The aerospace manufacturing industry requires cutting-edge processes to enable necessary efficiency and durability within tight size, weight, and power (SWaP) requirements and current machining techniques may be insufficient, giving rise to less conventional methods such as pulsed electrochemical machining (PECM).
In PECM, a workpiece and a tool in its inverse shape are positioned with a tiny gap between. An electrolyte solution flows through the gap to remove waste materials from machining. The inversely shaped tool moves toward the workpiece, and a pulsing DC current is applied – dissolving the workpiece material until the desired shape is achieved.

Turbines, impellers, blisks
Turbomachinery components are subjected to high forces, require complex 3D surfaces, and demand tight tolerance features. Components such as bladed discs (blisks) and integrally bladed rotors (IBRs) are a growing but demanding application which embodies many of these challenges. Normally manufactured by forging a large nickel- or titanium-alloy disc followed by 5-axis CNC milling of the complex airfoil geometry, as airfoils become thinner or include advanced 3D features or tip geometries, high CNC milling speeds become difficult due to blade vibrations or access between airfoils. Similar geometric challenges also exist with non-rotating components such as stator and vane segments.
Alternative methods such as casting, powder metallurgy, friction welding, or additive manufacturing (AM) all have the potential to reduce material use but come with their own challenges. Casting involves differential cooling rates for thin airfoils vs. thick walls in the hub, creating material stresses that can cause cracks in large components. Some AM and powder metallurgy techniques also have scale limitations due to thermal distortions. In general, near-net techniques also come with additional material property risks which have not been fully addressed for critical components. Finally, in most cases, near-net options require final machining to correct any tolerance distortions or improve surface finish, especially in applications with high Mach number airflow.
Many rotating and static turbomachinery components, including blisks/IBRs, turbines, and impellers, have shared design and manufacturing challenges. They’re all highly sensitive to geometrical deviations and material properties and any variation can compromise the component’s efficiency and lead to imbalances while in use.
Fortunately, PECM poses a worthwhile alternative value proposition. PECM is neither a thermal nor contact-based process, meaning cooling rates and vibrations from cutting are nonexistent. Instead, PECM dissolves the material atom by atom to the desired shape while permitting high aspect ratios and maintaining an attractive material removal rate. The precise shape and smooth surfaces made possible by PECM greatly improve the efficiency of the turbomachinery. PECM is also flexible and can be used for bulk material removal or final finishing of a near-net manufactured part.


Metal AM, then PECM
With the increasing prevalence of AM in aerospace, it’s worth noting that PECM can also be used as a finishing process, not just the primary machining method.
Metal AM has found footholds in aviation engines (combustion devices, housings, heat exchangers), rocket engines (injectors, combustion chambers, impellers), and a range of satellite applications. However, surface roughness is a common issue in 3D printing, particularly remnants from support structures. These surface irregularities can lead to incorrect fit, increased friction, corrosion, and cracks. However, PECM can address surface roughness in post-processing. Although PECM has similarities to electropolishing, it differentiates itself by using a locally small gap between electrode and workpiece. Custom PECM methods developed by Raleigh, North Carolina-based Voxel Innovations make it especially efficient for removing macro-level roughness associated with AM support structures, downskin surfaces, electron beam melting (EBM) powder bed, or freeform AM methods.
Metal AM also has limits on wall thickness and aspect ratios and can be challenged with distortions due to the inherently thermal nature of the process. Instead of compromising design to work within these limits, PECM creates thin-walled or critical features in a secondary machining step.
Another potentially cost-effective solution may be to add extra stock material to the AM part’s surface, then use PECM to dissolve the extra material into tolerance. Similarly, the metal AM build parameters could be adjusted to speed up the deposition rates while using PECM to address the resultant geometry more efficiently. As metal AM grows into more volume production applications, a hybrid approach of metal AM followed by PECM may be a more efficient, effective manufacturing approach.
High-temp applications
Material choice is a careful balancing act, particularly in aerospace, and design engineers must optimize for bonding and joining concerns, corrosion, system mass, and cost, all while considering thermal resistivity and matching coefficients of expansion.
