

Minimizing the time and frequency of setups on CNC grinding machines is key to enhancing productivity. The strategies are applicable across various CNC grinding machines, but the annual savings estimates below are specific to CNC tool grinding.
A standardized approach also aligns with lean manufacturing principles. Process discipline, daily accountability, and visual management can be integrated into production, supporting continuous improvement.
1. Maintain precise machine calibration, including onboard in-process gaging and measuring devices. An inaccurately calibrated machine wastes time and materials, requiring more blanks to produce the first acceptable part.
2. Use precision wheel arbors and wheel bodies, with grinding wheels featuring a hole tolerance of H5 (-0/+0.0004"). It’s equally important to dress and preset the grinding wheel on the designated wheel arbor for the machine, without switching between arbors.
3. Ensure precision wheel dressing, as any run-out means only one-third of the wheel’s periphery is effectively grinding. Many operators opt to dress a small, predefined, and programmable corner radius to increase corner durability, minimizing the need for frequent adjustments until the wear naturally stabilizes.
4. Maintain precise wheel balancing, with a typical balance class of G2.5, which corresponds to a residual imbalance of approximately 2.5g.mm/kg at 10,000rpm.
5. Accurate wheel pre-setting (measurement) is crucial, ensuring the presetter precisely captures the corner radius and any other dimensions on the wheels.
6. Use precision grinding software with robust tool design capabilities. The software should accurately integrate the corner radius into calculations and support detailed 3D simulations and machine animations for enhanced precision.
7. Ensure thermo-stable, high-precision coolant oil delivery. All grinding spindle motors should feature internal oil cooling, and a high-accuracy coolant chiller is recommended to maintain a consistent temperature, even as oil volume fluctuates when other machines on the line are powered on or off.
Here are examples of potential annual savings per CNC tool grinding machine, based on a setup time reduction from 52 minutes to 45 minutes and a reduction of blank waste by 2 pieces per setup:
Lot size | Annual savings, 7 minute cycle time | Annual savings, 15 minute cycle time |
---|---|---|
150 | $6,090 | $3,890 |
50 | $15,330 | $10,440 |
15 | $38,990 | $29,970 |
Estimated annual savings are based on assumptions regarding the number of operators, machine up time, hourly shop rate, and wheel costs.
Implementing these strategies can greatly reduce the required number of setups, boosting efficiency and throughput while elevating overall grinding quality.
MyGrinding Inc.
https://www.mygrinding.com
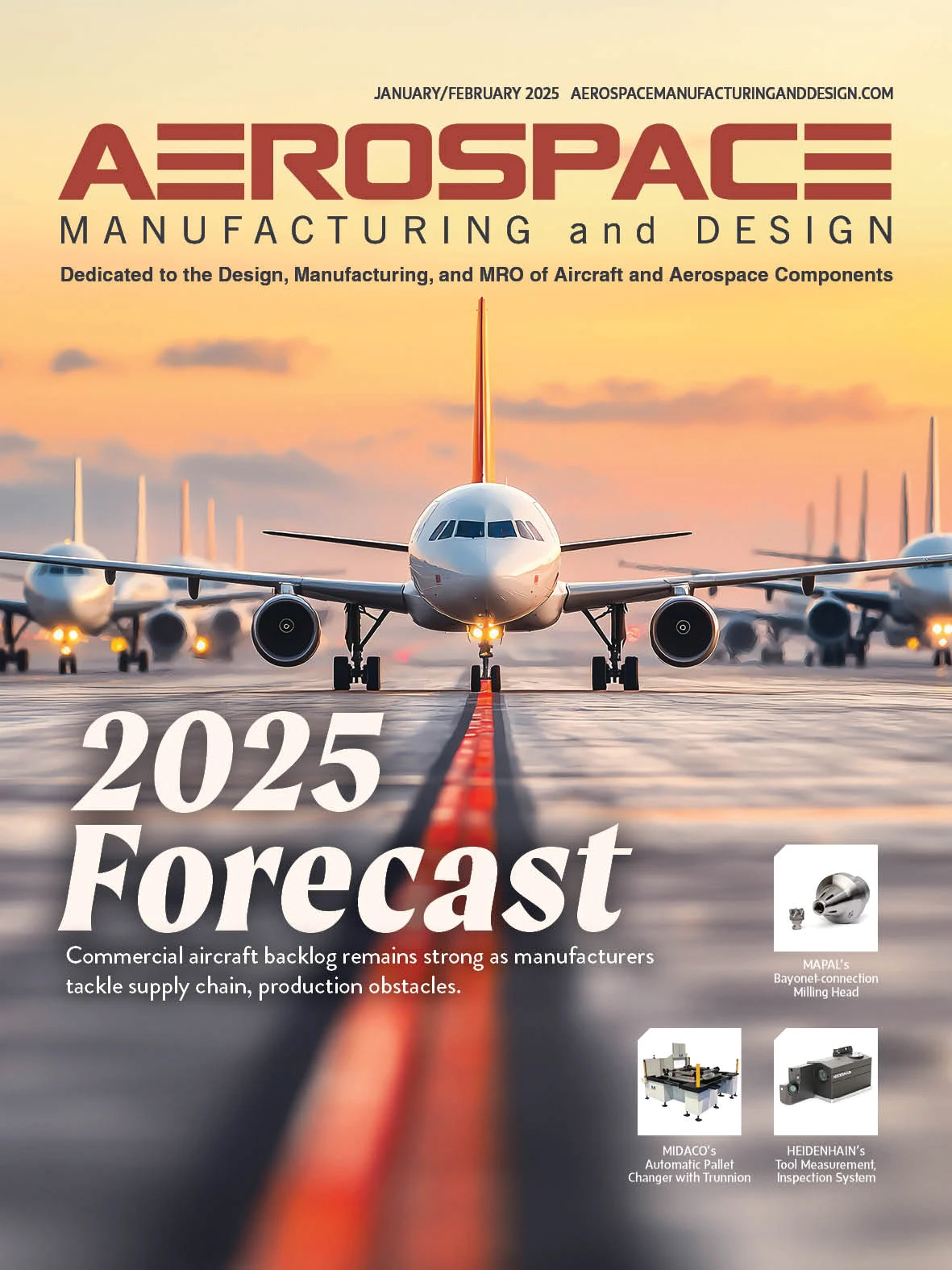
Explore the January/February 2025 Issue
Check out more from this issue and find your next story to read.
Latest from Aerospace Manufacturing and Design
- Airbus to acquire assets relating to its aircraft production from Spirit AeroSystems
- FANUC America's Cobot and Go web tool
- Chicago Innovation Days 2025: Shaping the future of manufacturing
- High-density DC/DC converters for mission-critical applications
- #59 - Manufacturing Matters: Additive manufacturing trends, innovations
- ACE at 150: A legacy of innovation and industry leadership
- Free webinar to offer expert advice on optimizing machining operations
- How collaboration between companies can elevate manufacturing