
GIE Media

Aerospace frame components are complex and must meet demanding specifications. Our goal at Sandvik Coromant is to offer complete solutions, like our wide range of competitive tooling solutions for aerospace frame assembly and processing knowledge that helps you excel.
1 Put dynamic milling to work in your programming
Consider the best tool path for the application. Avoid dramatically reduced tool life by programming a clockwise roll-into-cut. Keep the cutter constantly engaged; program around interruptions and holes when possible. In 3- and 5-axis machining, minimize tool wear and maximize material removal by using dynamic milling toolpaths for an overall stable process. Use Mastercam’s Dynamic Milling or NX adaptive milling toolpaths when machining pockets to efficiently remove material.
2 Improve stability and security to achieve high precision specifications
_fmt.jpg)
Make improving rigidity and stability a top priority. When machining frame components, vibration risk is high, and the cure tends to be slow machining or dampened tools. A more productive solution is Silent Tools™, a unique range of long-reach cutting tools and adaptors for turning, milling, and boring, with a damping system inside the tool body to minimize vibration. The benefits: productivity gains of at least 50% for the shortest adapter lengths and up to 300% for longer adapters. Use CoroChuck® 930, which offers the best pull-out security on the market and reduces vibrations for excellent stability and accessibility in all milling and drilling operations.
3 Achieve optimal metal removal in high feed pocket milling with CoroMill® MH20
Maintaining high metal removal rates is critical, especially in pocket and deep cavity milling. The new CoroMill® MH20 for high feed pocket milling offers geometries for the highest metal removal rates in stable applications. With a strong radius for higher security around the corner, the versatile solution delivers optimized edge-line security for reliable corner machining and pocket milling in unsupervised machining.
4 Understand what plunge milling can mean to your operations

When side milling isn’t possible due to vibrations, plunge milling is effective for roughing-out cavities. It makes a deeper hole through repeated axial cuts, requiring lower feed per tooth. Consider plunge milling when tool overhang is greater than 4x DC, stability is poor, and when semi-finishing corners or working in difficult- to-cut material like titanium. Developed for plunge milling in HRSAs, the CoroMill® Plura Gannet solid carbide end mill offers robust geometry designed for plunging with long overhangs. Equipped with coolant grooves on shank, CoroMill® Plura Gannet facilitates safe chip evacuation.
5 Machine aluminum alloys with thin-wall machining techniques
A vital element of good machinability is to achieve low cutting forces, allowing for low power consumption, less vibration, and a good quality surface finish. Leverage a solution offering high-speed stability and excellent metal removal rates like the RAL90 aluminum milling cutter to machine challenging aero structure components made of aluminum and aluminum alloys. Get the stability you need for aluminum machining with the CoroMill® Dura range of inch solid carbide end mills using patented WhisperKut technology to significantly reduce chatter.

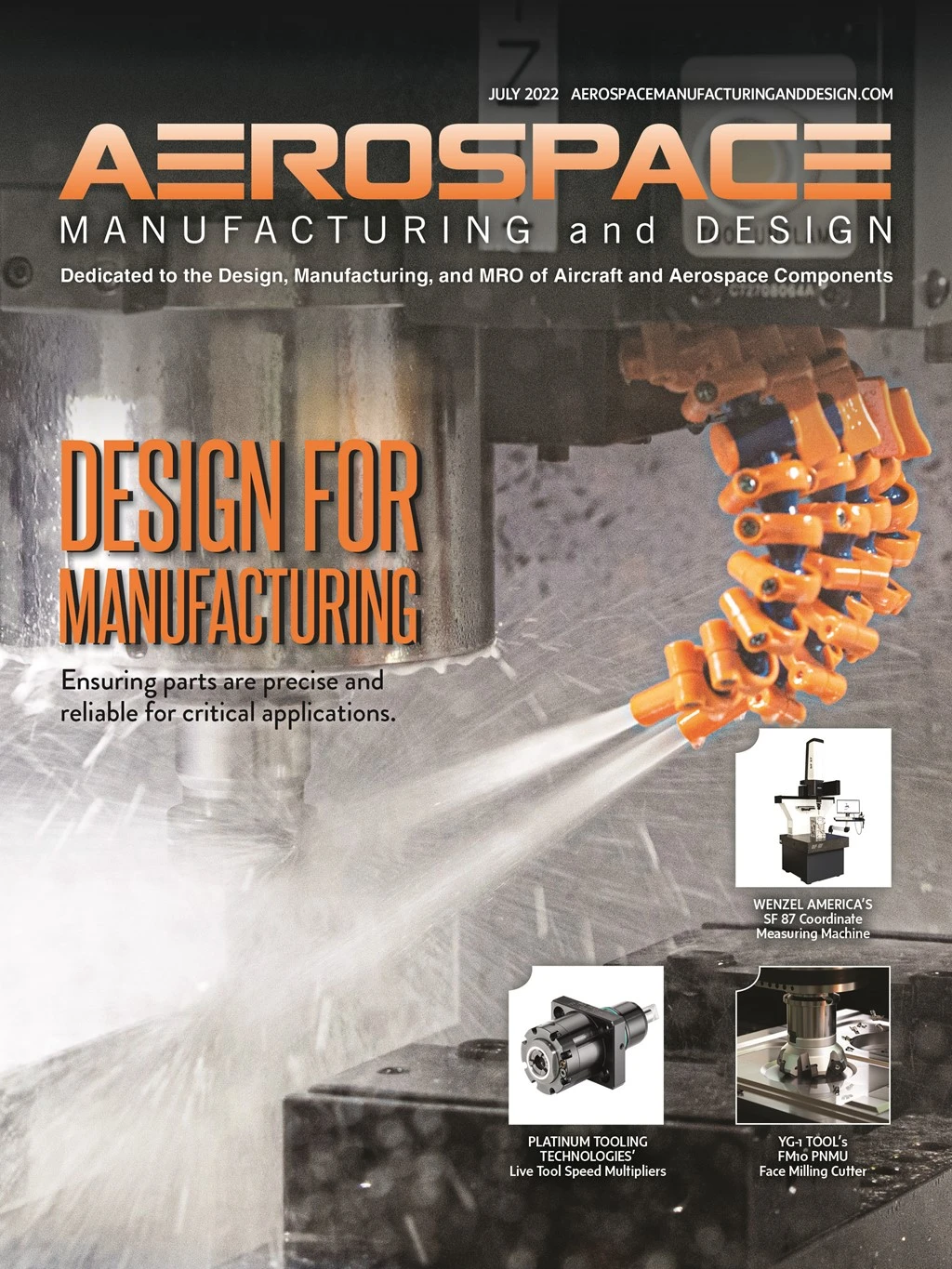
Explore the July 2022 Issue
Check out more from this issue and find your next story to read.
Latest from Aerospace Manufacturing and Design
- Archer Aviation, Palantir partner on next-gen aviation
- Fairlane Products’ TG GripSerts and accessories for low-profile clamping
- Boeing to build US Air Force’s sixth-generation fighter jet
- Sandvik Coromant introduces CoroMill Plura barrel
- #54 - Manufacturing Matters - HMI Solutions for EV Industry from EAO
- Aerospace Industry Outlook returns for spring 2025
- Drop in for an interactive webinar on automation in manufacturing
- SW’s wing rib technology for the aerospace industry