In high temperature applications in liquid rocket engines or hypersonic systems, these needs cannot be met by standard material choices. Ceramics and ceramic-composites with high thermal conductivity and resistance to corrosion may seem like an ideal solution, however, their cost, bonding challenges, and forming limitations impede broader implementation. That leaves high temperature metal alloys including nickel super alloys, titanium aluminides, refractory metals, and high entropy alloys that can be difficult to machine conventionally due to heat and wear resistance – exactly the reason they’re used in high-temperature applications. The difficulty of machining these materials is especially problematic in heat exchangers, given that these components function at their highest efficiency only with high aspect ratios, thin walls, and tight spacing. Many conventional machining processes rely on heat or contact to form features, which can deform thin walls and may lead to irregular channel sizes (and uneven heat flow) or incorrect fit with other components. Many electronics applications require a different set of material choices. Chip-level cooling and high-power radio frequency (RF) or microwave devices in airborne applications may require low coefficient of thermal expansion (CTE) or matching thermal expansion of another material (e.g., silicon). This can include materials such as metal matrix composites, refractory metals, or low CTE Invar and Kovar – all challenging to manufacture. In addition, these electronics applications often require precise depth and wall thickness control to manage heat transfer and packaging requirements. Cryocoolers used for cooling infrared cameras sensors are another example of hard-to-machine geometries, given the typical requirement of high aspect ratio cooling features.



Traditional CNC milling or EDM may be too slow, too expensive, or lead to compromised designs. In contrast, PECM is insensitive to the mechanical properties of the materials and can machine nickel super alloys as fast as copper or aluminum. In addition, the low forces make it an especially good fit for thin wall features and high aspect ratios.
Sponsored Content
MORE THAN A TRUCK.
Hino trucks power through the toughest challenges with proven durability, performance, and exceptional comfort. With Hino Edge connectivity, an exclusive standard 5-year Allison Transmission warranty, and 24/7 HinoWatch roadside assistance, our support goes beyond the sale. With The Ultimate Ownership Experience, Hino always delivers MORE THAN A TRUCK.
Sponsored Content
MORE THAN A TRUCK.
Hino trucks power through the toughest challenges with proven durability, performance, and exceptional comfort. With Hino Edge connectivity, an exclusive standard 5-year Allison Transmission warranty, and 24/7 HinoWatch roadside assistance, our support goes beyond the sale. With The Ultimate Ownership Experience, Hino always delivers MORE THAN A TRUCK.
Sponsored Content
MORE THAN A TRUCK.
Hino trucks power through the toughest challenges with proven durability, performance, and exceptional comfort. With Hino Edge connectivity, an exclusive standard 5-year Allison Transmission warranty, and 24/7 HinoWatch roadside assistance, our support goes beyond the sale. With The Ultimate Ownership Experience, Hino always delivers MORE THAN A TRUCK.
Sponsored Content
MORE THAN A TRUCK.
Hino trucks power through the toughest challenges with proven durability, performance, and exceptional comfort. With Hino Edge connectivity, an exclusive standard 5-year Allison Transmission warranty, and 24/7 HinoWatch roadside assistance, our support goes beyond the sale. With The Ultimate Ownership Experience, Hino always delivers MORE THAN A TRUCK.
Sponsored Content
MORE THAN A TRUCK.
Hino trucks power through the toughest challenges with proven durability, performance, and exceptional comfort. With Hino Edge connectivity, an exclusive standard 5-year Allison Transmission warranty, and 24/7 HinoWatch roadside assistance, our support goes beyond the sale. With The Ultimate Ownership Experience, Hino always delivers MORE THAN A TRUCK.
Ultimately, cost is among the most decisive issues for any manufacturing process. Parallel production, made possible through PECM, creates many slots, pockets, or other features simultaneously in the same vector, enabling higher density features, faster production, and lower cost per part.
PECM excels in smooth surfaces, high aspect ratios, high feature density, and thin walls, even in hard-to-machine materials. All of this may be achieved in large quantities and at comparatively low cost, which is why aerospace companies should consider leveraging PECM.
Get curated news on YOUR industry.
