

1. Technical ceramics
such as alumina, zirconia, and sapphire can significantly improve the performance of components subjected to extreme conditions, especially in aerospace and defense applications. This becomes extremely valuable when other materials such as metals and polymers are susceptible to fatigue/failure and not warranted in complex applications. The advantage to using technical ceramics in aerospace/defense applications is most recognizable when needed for high temperature environments. Sapphire can be advantageous for lenses and windows exposed to abrasive, harsh environments as they offer superior scratch resistance. Sapphire also transmits infrared (IR) even at high temperatures.
2. High precision machining
is often required when trying to hold tight tolerances for special aerospace/defense applications. As a specialist in this field, INSACO has the ability to hold various geometries to an extremely fine precision, that would otherwise not be feasible through green machining or isostatic pressing alone.
3. Diamond grinding.
While metals are typically machined through some form of cutting or single point turning, this conventional machining method does not work on hard ceramic materials. In most instances, the ceramic material itself is harder than the cutting tool used to machine it, thus preventing adequate material removal. To overcome this obstacle, diamond grinding is utilized. Overall, diamond grinding is a highly precise and efficient method for machining hard materials like ceramics. The use of diamond particles in the grinding wheel allows for tight tolerances, intricate features, and extended tool life.

4. Accuracy and tolerances.
With the philosophy “if you can’t measure it, you can’t make it,” Insaco has evolved an elaborate quality control (QC) program with best-in-class contact and non-contact instruments which frequently verify tolerances as tight as 0.000039". This capability assures proper measuring and document processes, which verifies that a part is made to print or it does not ship.
5. Technical aerospace, defense, and semiconductor applications.
Since 1947, INSACO’s management has committed to continuous capital upgrades to facilities, cutting edge equipment, and the expertise to work with this equipment. These upgrades enhance dependability, improve machining capability, consistently achieve tighter tolerances, and increase capacity to meet customer demands. INSACO will take an unbiased approach to material selection, and will offer guidance on the most optimal material for each specific end use application. The emphasis on hiring top-level machinists is to ensure the capability of delivering parts as promised. INSACO engineers are available to discuss design considerations and review drawings for machinability as well as highlight cost driving details before a design is finalized.

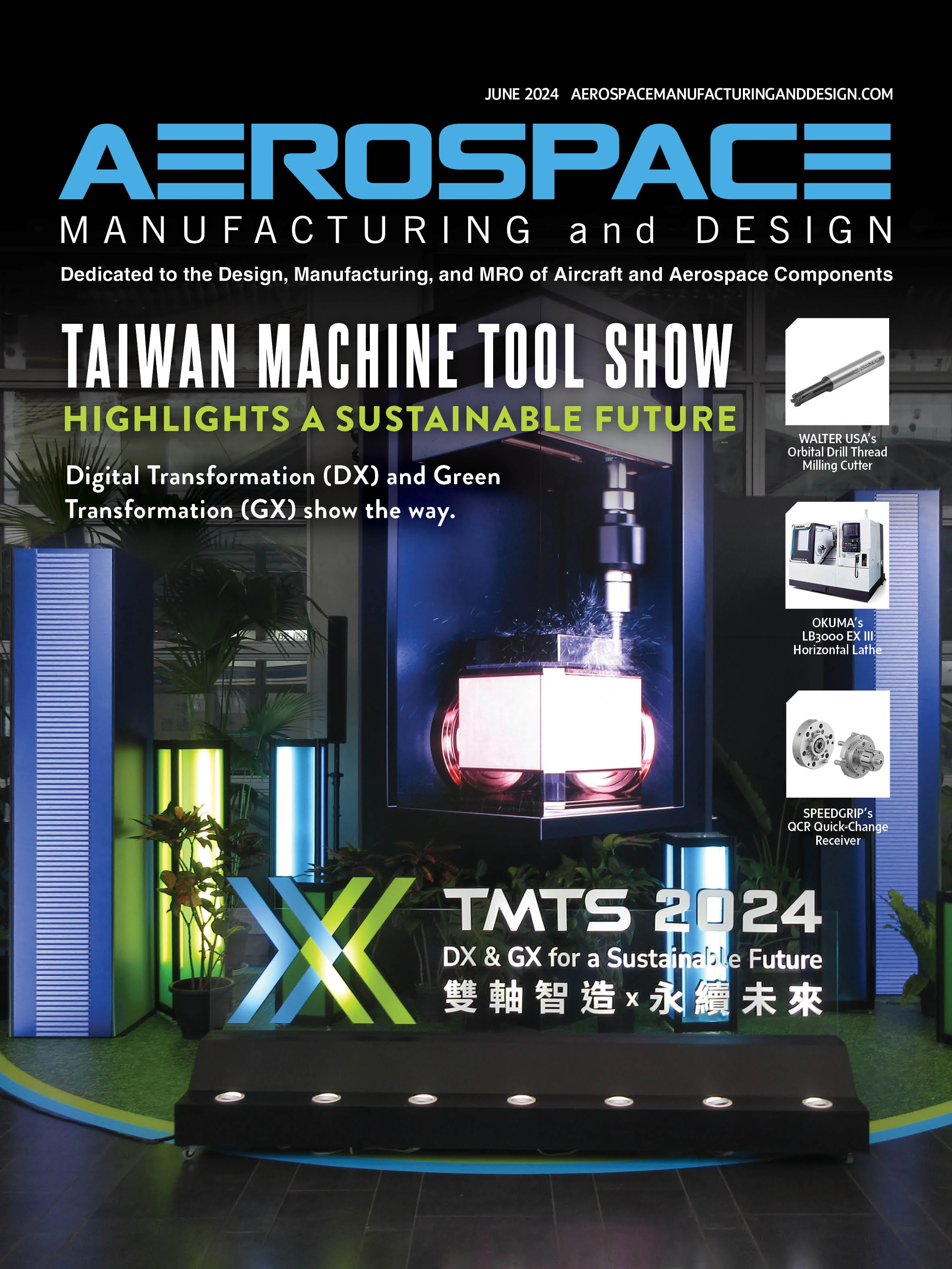
Explore the June 2024 Issue
Check out more from this issue and find your next story to read.
Latest from Aerospace Manufacturing and Design
- Airbus to acquire assets relating to its aircraft production from Spirit AeroSystems
- FANUC America's Cobot and Go web tool
- Chicago Innovation Days 2025: Shaping the future of manufacturing
- High-density DC/DC converters for mission-critical applications
- #59 - Manufacturing Matters: Additive manufacturing trends, innovations
- ACE at 150: A legacy of innovation and industry leadership
- Free webinar to offer expert advice on optimizing machining operations
- How collaboration between companies can elevate manufacturing