
When used correctly, probing can have significant cost, efficiency, and quality benefits. Probing is often underutilized because operators are not familiar with best practices. The following tips are intended to help operators use probes to make machining processes more precise and efficient.
1. Clean the surfaces you are measuring. This is important for calibration and part measurement. Dirty surfaces will produce false readings affecting calibration offsets and subsequent part measurements. A clean surface ensures accurate measurement results and better part quality.
2. Maintain probe quality and geometry. Is the stylus assembly tight? Does it look out of square? Was the probe dropped or hit? Any of these will cause measurements to be off. Treat your probe with the same care as any other precision measuring device.
3. Calibrate the probe regularly to maintain accuracy. Calibration is performed using an artifact (a standard of known, measured size). If you do not have an artifact such as a calibration sphere, a qualified feature on the machine, tool, or fixture can also be used. It’s not unusual to get different values when different operators measure the same feature. The quality of the data input determines the calibration of the probe and part precision.
4. Use an artifact or calibration gauge as close to the part or feature size as possible. This will yield the most accurate calibration. For example, if the part to be measured is 20" in diameter, try to use an artifact that is close to that size. It helps to maintain the aspect ratio as close as possible.

5. When probing, make sure the stylus tip, not probe shank, contacts the part.
6. Verify the accuracy of your work offsets or measurement reference as this establishes the basis for measurement of feature location. If the measurement reference is not accurate, the probe measurements will be skewed. An inaccurate part setup, affects probing results.
7. If the probe does not have automatic shut off, turn it off to save the battery life. The next operator will thank you.
In addition to setup benefits, probing’s in-process advantages include the automated measurement and updating of tool offsets. The alternatives to probing during setup – touching off with a tool, using an edge finder, or manual measurements – are all less precise and more time consuming. Probes reduce cycle time and the opportunity for human error (and resulting scrap), while improving part quality.
Fives Group
About the author: Dan Silberhorn is manufacturing engineer, programming at Fives Giddings & Lewis .
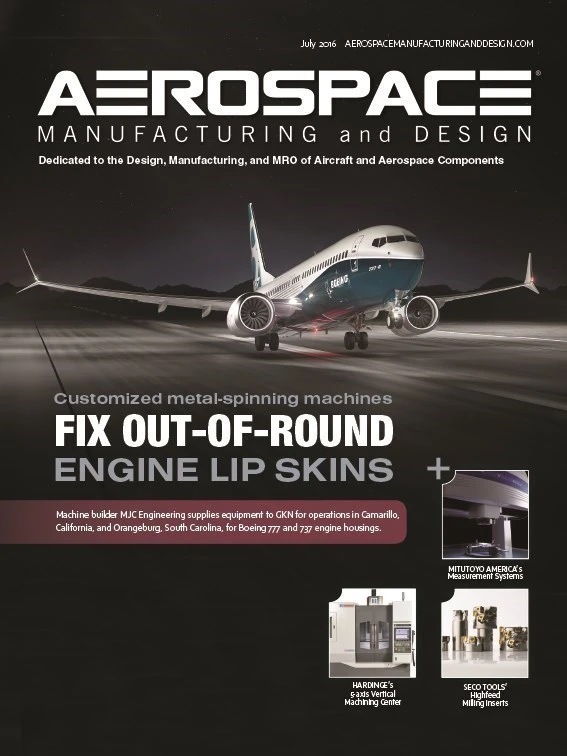
Explore the July 2016 Issue
Check out more from this issue and find your next story to read.
Latest from Aerospace Manufacturing and Design
- Revitalizing the Defense Maritime Industrial Base with Blue Forge Alliance
- Safran Defense & Space opens US defense HQ
- Two miniature absolute encoders join US Digital’s lineup
- Lockheed Martin completes Orion for Artemis II
- Cylinder CMMs for complex symmetrical workpieces
- University of Oklahoma research fuels UAS development
- Motorized vision measuring system
- Everyone's talking tariffs