_fmt.jpg)
As one of the largest contributors to global CO2 emissions, there’s pressure on the aerospace industry to provide greener aircraft that are lighter and can travel for longer distances. However, achieving this requires working with tough-to-machine aluminum and heat-resistant super alloys (HRSAs). Aerospace original equipment manufacturers (OEMs) can adopt advanced tooling solutions to sustainably machine these tough components.
According to the World Economic Forum (WEF), “Achieving net-zero CO2 emissions by 2050 will not only help create an environmentally sustainable future, but also ensure a financially resilient and competitive aviation industry as a whole.” However, while e-mobility has become increasingly established in automotive – and August 2021 saw electric vehicle (EV) sales overtake sales of diesel in the UK – these developments will take longer to materialize in aerospace.
Generally, electrified aircraft aren’t expected to reach widespread use until 2035. Lonely Planet reports easyJet hopes to run electric planes on routes under 311 miles (500km) by 2030 and Norway aims to make all short-haul flights electric by 2040 but “We won’t be flying long-haul on rechargeable jumbos any time soon: the batteries are simply too heavy.”
While batteries need to become lighter, there’s also a growing onus on OEMs to manufacture lighter components to counterbalance the problem. We can be sure aluminum – specifically, new types with greater strength, fatigue resistance, and other attributes – will be used to make systems lighter.
We’re also seeing an increased use of new HRSAs, already used in aircraft parts facing extreme performance demands because they retain hardness when facing intense heat. These materials properties will prove essential, as one approach to more sustainable air travel will be to burn the engines harder and hotter.
_fmt.jpg)
Components must also be produced to tighter tolerances and more varied designs. As with EVs, tomorrow’s electrified aircraft designs – including the airframes and the engines – will vary more from manufacturer to manufacturer than existing internal combustion-engine craft. For the airframe, some OEMs are exploring delta shape, blended wing body, and strut braced wing concepts. Other OEMs are sticking to traditional big tube, wings, and engine designs.
There’ll also be different forms of engine architecture such as electrified, battery-driven, electromagnetic, or hybrid engines, where current engines are assisted by electric power motors. OEMs will be required to produce an increasing variety of components to tight tolerances while also finding new ways to reduce noise, weight, and emissions – influencing how electric systems perform. But aluminum and HRSA components are difficult to machine, so achieving this sustainably and cost-effectively will be a challenge.
Rapid progress
One path to producing lighter, more fuel-efficient aircraft is through additive manufacturing (AM) techniques. AM allows the development of very complex-shaped customized parts and functional products to tight-tolerances, so difficult-to-machine lattices can be easily machined. According to findings by Dassault Systèmes, “in the aerospace sector, weight reduction from AM processes can result in energy savings of up to 25%,” while “each kilogram (2.2 lb) of weight loss on a flight can save up to $3,000 in fuel annually.”
But is AM manufacturing itself sustainable? A study co-authored by the Department of Manufacturing Engineering at Romania’s Technical University of Cluj-Napoca, describes AM is “a great alternative to traditional manufacturing (TM) methods like injection molding, die-casting, or machining,” and “AM has the potential to lower costs and to be more energy-efficient than conventional processes.”
AM will also have an effect on how products are manufactured. Advantages can include reduced carbon emissions, less material usage, and less transportation because parts can be made in-house instead of imported.
Manufacturers can also produce more complex, compact, and innovative aerospace parts through rapid prototyping; while referring to several different techniques, the goal is to quickly produce a tangible 3D prototype from a computer aided design (CAD) file. With these prototypes, small-volume trials of new materials can be performed before full-scale manufacturing to ensure components are made with innovation, quality, and precision.
Aerospace OEMs can adopt new methods to produce more complex components, but what about having the right tools for the job – particularly when machining tough aluminum and HRSAs?

These materials require cutting tools with higher wear resistance and longer tool life. Sandvik Coromant developed the S205 grade for steel inserts used in turning. Its metallurgy includes an Inveio layer of tightly packed, uni-directional crystals, creating a strong protective barrier around the insert to strengthen the tool and enhance its mechanical properties. The insert has proven useful in manufacturing engine turbine discs, rings, and shafts, with customers reporting 30% to 50% higher cutting speeds using the S205 compared with competing HRSA turning grades.
Holistic approach
We have discussed manufacturing processes and tools, but how can we best combine the two? Time can be wasted putting together a fully integrated solution if the systems aren’t designed to play well together.
Companies such as Sandvik Coromant are supporting customers in aerospace with a components solution. The solution has several stages including looking at the machine requirements and time studies to examine cost-per-component, and analyzing production methods at the run-off, related both to methods-time measurement (MTM) and end-user processes. The components solution also includes computer-aided manufacturing (CAM) programming and project management of local or cross-border projects.
For one customer experiencing chip breaking problems in production, the components solution allowed us to spot the cause and devise a solution. For the customer, Sandvik Coromant’s specialists developed a new strategy with dynamic drive curves allowing us to control the chip breaking in every moment. We called this new approach scoop turning and now have a patent on it. With scoop turning, the customer achieved an 80% cycle time reduction with great chip control and doubled tool life.

The customer reduced its use of four machines down to one, reducing the need for multi-tasking, with more secure machining processes and green light production. Reduced machine usage and complete production runs with fewer tool changeovers – thanks to tougher machining grades such as S205 – will be key to more sustainable aircraft production.
Software will also play a vital role, such as the CoroPlus Tool Guide that’s part of the Sandvik Coromant digital portfolio. Customers can make crucial decisions on the choice of tool and cutting parameters before they commence production.
