
In October 2020, Boeing Co. officials announced the company was restarting its 737 MAX jetliner program. That was good news for brothers Josh and Andrew Baskins, co-founders of Baskins Machined Products LLC (BMP) of Collinsville, Oklahoma, which began tooling up for the aircraft in 2017. Starting with a single special-order MA-600 II horizontal machining center (HMC) from Okuma, this nine-year-old, 20-person job shop soon had a dozen such machines sitting on its production floor, all optimized for one thing: cutting titanium.
Maxing out
“We were a 737 MAX production shop,” says Andrew Baskins. “In all, we had 14 machines dedicated to that particular program, most with high-torque, 6,000rpm, HSK 100 spindles and a 5-axis rotary attachment on one side of the table. They were custom-built for milling large titanium components like those used on the MAX and other aircraft. So, between COVID-19’s effect on the travel industry and Boeing’s decision to ground the planes, it basically decimated us.”
Still, if you can mill titanium, you can mill other tough metals, so the Baskins picked up the pieces, keeping the machines as busy as possible. Given the MA-600’s large machining envelope (39.37" x 35.43" x 39.37") and relatively sedate spindle speeds, however, it hasn’t always been an easy task, which is why the MAX restart is such welcome news.
“It’s been a rough year, that’s for sure, but we’re one of many shops in the same situation,” Baskins says. “The difference is, we have the ability to pull out of it. We’ve picked up a lot of military work and are doing some pretty amazing parts, so even though we’ve missed the MAX and are looking forward to ramping up again, we’ve also managed to stay fairly busy.”

Beyond titanium
BMP isn’t limited to machining titanium and hard metals. The shop is also well-equipped for aluminum machining, boasting a handful of 3-axis and 5-axis vertical machining centers (VMCs) with 12,000rpm spindles and higher, as well as a pair of live-tooling CNC lathes. Add to that a team of experienced programmers and manufacturing engineers, and there’s little they can’t produce.
Yet, even the best programmer has a bad day now and then, so the Baskins decided to make another purchase while investing millions of dollars in HMCs: Vericut toolpath simulation and optimization software from Irvine, California-based CGTech Inc.
“Originally, it was just me doing all the programming and prove-outs,” Baskins says. “I would use the simulation that’s built into our CAM software, and then step through all my programs at the machine very cautiously. And while that worked for a time, it became a bigger risk as we started adding more people and equipment. It’s just too easy for someone to make a simple mistake that’ll end up costing way more than Vericut, so we felt that we were at a turning point, that there were too many opportunities for something really tragic to happen. That’s why we bought Vericut.”
Empowering people
Baskins still programs, but he’s now accompanied by five members of the BMP engineering team, each responsible for taking first-time jobs from start to completion. “Whoever is assigned a new part will develop the process plan, program the part, design and build the tooling, set up the machine, and run the first job,” he explains. “It’s one person managing everything from beginning to end, and once the process is deemed good, we send it over to production.”
One team member includes Product Development Manager Don Javier, who’s quite pleased with BMP’s way of doing things. “I worked as the programming manager at another shop and all I did was program parts and manage the department,” he says. “Working here provides instant feedback on the processes that you create and the tooling you select. It’s a lot more hands-on, something all of us enjoy.”
Javier used Vericut at his last job, so he was well-prepared to help Baskins and his coworkers implement the toolpath simulation software when he came aboard. Six machines on his first day eventually turned into 23, all of which he modeled in Vericut.

Hindsight is 20/20
“Vericut’s especially helpful with fixture design and during the setup and programming processes,” Javier says. “A lot of times, you’ll start out one way and see that there’s tooling interference, for example, or a machine over-travel, and you can fix the problem before it affects the machine. It helps you make better decisions upfront. And while I used to keep track of how much time we saved when we first got Vericut, it’s become such an integral part of what we do here that we no longer bother keeping track. We know Vericut’s value, even though I can’t quantify it for you.”
Baskins agrees. He notes that all six of BMP’s programmers use Vericut, 100% of the time. In hindsight, his only regret is that they didn’t buy it sooner. “I consider myself an excellent programmer and am extremely careful to never release anything to the floor that’s going to crash a machine, but everyone makes mistakes,” he says. “So even though we didn’t have the money to do everything we wanted early on, Vericut was always on the top of our wish list. Fortunately, we never got bit by not having it, but it could easily have gone the other way.”
