

When recommending grinding equipment to produce reamers, I’ve wondered why reamers have centers and why some users still insist on buying reamers with centers.
Historically, reamers have been manufactured using a cylindrical grinding operation while the reamer blank is held between centers. For carbide reamers, this entails drilling a hollow (female) center prior to pressing and hardening. Then, the female center is polished by spinning a cone inside it, using abrasive polishing paste.
The two primary components crucial for accuracy in producing reamers are the total indicator reading (TIR) on the cylindrical land in relation to the shank and the lip height on the chamfer cutting edges.
One reason reamers (particularly HSS) historically have centers is the convenience of resharpening them on manual grinding equipment. Reamers are clamped between centers and a mechanical finger is positioned under the 45° cutting chamfer. A cup wheel regrinds the chamfer. For each chamfer, the finger is re-positioned, ensuring consistent lip height regardless of the flute spacing.
However, the reality is centers are never used in the reaming operation since the reamers are typically chucked on the shank, just like a drill or endmill.
There are more modern methods for producing carbide reamers without needing centers. The latest advances in CNC peel and pinch grinding can produce carbide reamer blanks to high accuracy and finish requirements at reduced manufacturing costs.
Peel and pinch grinding (a.k.a. single point grinding) is a cylindrical grinding process where a roughing and a finishing wheel interact simultaneously on the blank from the back and from the front. The roughing wheel, positioned slightly ahead radially and axially, removes most of the material, while the finishing wheel provides the final finish and tight diameter tolerances. Since the blank is pushed through a V-block system, constant support is maintained, resulting in very low TIR measurements.
This process is suitable for chucking reamers, reverse-shank reamers, and stepped reamers, although some designs may require multiple setups.
Grinding the flutes and cutting chamfer is then performed on an automated CNC tool grinding machine. Typically, flute spacings are uneven (staggered) which reduces vibrations and chatter.
For long-flute reamers, a half-round steady rest can be used. This might seem expensive, as there are endless reamer diameters including custom sizes; however, the cost of manufacturing these supports is still less than the labor-intensive process of installing centers into each reamer blank manually.
Peel grinding and tool grinding can be automated. Additionally, hybrid grinding models combine peel and tool grinding capabilities in a single machine.
Persuading users to move away from requiring centers will ultimately reduce the cost of producing reamers, particularly carbide reamers.
MyGrinding Inc.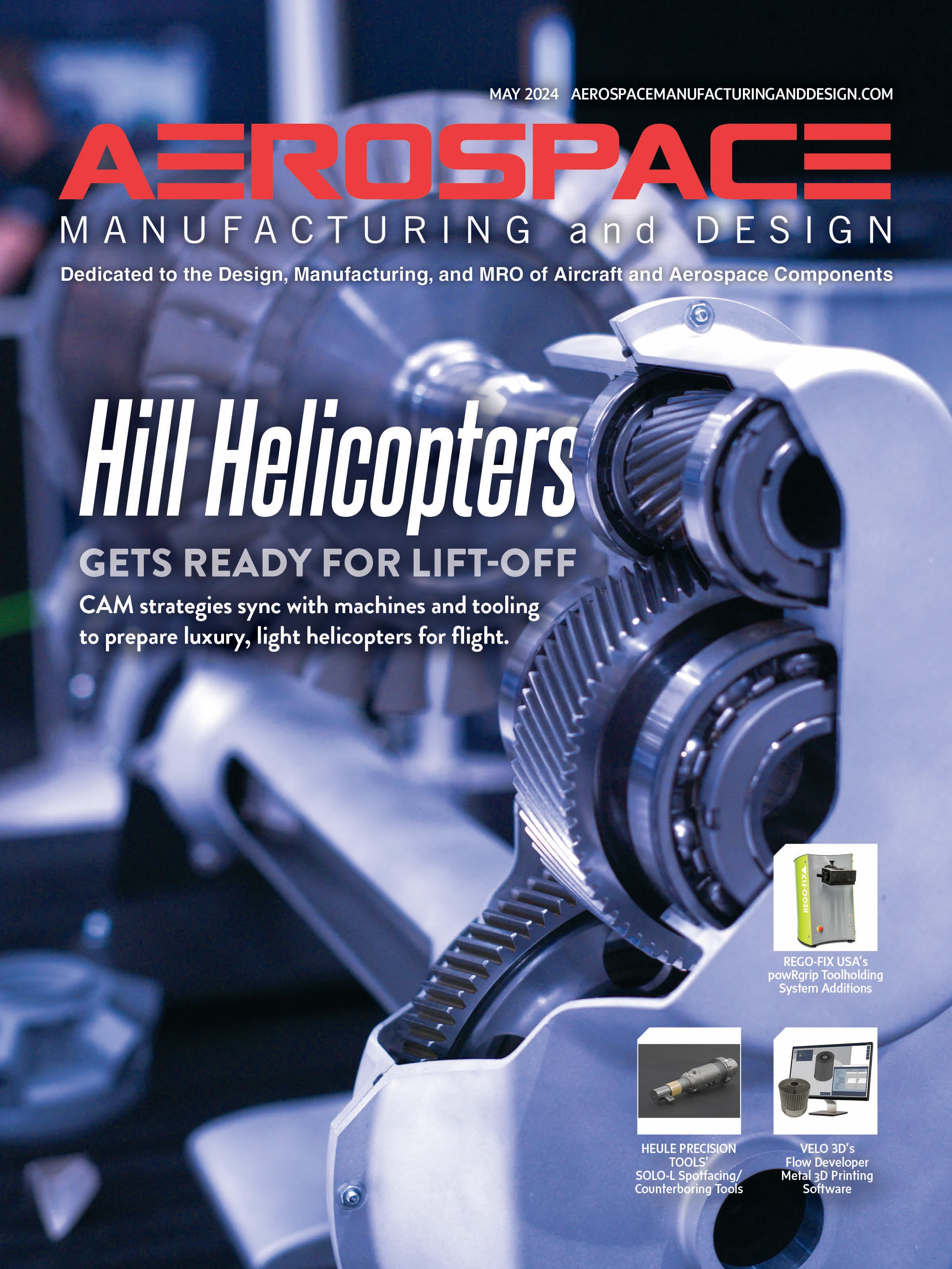
Explore the May 2024 Issue
Check out more from this issue and find your next story to read.
Latest from Aerospace Manufacturing and Design
- GKN Aerospace accelerates additive fabrication for fan case mount ring
- Expanded offering of internal coolant live tools
- #47 Lunch + Learn Podcast with INSACO
- Doncasters’ Groton expansion reaches major milestone
- Hardware-encrypted drive with trusted supply chain
- Titanium drop bottom furnace installation underway
- Solid carbide taps for demanding materials
- The Partner Companies acquires Precision Eforming