Enter your email to receive our newsletters.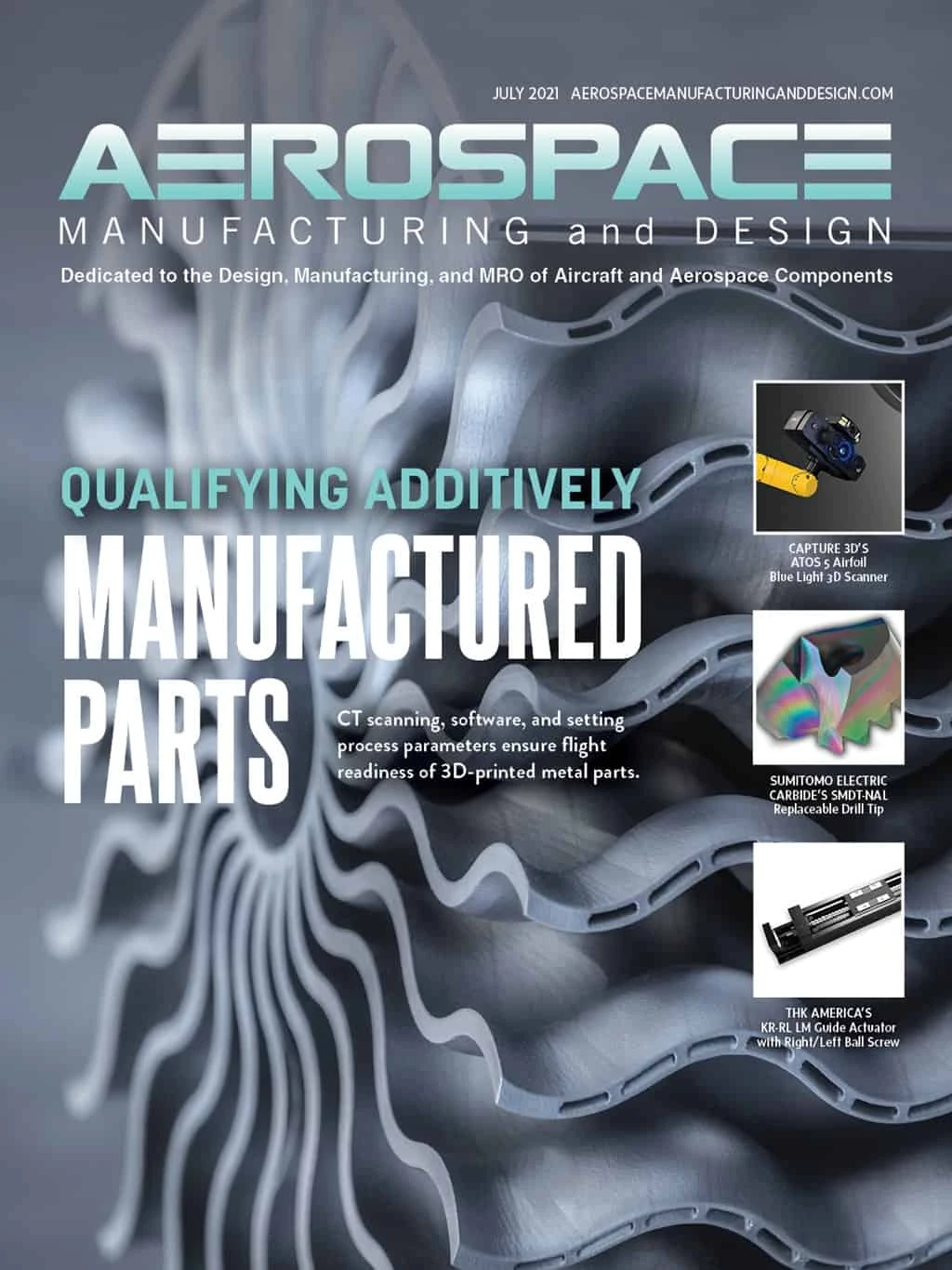
Explore the July 2021 Issue
Check out more from this issue and find your next story to read.
Latest from Aerospace Manufacturing and Design
- Guill Labs offer materials and extrusion testing
- High production vertical honing systems
- July Manufacturing Lunch + Learn webinar with OPEN MIND Technologies
- July Manufacturing Lunch + Learn webinar with Techman Robot
- Hexcel and NIAR expand collaboration
- Open aperture XY alignment stage
- Close out July with our Lunch + Learn on medical machining solutions
- Build your Controlled Unclassified Information (CUI) toolkit