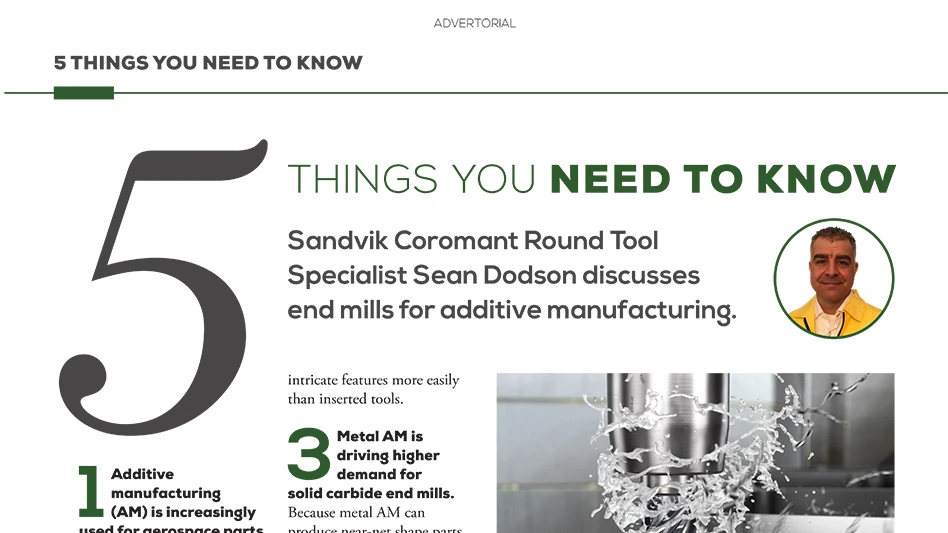
GIE Media

1) Additive manufacturing (AM) is increasingly used for aerospace parts.
Aerospace engines are currently the main application for (AM) parts. However, we are starting to see more interest from the airframers as well. Some formerly cast parts are now candidates for AM. Titanium, Inconel, stainless-steel, and other heat resistant super alloys (HRSAs) long used in aerospace are now able to be used in AM. And parts designed for AM that combine features of several, separate parts onto a single piece are becoming more common.
2) Additively manufactured metal parts are challenging to machine.

AM’s ability to produce more complex shapes – and use of hard materials – make them challenging to machine with traditional tools. The complicated shapes AM can create makes it difficult to apply inserted tools because of space constraints or the need for complicated tool paths not encountered in machining solid billets. Solid tools can reach intricate features more easily than inserted tools.
3) Metal AM is driving higher demand for solid carbide end mills.
Because metal AM can produce near-net shape parts, there is less need for heavy roughing to achieve the desired finished part. Solid carbide end mills fit perfectly with additively manufactured parts because of their longer lengths of cut, up to 5x the diameter. Solid carbide tools designed for high-feed side milling, such as Sandvik Coromant’s CoroMill Plura line, are offered in grades and geometries to match AM materials and shapes.
4) Proper tool path can increase tool life, improve productivity.
Tool path has a large impact on overall productivity and cost per part. Many CAM software providers now offer tool paths optimized for AM. Better tool paths maintain consistent cutting forces, offer improved metal removal rate (MRR), produce better part finish, and provide longer tool life. With less material to remove from near-net shape parts, less radial contact with deeper passes from a well-designed tool path makes machining more productive and saves time. Plus, lighter roughing allows use of smaller spindle, smaller horsepower machining centers, which reduces energy use.

5) Solid carbide end mills offer advantages in machining additively manufactured parts.
The long length-of-cut capabilities of solid carbide end mills require fewer axial passes to achieve a finished part compared to a similar diameter inserted tool. Although the initial cost can be higher than inserted tools, solid carbide end mills can be more effective, with higher MRR using more efficient tool paths, and the tooling can be reconditioned, reducing overall tool cost.
Get curated news on YOUR industry.
Enter your email to receive our newsletters.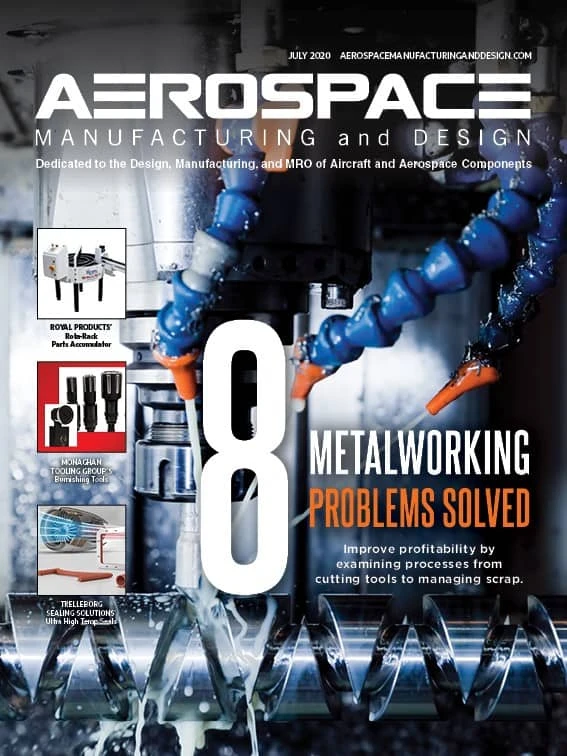
Explore the July 2020 Issue
Check out more from this issue and find your next story to read.
Latest from Aerospace Manufacturing and Design
- Ralliant to establish global headquarters in North Carolina
- Philatron MIL-DTL-3432 military cables
- Beyond Aero refines its hydrogen-electric light jet
- Americase's advanced protective solutions
- Social media - what are your thoughts
- GE Aerospace secures Air Force engine contract
- Thomson Industries' online sizing and selection tool
- #53 - Manufacturing Matters - 2024 Leaders in Manufacturing Roundtable