Digitalization is becoming more common as component and system manufacturers develop ways to make their products more intelligent. Potential benefits – increased efficiency and responsiveness in a production environment – are clear, but there is still uncertainty about how and when the full benefits of the fourth industrial revolution, Industry 4.0, will materialize.
Several factors need to coalesce for Industry 4.0 to become a reality. Political and economic incentives, correct investment in skills and training, and the availability of advanced tools for easy implementation will all affect the pace of adoption.
Global contrasts
Around the world, the economic, political, and technological drivers for Industry 4.0 adoption vary. In Germany and the United Kingdom, Industry 4.0 is viewed as the route that will lead to the emergence of smart industry; where people, devices, objects, and systems combine to form dynamic, self-organizing networks of production, made possible by technological advances that constitute a reversal of conventional production process logic.
For the United States, the emphasis is more on the role of Big Data in collaboration, and Industry 4.0 has become synonymous with the Industrial Internet of Things (
In China, where labor and materials costs are rapidly increasing, digitalization is being championed to transform outdated production methods. Many Chinese manufacturers are still operating in the age of Industry 2.0. However, the political impetus for change is evident in China Manufacturing 2025, a government plan to transform the country into an advanced production nation by the middle of this century. This initiative will see heavy investment in Internet architecture, Big Data, and cloud computing, leading to more intelligent factories. The necessary pace of change is incomparable with other developed nations: China is looking to take a careful, methodical approach to the digitalization of manufacturing, seeking partnerships with more experienced nations along the way.

Industry variations
Adoption of Industry 4.0 principles also varies between industries. The automotive sector is well-advanced in the adoption of automation, data interchange, and advanced production technologies – requirements of high-volume, high-quality, cost-sensitive manufacturing. This sector views process control as the means to advance the quality of production processes while reducing operating expenses. In component production plants, Industry 4.0 implementation offers considerable potential, especially in predictive maintenance. Continuous recording and analysis of process data
By contrast, the aerospace industry has been slower to
The need to bring innovative products to market faster is being felt in many industries. Industry 4.0 offers the means to completely digitalize the product development life cycle, in turn allowing manufacturers to provide customers accurate traceability, quality control, and
Individual responsibilities
In addition to global and industry sector differences, successful adoption of Industry 4.0 relies on the human factor – our willingness to understand, embrace, and deliver change. According to Harvard Business Review’s “From Data to Action” report, the most difficult aspect for organizations to change on the route to smarter factories is internal culture.
Successful implementation of Industry 4.0 requires strong leadership; the person at the top must set the example and be seen fully embracing change, committing to it, and communicating it in a compelling way. The philosophy of making fact-based decisions using quantitative manufacturing data will need to be coached into all levels of management. People at every level of the organization need to understand how they benefit from Industry 4.0. For example, collaborative robots (
Tooling up
A smart factory requires products embedded with systems, sensors, and actuators linked together via the Internet – including assembly tools. Intelligent tools must support operators as they adapt to Industry 4.0 techniques. In the past, assembly workers were valued because they could perform the same task competently on the same line day after day. In a smart factory, workers may be required to rivet body panels one shift and wire up a lighting system the next. Traditional training in all these skills takes time – and the pace of technological change can quickly render such learning obsolete.
How can we ensure that modern assembly workers feel valued and competent and can access information to complete diverse tasks efficiently and without error? One answer is PivotWare, a process control platform that guides operators through a specific set of assembly tasks as part of an automated process. A graphical and textual display shows exactly what tools to use, what components to apply, and where to fix them. The system verifies each step is completed correctly before the operator can move to the next stage. The platform is programmable by the customer, so responsiveness to changes in production requirements is unhampered.
Specialists such as Desoutter are already developing the next generation of tools that can deliver Industry 4.0 capabilities and support the smart factory model. Tomorrow’s operating platform will deliver a major step-change in multi-tool management, offering far greater connectivity and flexibility than is currently possible.
Conclusion
Industry 4.0 may have some way to go, but it is gathering pace. Governments acknowledge its potential to deliver wealth and job security and are taking steps to help make the transition. Forward-thinking companies also recognize that they have to invest in the latest technologies if they want to improve production efficiency. There is also a growing awareness of how we need to make sure that people are equipped with the right tools to be more flexible and adaptable. If we want these things to happen quickly, we must all play our part in accelerating the transformation.
Desoutter Industrial Tools Inc.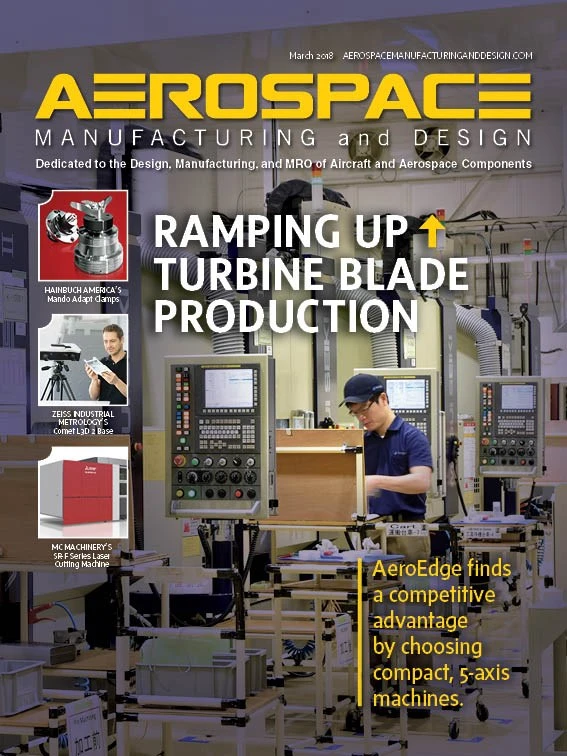
Explore the March 2018 Issue
Check out more from this issue and find your next story to read.
Latest from Aerospace Manufacturing and Design
- 2024 Favorites: #10 Article – How 3D-printed aviation parts can accelerate return to air
- 2024 Favorites: #10 News – Boom Supersonic completes Overture Superfactory
- OMIC R&D hosts Supporting Women in Manufacturing Day 2024
- 4D Technology's AccuFiz SWIR interferometer
- Seventh Lockheed Martin-built GPS III satellite launches
- KYOCERA AVX's CR Series high-power chip resistor
- UT researchers receive Air Force grant for wind tunnel
- Monticont's linear voice coil servo motor