Close the loop
Aside from new approaches to tools and manufacturing, aerospace OEMs can also turn to manufacturing. According to a report by the Air Transport Action Group (ATAG), Kaiser, the company supplying aluminum to Boeing, employs a closed-loop recycling system – one of the largest programs of its kind in the industry. Kaiser estimates around 10 million kilograms of offcut and scrap metal will be reused by the industry annually through the scheme.
At Sandvik Coromant, we’ve initiated a circular system for recycling carbide tools by buying-back customers’ worn-out carbide tools and re-using them to make new ones; most of the raw materials used in our cemented carbide tools come from scrap. We practice sustainable business in an environment of limited resources and minimize excessive waste. By doing this, we’ve found making tools from recycled material requires 70% less energy while CO2 emissions are 40% less.
There’s mounting pressure on the aerospace industry to manufacture greener aircraft that are lighter and travel longer distances. However, with the right processes and tools in place – and a more holistic approach to manufacturing – aerospace OEMs can help establish a greener future for aerospace.
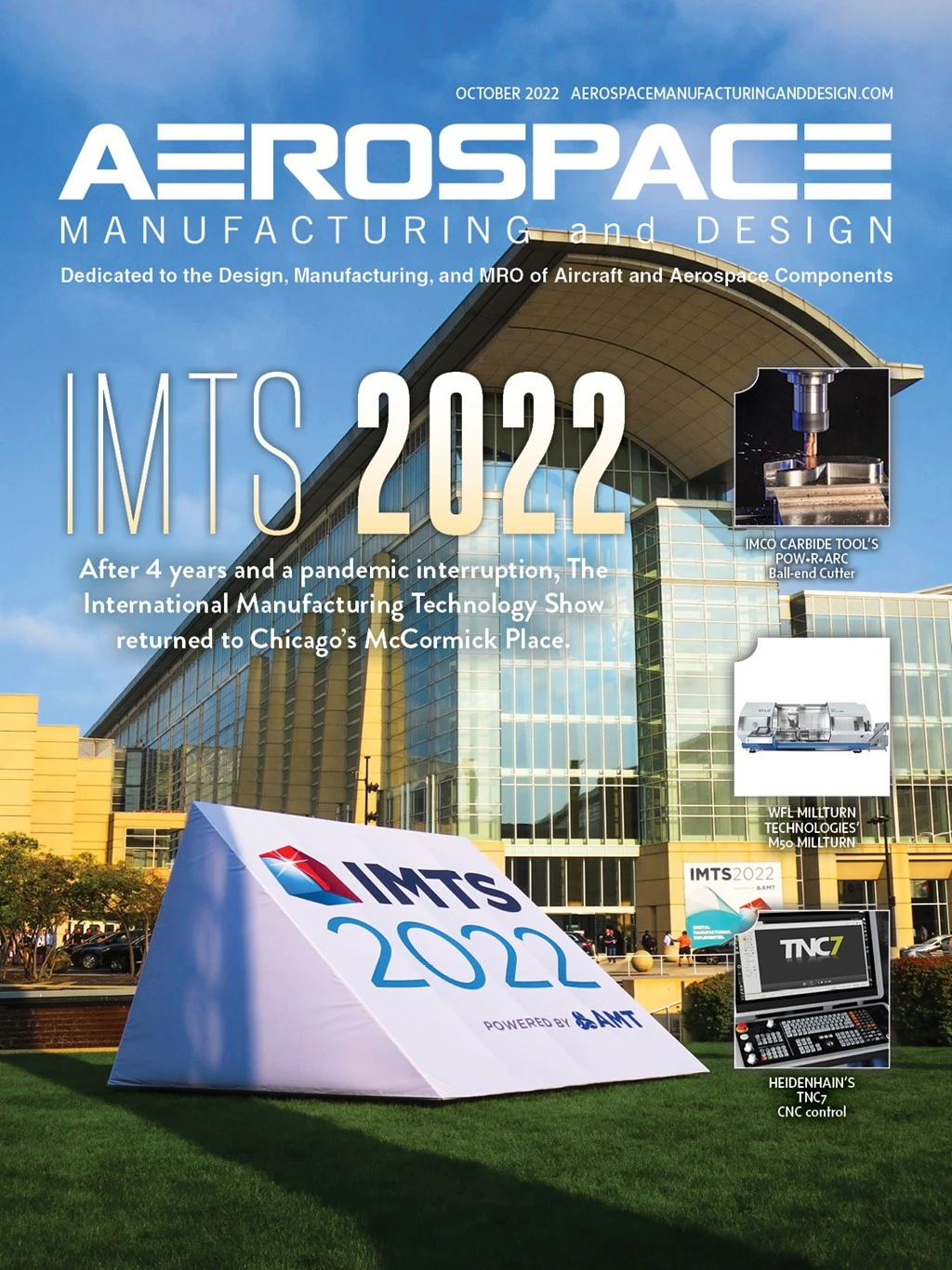
Explore the October 2022 Issue
Check out more from this issue and find your next story to read.
Latest from Aerospace Manufacturing and Design
- Embraer tests wing for new technologies demonstrator
- Mitutoyo America’s SJ-220 portable surface roughness tester
- #55 - Manufacturing Matters - A Primer on Defense Contract Manufacturing
- Registration is open for April’s Manufacturing Lunch + Learn!
- Natilus begins search for new home to build world's most efficient commercial aircraft
- Aerospace Industry Outlook webinar is back by popular demand
- Automation Webinar with Visual Components
- PrecisionX Group expands manufacturing operations