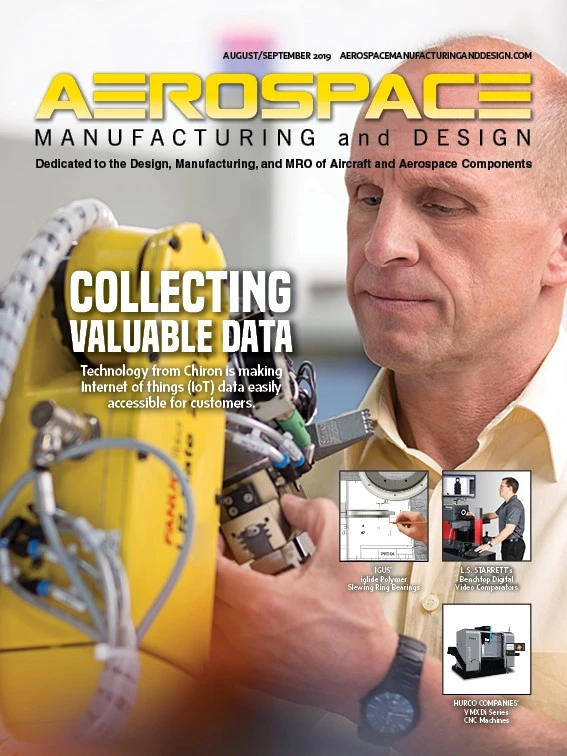
Explore the August September 2019 Issue
Check out more from this issue and find your next story to read.
Latest from Aerospace Manufacturing and Design
- Malaysia Aviation Group orders 20 more Airbus A330neo widebodies
- More displacement from space-tested piezo actuators
- Textron Aviation to bring its largest-ever lineup to 2025 EAA AirVenture
- Qualified materials for 3D-printing mission-critical applications
- #69 Manufacturing Matters - Shopfloor Connectivity Roundtable with Renishaw and SMW Autoblok
- Demystifying Controlled Unclassified Information (CUI)
- Simplify your shop floor operations while ensuring quality parts
- Happy Independence Day - July 4th