
Thermwood recently printed several sections from a 51ft long yacht hull mold to demonstrate how only a single mold may be needed for the manufacture of larger vessels. This concept can be applied to multiple industries, such as aerospace, automotive and foundries, as well as for applications in the marine industry.
The printed sections of this test mold are made of carbon fiber reinforced acrylonitrile butadiene styrene (ABS) from Techmer PM. ABS was chosen because of its physical properties and relatively low cost compared to other reinforced thermoplastics.
The demonstration
Thermwood printed a 10ft section from a 51ft long yacht hull mold on a 10ft x 10ft large scale additive manufacturing (LSAM) MT, the smallest and lowest cost additive manufacturing (AM) system currently available from Thermwood. The entire mold section, made of four printed pieces, weighs 4,012 lb and required 65.5 hours to print.
This rather unique mold design was specifically developed for AM. It’s printed in sections, each about 5ft tall. These printed sections are then bound together chemically and mechanically using high strength polymer cables into two mold halves. The two mold halves then bolt together to form a complete female mold for the yacht hull.
The process
Each mold section has a molded-in rocker. When the mold is fully assembled, it rests on the floor on these rockers. At this point, the mold can be rolled over to tilt about 45° to either side, kind of like a giant rocking chair. This allows for easier access during the layup process. A set of molded wedges are clamped to the rockers to hold the mold in the desired position. Once the hull has been laid up and fully cured, the mold is rolled to level and the printed wedges are clamped to both sides, holding them level. Then the two mold sides can be unbolted and slid apart to release the finished boat hull.
The test pieces Thermwood printed show that this approach will work in practice. Certain thermosets will work directly on the ABS molded surface using just traditional mold release practices; however, other thermoset materials are based on solvents that can chemically attack the ABS polymer.
To prevent this, Thermwood has experimented with several protective coatings including traditional mold gel coats. While virtually all of the coatings tested worked at room temperature, large thermoset molds often experience some heat as a result of the exothermic reaction that occurs during the thermoset curing process. Thermwood tested each coating at 200°F and found that some worked at room and elevated temperature, while others that worked at room temperature did not work well at the elevated temperature.
While it appears that this approach will work today for certain thermosets, the ideal would be to develop a low-cost polymer that is chemically resistant to the other thermoset solvents and eliminate the need for a protective coating.

The bottom line
This demonstration shows that, if you need a really large part for anything from aerospace to a marine application, you don’t necessarily need a really large machine. With a little imagination and some creative engineering, really large structures can be made, even on smaller, lower cost additive manufacturing systems.
Thermwood
http://www.thermwood.com
Get curated news on YOUR industry.
Enter your email to receive our newsletters.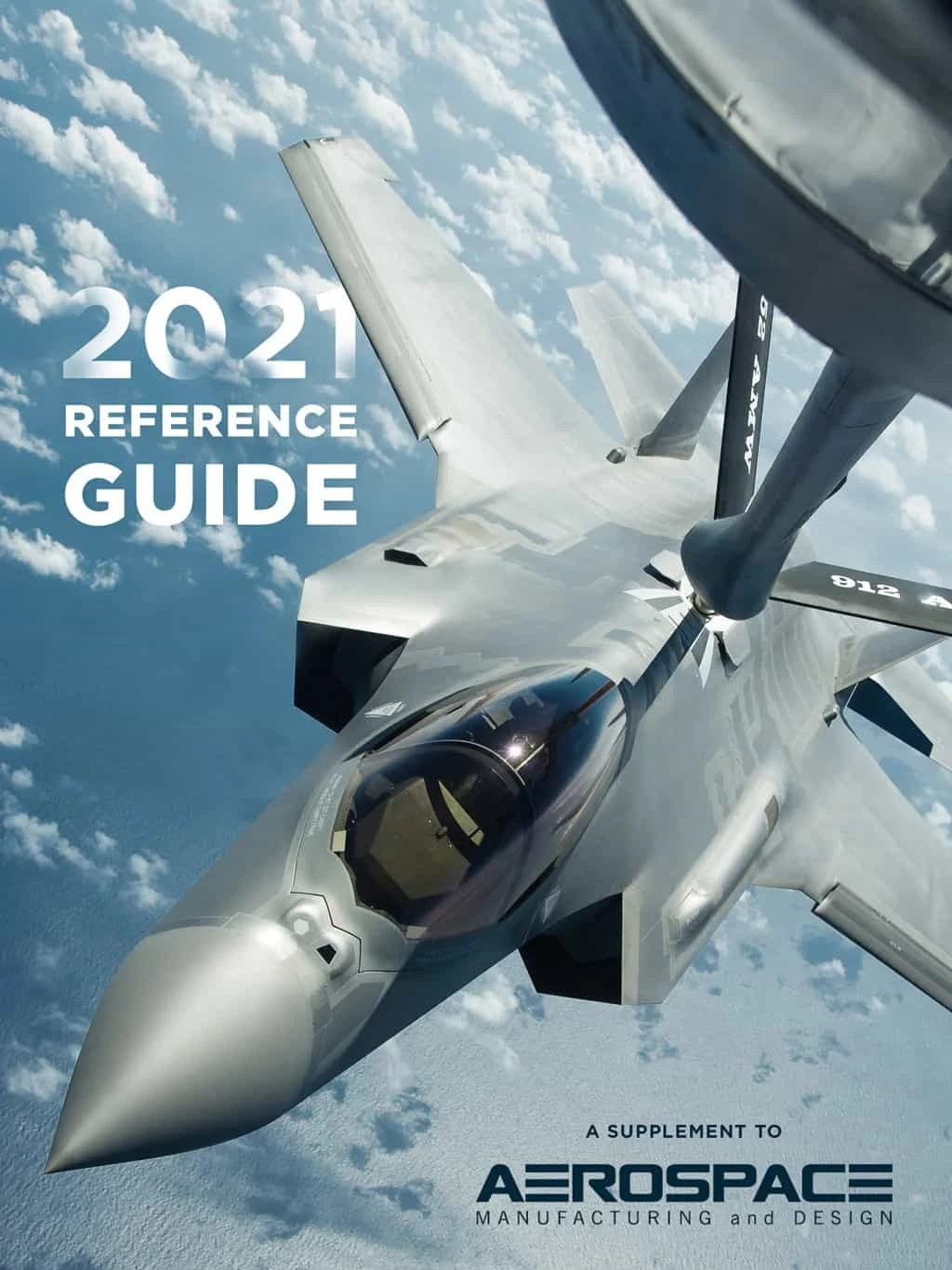
Explore the AMD Reference Guide 2021 Issue
Check out more from this issue and find your next story to read.
Latest from Aerospace Manufacturing and Design
- Beyond Aero refines its hydrogen-electric light jet
- Americase's advanced protective solutions
- GE Aerospace secures Air Force engine contract
- Thomson Industries' online sizing and selection tool
- #53 - Manufacturing Matters - 2024 Leaders in Manufacturing Roundtable
- Join us for insights on one of the hottest topics in manufacturing!
- You can still register for March’s Manufacturing Lunch + Learn!
- Ohio creates Youngstown Innovation Hub for Aerospace and Defense