
In metalworking operations, eight common problems sap profitability. The following steps show how to identify those issues and counteract them to maximize growth.
Tooling
Numerous metals are used in manufacturing. Based on their composition, these materials each machine differently. With superalloys, for example, end mills and inserts can burn up if not run properly.
Solution: Select the proper cutting tool for each material. Choosing the most appropriate cutting tool for the material being machined can save metalworking shops up to 15% on overall costs and improve machining productivity by 20%.
Cutting fluids
When not managed properly, cutting fluids are costly expenses. Metalworking fluids make up as much as 10% of the cost of a finished part, and large volumes of waste coolant are expensive to handle and haul away. Outdated, inefficient fluid recycling systems are also problematic.
Most applications use a water-miscible fluid, but oil-based coolants are the best option in precision machining applications. However, oil-based coolant residue can get inside machines and stain parts that need to be cleaned.
Solution: Recycling cutting fluids in-house is easy and can save metalworking operations thousands of dollars per year on new cutting fluid purchases. In-house fluid recycling systems provide machines with a consistent source of clean fluid in the proper concentration. Turnkey in-house fluid recycling systems:
- Increase tool life up to 25%
- Reduce haul-away costs up to 90%
- Lower new coolant purchases up to 75%
If choosing oil-based coolant, consider switching to a synthetic coolant if the application isn’t in precision machining. Synthetic coolants have excellent cooling properties that provide long life in the sump, reducing maintenance and waste. Also, synthetic coolants don’t contain mineral oil so parts come off the machine cleaner, and as a result, don’t require washing and blow-off.

Setup, fixturing
Setup time and fixturing are often a major source of lost productivity in metalworking. It’s not uncommon for half of setup time to be wasted.
Solution: Milling and turning applications can use precise quick-change fixturing with high repeatability and accuracy by making some changes to setup and fixturing procedures. First, pursue quick-change tooling that allows operators to switch out tooling via a quick-release screw, significantly lowering setup time.
For fixturing, a workholding vise enables quick change-outs and minimizes downtime. Also, having multiple fixtures nearby and ready to use saves time, making part switches quick and easy when the machine cycle is complete.
Technology, innovation
Technology is constantly changing. Metalworking operations that don’t stay abreast of the latest innovations may lose their competitive advantage.
Solution: New developments pop up every day in machines and tooling that are better solutions for productivity. Using integrated tools to expand functionality is a way to drive efficiency. For example, using a tool for a 5-axis machine that drills, countersinks, and chamfers (instead of three separate tools) reduces the number of individual tools needed.
Metal removal rate
Two aspects of metalworking processes – lackluster metal removal rate (MRR) and manual processes – can significantly drive down production.
Solution: Changing metalworking processes to a higher MRR can positively impact an operation’s revenue. By using the correct toolpaths, depth of cuts, speed, carbide grades, and geometries, MRR can improve productivity.
Improving production in deburring can be done by changing from a manual process to a deburring wheel.
Programming
An improperly programmed machine can create unneeded operational steps, contributing to overtime and weaker production rates. Further, outdated control systems and programming cause many shop inefficiencies, such as low productivity and high maintenance costs.
Solution: Updating or replacing outdated control systems and/or hiring a reputable and knowledgeable automation company with industry specific experience for programming can significantly increase a shop’s efficiency. Updating machine programming or adding automation to current operations:
- Reduces time to market
- Improves quality
- Enhances workplace safety
- Increases output
- Reduces labor
By remotely monitoring equipment, real-time data can be used to proactively adjust maintenance programs and production schedules. KMC Global Controls & Automation, based in Kalamazoo, Michigan, works with manufacturers to program their machines to reduce labor costs. Features such as maintenance reminders, interactive fault screen controls, user-friendly human-machine interface (HMI) screens, and cloud-based machine monitoring that identifies machine energy wasters that can be shut off when they are not being used, help operators get the most out of their metalworking equipment.

