
Titanium and high-nickel alloys burn through inserts and cutting tools like no other materials, especially during roughing operations. These materials are abrasive and tend toward work hardening at high temperatures. As a result, expensive tools and inserts are often changed out more frequently, simply as a precaution to protect high-value components.
1. Choosing the right fluid is just as important as choosing the right tools, cutting parameters, and CNC machine. Coolant is an often-overlooked part of this decision-making process, yet it has a significant impact on critical operations such as surface finishes and geometric tolerances. By making informed and data-driven decisions around coolant, you can achieve measurable improvements and savings in material removal rates, tool life, sump life, and part quality.
2. The Skytec family of products was developed by a team of experts including chemists, engineers, and application technicians, and tested by well-known machine tool builders and aerospace original equipment manufacturers (OEMs). These are ideal metalworking fluids for titanium because they minimize tool wear and reduce the number of tool changes without compromising process reliability. They are also suitable when machining aluminum, steel, and nickel-based alloys. The fluids perform without foam even in high-pressure systems greater than 1,000psi.
3. The easiest time to introduce a new fluid is during a new product introduction, but this decision isn’t always a central part of the planning process. If you have a new product in the pipeline, look at your current situation and consider the age of the coolant formulas currently in use. Every year there are product improvements and new formulas that can truly add value to the production process.
4. If OEM approvals are needed, the key is to have the discussion with the supplier quality team (SQE, SQA, etc.) early on. Requirements aren’t standard across the OEMs. Invite your coolant supplier to support you through this process. At Blaser, we have extensive experience with major manufacturers and understand how to complete necessary qualification testing. Aerospace industry approvals can be difficult, but they’re much easier at the time of a new product launch when it’s part of a comprehensive strategy. Understand the requirements, collaborate, and make it part of your plan from the start.
5. There’s no one-size-fits-all solution. Decisions about production strategies should be data-driven and based on your unique situation. Blaser supports customers with people, products, and services, not just metalworking fluids. Leverage supplier know-how about water quality, foam control, filtration, product and material compatibility, process optimization, machine cleaning, and fluid monitoring. We can help you find improvement opportunities you may not have known even existed.
More information
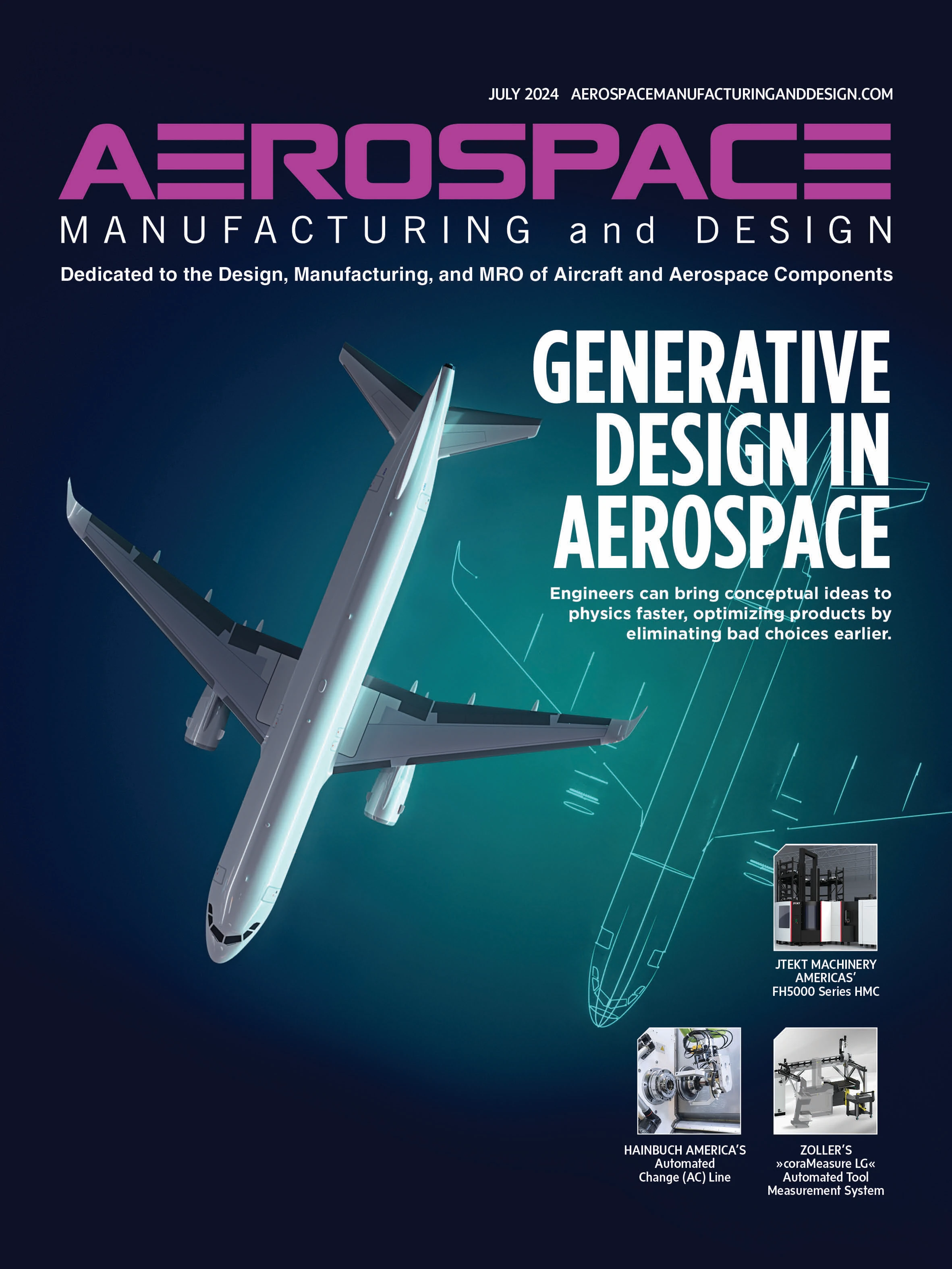
Explore the July 2024 Issue
Check out more from this issue and find your next story to read.
Latest from Aerospace Manufacturing and Design
- Revitalizing the Defense Maritime Industrial Base with Blue Forge Alliance
- Safran Defense & Space opens US defense HQ
- Two miniature absolute encoders join US Digital’s lineup
- Lockheed Martin completes Orion for Artemis II
- Cylinder CMMs for complex symmetrical workpieces
- University of Oklahoma research fuels UAS development
- Motorized vision measuring system
- Everyone's talking tariffs