
Even with 90+ available metals, many exhibiting diverse properties useful to aerospace engineers, no single metal or alloy consistently satisfies all design requirements. One way around this dilemma? Hermetically bonded dissimilar metals.
1. Design with solid state multi-metal bonds for lasting, reliable connections
While welding, brazing, and adhesives may suffice in less demanding applications, solid state bonds – those created through explosion, diffusion, or roll bonding – hermetically combine the advantages of two or more metals. This creates robust connections suitable for space applications. Bimetal and multi-metal fittings facilitate the use of contrasting and complementary metal properties, offering better performance, lower costs, and easier machinability.
2. Combine different properties in a single machined component
Metallurgically bonded materials can be engineered to exploit varied properties. For example, highly conductive metals bonded to poor thermal conductors control heat transfer. Bonds can also be designed to manage thermal expansion, distortion, or movement during heat cycling or to intentionally use thermal differences to change component shape. Harmonics can be managed by contrasting high and low Youngs modulus metals to attenuate vibration. Weight can be reduced by bonding heavy, high-strength metals to lighter metals to improve strength-to-weight ratio, alter centers of gravity, or reduce payload weights in aerospace applications.
3. Make critical transitions with bonded dissimilar metals

In a recent project for Benchmark Space Systems, Atlas Technologies designed and manufactured niobium/stainless transition rings to connect stainless-steel rocket thruster heads to niobium alloy nozzles. These bimetallic transition rings sit at a critical junction in the system, managing the 2,000°F temperature differential within a span of less than 0.5". In gas and liquid delivery, stainless is effectively transitioned to aluminum tubing using bimetallic couplings to join pipes and tubes. In electrical applications, bonded aluminum/copper joints provide 100% contact with no oxide or corrosion build-up.
4. Reduce costs by using expensive materials only as needed and by improving manufacturability
Transition to lower cost metals where allowable. For corrosion resistance, expensive high-nickel alloy can be bonded to less expensive steel or aluminum for mechanical support. Metals difficult to weld or machine can be bonded to easily manufacturable metals. These transitions also support other economical manufacturing methods – such as extrusion, casting, or forming – by transitioning from metals that don’t lend themselves to these processes to those that can.
5. Improve design by adding specific metal properties to critical features
Bond hard metals to softer metals for robust performance. In Ultra High Vacuum (UHV), aluminum chambers are built with aluminum-stainless flanges. These flanges employ a stainless knife edge to crush a copper gasket that’s too hard for an aluminum knife edge to reliably crush. Or, use multi-metal transitions that maintain strength and ductility at pyrotechnic or cryogenic temperatures. The possibilities go on and on.
Atlas Technologies designs, develops, and manufactures bonded dissimilar metal products. Our standard and custom solutions are used extensively in aerospace, particle accelerators, cryogenics, and semiconductor manufacturing.
Learn more at AtlasUHV.com

Get curated news on YOUR industry.
Enter your email to receive our newsletters.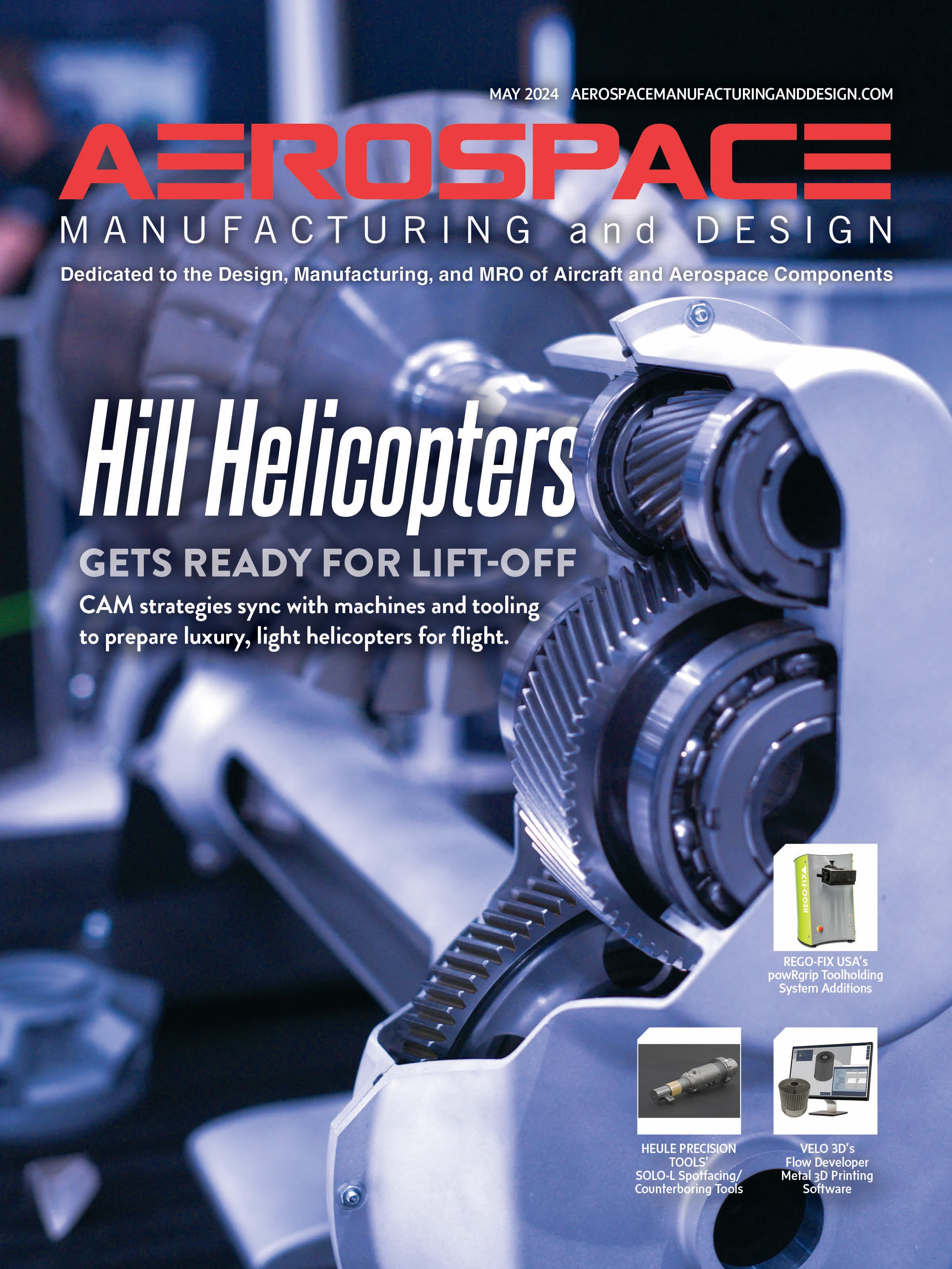
Explore the May 2024 Issue
Check out more from this issue and find your next story to read.
Latest from Aerospace Manufacturing and Design
- Trelleborg acquires Aero-Plastics
- Industrial automation products, enclosed encoders
- #61 - Manufacturing Matters: CMMC roll out: When do I need to comply?
- AIX shows aircraft interiors are a strategic priority for global airlines
- Machine Tool Builders Roundtable: Turn equipment into expertise
- No time to waste: How to machine MedTech parts more efficiently
- The 5 Best and Fastest Spindle Repair Services
- Mill smarter, not harder: How collaboration optimizes production