
GIE Media

1 What are the advantages of using flat bottom drills?
Using a flat bottom drill allows you to perform a range of drilling operations on a range of surfaces. That means you can drill (on flat, angled, contoured, or partial surfaces), counterbore, true existing holes, clear material left by a conventional drill point, or dish from an endmill. Another advantage common with flat bottom drills is they tend to leave a smaller burr on exit of a through hole.
2 How does a flat bottom drill produce a smaller burr?
The forces a drill puts into a workpiece are perpendicular to the cutting edge, so on a non-flat conventional drill, typically around 140°, the forces are outward. This displaces material in the same direction of the forces and a burr is easily formed as the drill exits. The higher the point angle, the flatter the drill is and the further downward the forces on the workpiece are shifted. A flat bottom drill has a point angle of 180°, which shifts the forces straight down. On exit, the material is pushed and displaced downward, rather than outward, decreasing the likelihood of a burr forming on exit.
3 Can you offer any application tips for using a flat bottom drill?
When on an angle, rates obviously need adjusted, but how you adjust them is critical. Typically, the speed will be reduced by a greater amount than the feed. This heavier chip load allows the drill to stabilize sooner and produce a better hole. Another tip (not only applicable to flat bottom drills) is to slow down the drill on exiting a through-hole if a burr is forming. This puts less force into the workpiece and prevents the bottom of the hole from blowing out from the increased downward force of these drills.
4 When should a flat bottom drill be used?
It depends on the application, but typically the benefits these drills provide are universal. There are cases where the through-coolant version is suggested, such as heat resistant alloys, due to the lack of thermal conductivity. There are also some materials where a flat bottom drill is less ideal, such as composite material that can delaminate on through-holes. The downward force these drills produce can be detrimental to the finished part.
5 What makes KSPT’s flat bottom drills special?
KSPT’s flat bottom drill has a 4-margin design, but the margin spacing, in combination with the unique end work, place the trailing margin in contact with the workpiece sooner than other flat bottom drills. This adds stability, especially when drilling a hole on a difficult surface, producing a straighter, truer hole and increasing tool life. There’s also a through-spindle coolant (3xD & 5xD) version and a non-TSC version (2xD) depending on material being drilled and the depth required.
More information: https://www.kyocera-sgstool.com

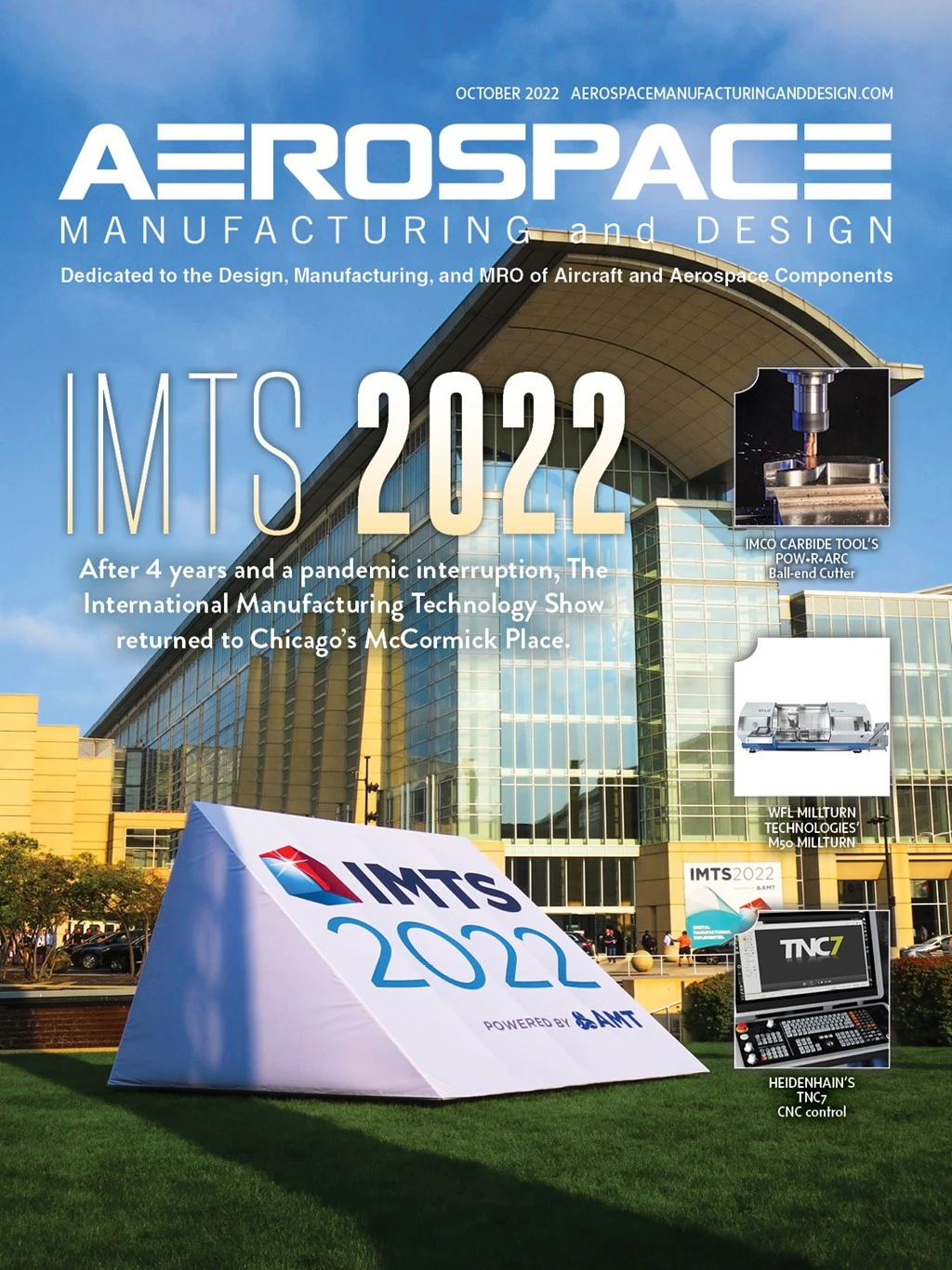
Explore the October 2022 Issue
Check out more from this issue and find your next story to read.
Latest from Aerospace Manufacturing and Design
- Taiwan’s China Airlines orders Boeing 777X passenger, freighter jets
- Reamer re-tipping extends life of legacy tooling
- Revitalizing the Defense Maritime Industrial Base with Blue Forge Alliance
- Safran Defense & Space opens US defense HQ
- Two miniature absolute encoders join US Digital’s lineup
- Lockheed Martin completes Orion for Artemis II
- Cylinder CMMs for complex symmetrical workpieces
- University of Oklahoma research fuels UAS development