Energy waste
Operations running when they aren’t needed are a primary source of energy waste. Pumps, blowers, conveyor motors, blending, and vessel agitation are a few examples of equipment and processes that are left to run for long periods of time even when product or materials are not being produced. And large power consumers are not the only culprits – wasted energy from small motors will add up through time. For example, a 2hp motor will draw about 1,500W/hour. Running that motor for one day will use 36,000W (3.6kW) of energy.
Solution: Increase energy efficiency and lower costs in four ways:
- Replace large motors with lower horsepower motors that match power to the application’s need
- Employ speed- and load-altering devices to efficiently manage material delivery from one process to another
- Operate motors when needed. Test motors during the initial start by running them briefly, then, pause the motors until product arrives
- Use cloud-based machine monitoring systems that can identify machine energy wasters that could be shut off during periods of inactivity
Metal scrap management
Manually handling and/or failing to process metal scrap in-house before it is sent to the scrap dealer is a considerable source of inefficiency and lost revenue. Ineffectively processed metal scrap takes up valuable space and takes operators away from production. It also accrues high haul-away costs and yields reduced prices from scrap dealers.
Solution: Metal scrap processing equipment reduces large piles of turnings to small chips and separates the chips from fluid. Because the pile of metal scrap is reduced to small chips, a larger payload can be sent to the scrap dealer, who will typically offer a higher price per pound for dry chips.
Processing equipment that creates efficiencies or increases the value of metal scrap includes:
- Scrap metal conveyance systems: Automate moving of scrap from the point of generation to processing equipment and then to recycling containers; conveyors significantly reduce operator interaction with scrap material and decrease forklift traffic, improving safety
- Crushers, shredders: This equipment turns large piles of turnings into shovel-size pieces
- Wringers/centrifuges: Separate chips from cutting fluids to create dry chips and collect spent fluid
- Briquetters: Compress wet chips into dry compact pucks that are easy to re-melt, transport, and store

Conclusion
Metalworking operations can maximize profits by focusing on these eight problem areas. Prioritize the problems based on the ones that will produce the greatest cost savings and then systematically address the problems, one at a time.
Get curated news on YOUR industry.
Enter your email to receive our newsletters.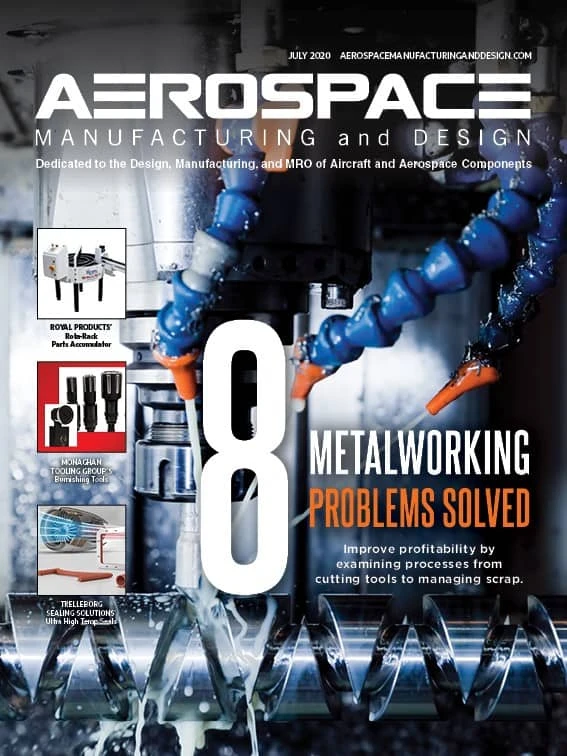
Explore the July 2020 Issue
Check out more from this issue and find your next story to read.
Latest from Aerospace Manufacturing and Design
- Ralliant to establish global headquarters in North Carolina
- Philatron MIL-DTL-3432 military cables
- Beyond Aero refines its hydrogen-electric light jet
- Americase's advanced protective solutions
- Social media - what are your thoughts
- GE Aerospace secures Air Force engine contract
- Thomson Industries' online sizing and selection tool
- #53 - Manufacturing Matters - 2024 Leaders in Manufacturing Roundtable