

1. Proper workholding can provide better results for your operation.
The right choice of workholding is one of the most important things behind the right choice of machine tools. If it’s not flexible, it’s not going to work for anybody. We look at what customers are purchasing for down the road. You might be making ammunition today and aerospace parts tomorrow, and having the flexibility in your machines and your workholding lets you do it. If you don’t have flexibility built into everything you do in your shop, you’re doing yourself a grave disservice.
2. Rotational and stationary workholding are trending
Electronics and electric workholding are the most exciting developments right now. Having predictable setups from your first job to your last job based on live feedback from your chuck through your machine tells you, “This is where my job position was, this is the clamping force I had, and this is the speed I was turning.” At that point all you must do is repeat that setup and you have predictable workholding.
3. Quick-change workholding can be incorporated into robotic machine applications
A part can become its own fixture because a zero-point system lets you screw a pin into the bottom of the part, and if you space everything correctly, you can use the part as a fixture. This does away with having to design a fixture that’s only good for one part or maybe a family of parts. It gives flexibility to automate across a broader spectrum of components. Our electric zero-point system has autosensing in the face just like our chucks.
4. Integrating intelligence (sensors, Ethernet communication) and electrification of workholding can improve efficiencies.
Once I do the first article inspection, I know I’m getting good parts. Within my tolerance, I now have predictable setups, so it allows me to be much more efficient and effective. It allows my production to be more predictable, because I know from the first part on, I can run that part all day long, all night long without anybody standing at the machine.
5. Sensoric/hybrid/ electric workholding offers advantages
After the first part is run, a robot can run parts automatically and autonomously. The robot opens a drawer, picks the parts, puts them on the machine, and it can run all night. We’re installing software allowing us to monitor that machine’s operation. We’re starting with one machine, then adding every machine in the shop because we see value in having predictable outcomes, and we can schedule more tightly because it allows you to predict how long the part’s going to run.
More info: smwautoblok.com/us/en
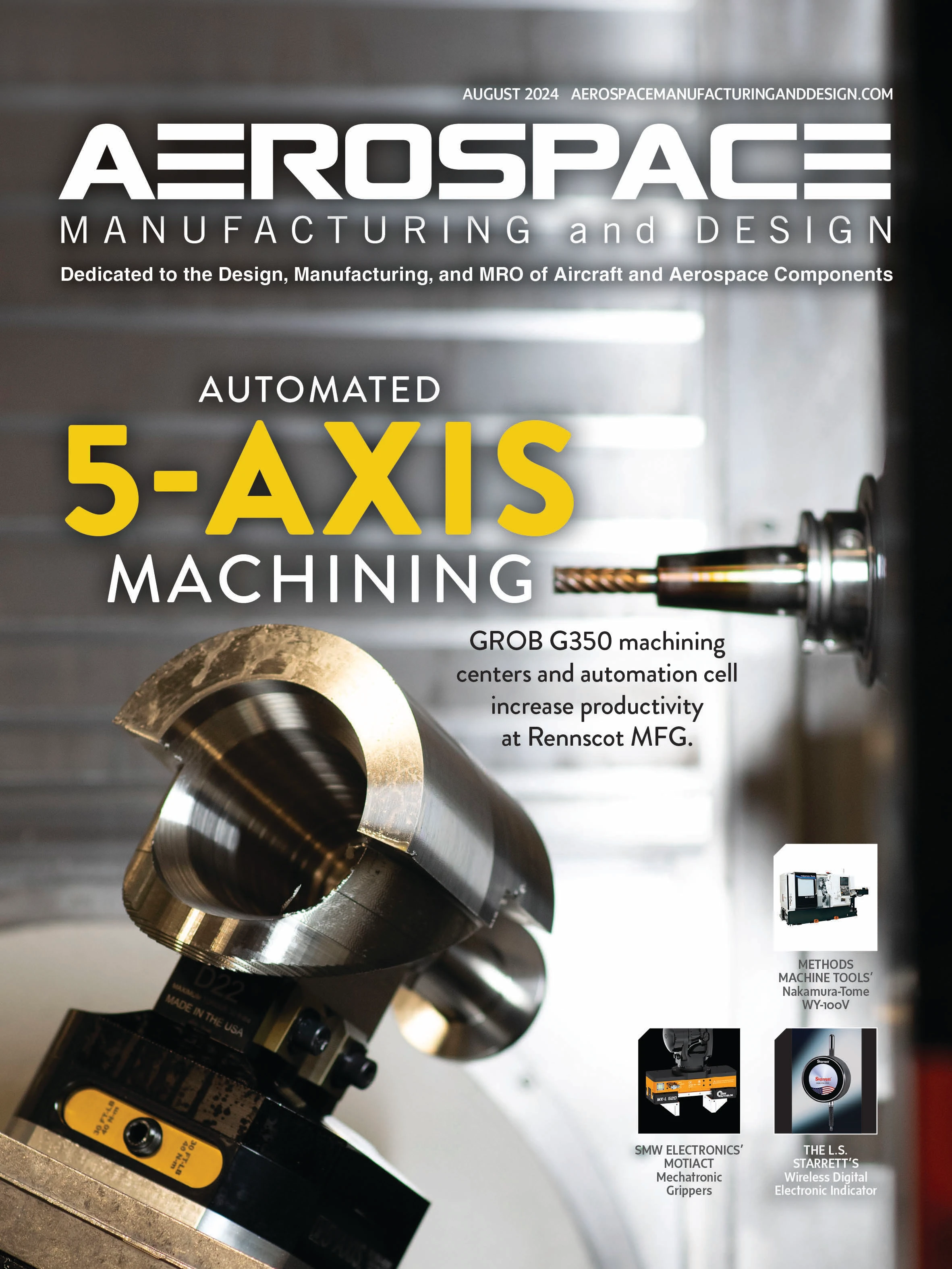
Explore the August 2024 Issue
Check out more from this issue and find your next story to read.
Latest from Aerospace Manufacturing and Design
- America Makes announces QTIME project call
- Innovation meets precision for 40% faster machining
- Upcoming webinar: Pro tips from a supply chain strategist
- Heart Aerospace relocates to Los Angeles
- Fixtureworks introduces Stablelock Clamps
- Piasecki acquires Kaman's KARGO UAV program
- PI Americas’ long-travel XY piezo nanopositioners-scanners
- AAMI project call submission deadline extended to May 12