
1) What do you consider “alternative” cutting tools/geometries to be?
TR: Mainly, I’m speaking of a way to modify or change the typical chip formation in a milling application. A few examples would be tools that approach the material with a shallow angle and small depth of cut (i.e., High Feed) or tools that segment (split) chips into small segments. A solid carbide end mill with a long flute length may have chip-splitting geometry to create smaller chip segments, making it easier to evacuate the chip while reducing power consumption. For tools using indexable inserts, advanced pressing and grinding techniques are used to create inserts with similar chip-splitting capability.
2) How does chip control affect milling?
TR: Chip control is a must. The main aspects of chip control are chip thickness and chip evacuation. The ability to maintain the correct average chip thickness is critical for process stability and productivity. Depending on the type of cutting tool (90°, 45°, etc.), the width and/or depth of cut can affect chip thickness and the shape of the chip (length and width of

3) You mentioned High Feed tooling. What is a High Feed tool and how does it differ from the typical milling tool?
TR: High Feed tooling uses an extremely shallow depth of cut when compared to conventional milling techniques/tooling. The main idea is to achieve high material removal rates at, you guessed it, high feed rates. This is made possible by the extreme lead-angle design, which creates a much thinner chip, we must compensate for this by increasing the feed rate. High Feed tooling functions at feed rates 10x to 12x higher than typical milling tools running at conventional cutting parameters.
4) What has changed in terms of carbide grades?

TR: Within the past year, Iscar has introduced a few new grades (IC882 & IC5820) for material groups of stainless steel and high-temperature alloys. The results have been 20% to 30% improvements, on average, over the old go-to grades typically applied in aerospace materials.
5) When should these tools be applied?
TR: In short, when there’s a lack of rigidity. The number one goal in any machining/milling process should be to create as rigid a scenario as possible. Of course, there are usually factors that force our hand and that reduce the rigidity of the milling process. A few examples of this would be deep cavities, tall and thin ribs, small corner radii/fillets, etc. This is when alternative cutting tools/geometries and proven programming techniques can be combined to keep productivity at a high level.
Iscar USA
https://www.iscarusa.com
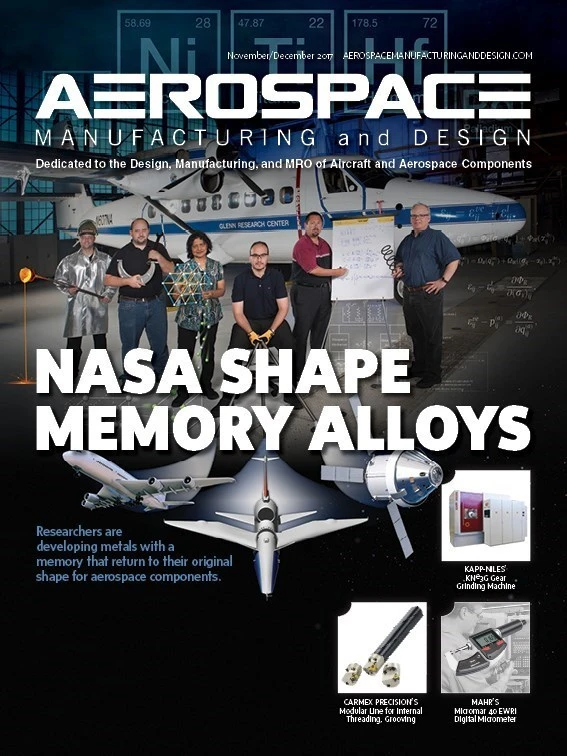
Explore the November December 2017 Issue
Check out more from this issue and find your next story to read.
Latest from Aerospace Manufacturing and Design
- AAMI project call submission deadline extended to May 12
- Jergens launches cast iron tooling column additions
- Airbus to acquire assets relating to its aircraft production from Spirit AeroSystems
- FANUC America's Cobot and Go web tool
- Chicago Innovation Days 2025: Shaping the future of manufacturing
- High-density DC/DC converters for mission-critical applications
- #59 - Manufacturing Matters: Additive manufacturing trends, innovations
- ACE at 150: A legacy of innovation and industry leadership