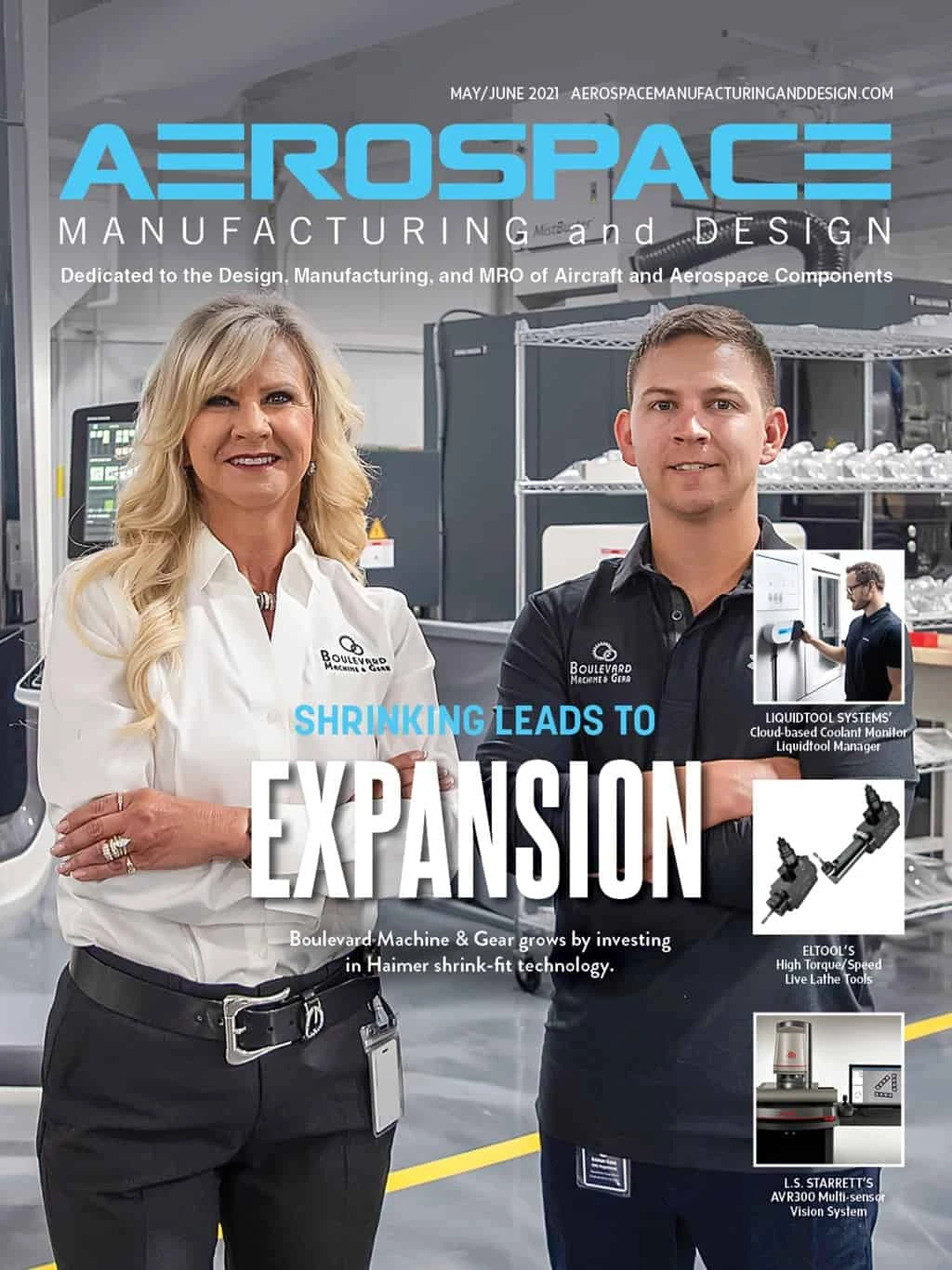
Explore the May June 2021 Issue
Check out more from this issue and find your next story to read.
Latest from Aerospace Manufacturing and Design
- GE Aerospace secures Air Force engine contract
- Thomson Industries' online sizing and selection tool
- #53 - Manufacturing Matters - 2024 Leaders in Manufacturing Roundtable
- Join us for insights on one of the hottest topics in manufacturing!
- You can still register for March’s Manufacturing Lunch + Learn!
- Ohio creates Youngstown Innovation Hub for Aerospace and Defense
- Tormach’s Chip Conveyor Kit for the 1500MX CNC Mill
- How to Reduce First Article Inspection Creation Time by 70% to 90% with DISCUS Software